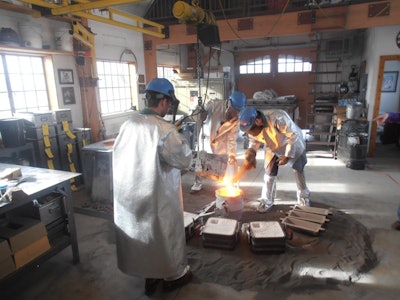
More than 30 designers and engineers went “back to college” to learn how Austempered Ductile Iron (ADI) could work in their manufacturing operations. The first ever AP University, hosted by Applied Process Inc. was held in January at Eastern Michigan University on the Livonia Campus and Joyworks Studio in Ann Arbor, MI. The program was so successful that plans are in the works for another session.
The three-day event was created to educate those who design engineered components on how to best utilize the opportunities provided by ductile iron and ADI. Curriculum covered a range of topics and was taught by industry professionals. Classes covered the casting process, castability studies, casting issues and resolutions, successful weldment to casting conversions, an introduction to ADI, Austempering 101, ADI applications in gearing and applications of casting conversions. Attendees toured the Applied Process plant and visited Joyworks, a metalworking studio focused on research and education owned by John R. Keough, Chairman of Applied Process.
“We are passionate about our products and processes,” explains Vasko Popovski, Director of Sales and Marketing for Applied Process. “In this economy, companies are facing the problem of cutting costs while still providing a quality product. We believe casting and ADI are the solution and brought industry leaders together to show them the added value, not only for them – but for their customers as well.”
Companies that choose to create products through castings can often cut down on production time and cost while offering their customers a product designed specifically for their needs. These products are often stronger than those modified through welding.
“The event was much more than expected,” explains Tim Covert, Senior Material Engineer at Ford Motor Company. “We deal with ADI, but I was new to casting design. I was impressed, not only by the process, but by the knowledge and professionalism shown by the Applied Process Staff.”
Austempering is an isothermal heat treatment that produces a structure that is stronger than those created by conventional heat treatments. ADI is a specialty heat-treated material that creates a lighter, stronger, quieter and more wear resistant part.
Bill Maenle, Engineer and Product Design at Unverferth Mfg., has dealt with ADI in the past. “Moving from welding to casting has allowed us more flexibility which means we can best cater to the needs of specific soil conditions. In my experience, ADI provides a better product with more reliability.”
Maenle was one of many in attendance whose company had previous experience and current applications in ADI. Other companies that were new to casting conversions sent representatives to gain a general knowledge. Many attendees who were new to ductile iron, more specifically ADI, left AP University with a knowledge base that will allow them to convert and improve current and future projects.
“I am a chemist by degree and knew little about heat treatments and metals three days ago,” admits Michael Schmidt, Business Manager at Pennsy. “As we move into metals I am confident we will find applications for ADI.”
Due to high demand Applied Process already has plans to hold its second AP University. Visit www.appliedprocess.com for information about attending the next AP University.