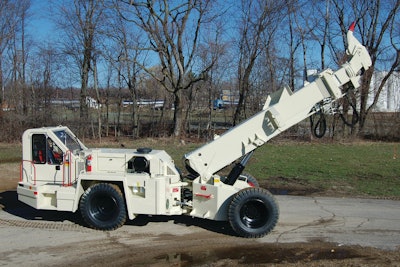
Custom car builders can put their best work into the engine and upholstery, but at a show most people won’t see beyond the paint. If the paint is thin, or thick and full of runs, the car is not going to bring home trophies. The same goes for off-highway equipment, although the job expected of paint in this industry goes beyond looking good and standing up to regular applications of wax. Show trophies give way to machine up-time and ROI. For off-highway equipment, the finish coat provides protection against the tough conditions in which the machines operate every day.
For more than 50 years, Getman Corp., Bangor, MI, has been supplying diesel-powered support vehicles for underground coal and hard rock mines. Products include the low-profile RDG-1504C Roadbuilder motor grader as well as tow tractors, pallet loaders, lube trucks, and scalers; the latter used to safely remove slabs of loose rock from the mine’s roof and face. Getman recently completed the first prototype in its Getman Transport series, a line of people movers that will eventually replace its existing TerraPro personnel carriers.
Mining can destroy even the best finish coat. “Whether it’s a coal mine in the United States or zinc mine in Australia, there are acids in the water that are found during the excavation of the ore body, and the machines are driven through it daily,” says Dana Getman, president of the company founded by his father. “Any machine that is imperfectly painted will have serious corrosion problems in a short amount of time.”
Then there’s the driving technique known as ribbing. “For some operators, if they can’t quite get around a corner,” says Getman, “they will hit the wall [known as a rib] because it helps them get the machine around the corner.”
Physically, Getman machines held up well, but there were challenges to be overcome with the painting process in Bangor. Improvements needed to be made in the amount of time required to fully dry, and how little time the coat held up to environmental conditions. Then, a customer’s comment hit home: “For years, we have thought it is important to emphasize the quality of our machines, including reliability and durability,” says Getman. “A U.S. coal miner came to visit the plant, and in the course of talking, he said I shouldn’t be overly satisfied with my painting process. I guess I knew that, but I never had anyone say it. The comment hastened the process to do something about our paint.”
Getman paints complete machines onsite in a single-stall paint booth, giving it the flexibility needed to build the custom machines required by the mines.
“Internally we were experiencing production issues with our final paint set up, which would take up to 12 hours to dry,” says Erik VanAllen, senior director of operations, Getman Corp. “After the finish coat was applied to the machine, it may have to sit there for a shift and a half. When production volume picked up, if we painted a truck in the morning, we couldn’t do any more painting until the next day. Everything staged outside, creating a significant bottle neck.”
While it was impossible to make all the hazards associated with the mine environment go away, VanAllen and Dana Getman knew they could do something to accelerate the production flow and improve how the product looked upon delivery, or when parked for a few weeks in a dealer’s lot. “We were considering a third shift or at least splitting the paint booth,” says VanAllen.
The company looked at other finishing options, including powder coating or installing larger ovens to bake the paint, but they were expensive. Some reduced the drying time, but not enough to justify the additional expense.
Take the call
Then VanAllen got a call from David Keller, national sales manager for Baril Coatings USA, Angola, IN. He had some interesting things to say about Baril’s Dual Cure Chemistry (DCC) product.
“Whenever I discuss DCC paint with a potential customer,” says Keller, “I can either talk production benefits, because it dries fast with no heat curing required, or I can cover its increased corrosion protection and color retention. The end-user gets a better-looking product, and the plant gets product moving through faster.”
Achieving a better finish coat was important, but it was the lightning-fast dry times that, to VanAllen, sounded too good to be true: Keller said 29 minutes, and during a meeting in Bangor, Keller proved it.
“Typically, whenever a paint salesman talks about increased corrosion protection, we have to talk about putting an oven in, increasing temperatures, and delaying dry times. DCC actually speeds up the production process,” says Keller.
Baril’s DCC paint has two forms of curing. One is a chemical cure — mixing part A with part B — and the other uses moisture from the atmosphere. Coupled together, it achieves the fast dry-to-handle time.
Baril Coatings is headquartered in the city of ‘s-Hertogenbosch in the Netherlands. Founded in 1982, Baril produces coatings for a variety of applications and has manufacturing and distribution operations in Eastern Europe, Jordan, China, England and the United States. The patented DCC coating has been on the market for seven years.
If 29 minutes is too long, Keller says there are some extremely fast curing versions. The product is customizable based on curing requirements, and there are several primer options. The product is VOC compliant, and there are no hazardous air pollutants (HAPs).
Keller worked with Getman, which switched over to Baril’s 604 UniBar IsoPrimer DCC and 174i2 PoluRan i2 top coat. The top coat provides thin film protection at up to two mils, although Getman applies the paint a little thicker.
Getman is also able to use its existing spray booth and saves money because heat isn’t required.
The DCC paint requires plural component paint equipment, because the product has a short pot life. “With our previous paint operation, we didn’t use an integrated paint mixing system, so we bought new equipment for the DCC paint and trained our folks,” says VanAllen.
“After we got the equipment up and running we were getting nice coverage quickly. The learning curve was that our guys were used to painting something that took a long time to dry, so they could fix a run hours later. Now they have to be diligent in the way they apply it the first time.”
VanAllen prefers to be very careful with the finish coat, and will keep a freshly painted machine parked for two and a half hours. With its fast dry-to-handle time, however, it means the machine could be moved out of the paint bay and another one moved in to be painted.
Baril worked closely with Getman to make the switch. “We worked with David Keller, who not only taught us a great deal about paint, but also helped us acquire the right equipment,” says VanAllen. “He was motivated to make sure this paint was effective for us, and was very hands-on. We benefitted from that relationship.”
New personnel line
Getman Corp. acquired the TerraPro line of personnel carriers a few years ago. With a height of 70 in. and width of 90 in., the 7090 TerraPro can carry up to 12 miners comfortably. Its galvanized body and chassis resists corrosion and looks tough.
“The galvanized body is different,” says Dana Getman. “That helped the image of the product, as it just looks muscular.”
But coating such a large assembly was an imperfect process. It was difficult and expensive. “And it added a lot of cost to the product,” says Getman. “We had to build the frame and body here, send it out to be dipped, bring it back and clean it up. The dipping process actually warps the panels, which caused problems during assembly.”
The switch to the Baril product came at a good time for a new line of Getman-designed personnel carriers known as Getman Transport (GT). “When we went to the new model, we wanted to get away from the galvanized body,” says Getman.
Completed this summer, the first prototype is currently undergoing testing before it is shipped to a mine in Indonesia. Getman says 66% of the components are shared with the proven TerraPro product. Differences include the frame, hydraulic steering and four-wheel-drive, a system that enables crab steering and a tight turning radius. The prototype has been named the GT 12, as it seats 12 on three bench seats. The design is scalable, including fewer seats and a truck bed.
Looking good
It’s been a year since Getman Corp. switched over to Baril Coatings’ DCC product. “Our axles come out of the paint booth, painted black, and they really look good. I still think it is beautiful,” says VanAllen. “I think the quality of our paint, and the appearance of our products, is much nicer.”
The machines are looking good after they leave Bangor, too. When a machine leaves the factory in southwest Michigan, it will spend days on the rail, in sea ports, and on ocean-going ships. “After five to six days of that salty air, there was already oxidation occurring with our old system,” says Getman. “You don’t see that with this paint process.”