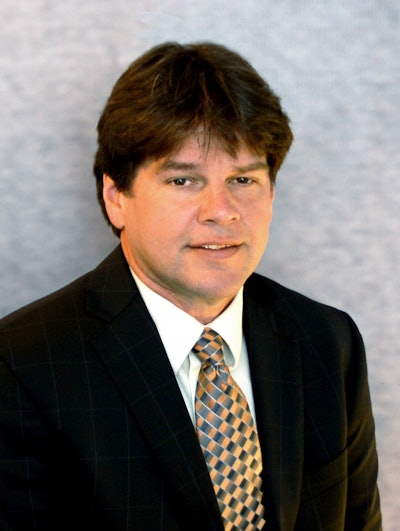
Responses from Frederick J. Ross, CD-adapco Director, Ground Transportation
Technologies of the Future: Hybrids, Electrification and Smart Systems
Have there been any recent advancements in hybrid technology which will help, or have the potential to, further increase their prevalence in the heavy-duty equipment industry?
Our technology allows design engineers to optimize and build more efficient hybrid technology, on an individual component and full system level. Put simply, our technology helps OEMs and suppliers to discover better hybrid designs faster by building a “digital twin” of a proposed vehicle that can be used to test its performance under real-world operating conditions, ultimately reducing both emissions and fuel consumption.
In regards to hybrids, what technological limitations currently exist that are impeding the ability to harness the full potential of hybrid power?
There are not any real technological limitations, except if you get a full-electric vehicle. In that case, it becomes battery storage and recharge time. The main limitation of hybrid systems includes the additional costs for hardware needed for a secondary electric system, and then to fully optimize the control systems to make sure all systems work efficiently together.
What progress is being made by your company and/or the industry in regards to developing fully optimized systems as opposed to individual components [e.g. overall powertrain optimization versus optimizing the drivetrain and engine separately]?
CD-adapco was recently acquired by Siemens. Siemens currently has tools to examine system performance, and help optimize controls. CD-adapco adds on 3D flow/thermal and stress to help evaluate design at different operating points. Combining both products together enables us to look at thermal stress in the powertrain/drivetrain over long drive cycles. This helps reduce costs for design of hybrid systems while increasing reliability and efficiency of the system.
What role is electrification and smart systems playing within your company’s product designs?
Hybrid/electric vehicles are important parts of future design to reduce ICE emissions/fuel consumption. Having simulation tools to address the battery design, or electric motor design, and look at the thermal environment, helps us work with clients to discover better designs, faster and more cost effectively.
It is our goal to be able to make a “digital twin” of the hybrid vehicle to enable simulation in a virtual environment. Making building first prototype, and first tests to be more of a verification/validation step.
How has or will the use of prognostics and predictive technologies continue to progress within your product designs, and the industry as a whole?
Prognostic and predictive technologies are at the early stage of impacting design. The automotive companies are furthest along in this area. The use of CAD software, moving into the digital world, and creating a digital twin allows for components to be tested in a virtual environment, either simulating real world operating conditions, or test conditions. This helps reduce turnaround time, costs, and helps build better designs, faster. This allows engineers to evaluate many design evaluations before the first prototype has been built.
What’s next on the technology horizon? Are there emerging technologies which will affect your products or the industry as a whole? How will hybridization, electrification and smart systems continue to progress within the next year and on into the future?
The first step is the merging of technology to move vehicles from the CAD environment to the “digital twin” to enable virtual vehicle design. This is moving existing tools into the mainstream of our clients. Once components are designed, using the digital twin, 3D printers can then save time on manufacturing, further reducing time to design, and build a new hybrid vehicle.
Challenges on the Horizon
What new challenges have arisen that affect the way your company designs or manufactures its products? How it does business? How it goes to market? How it differentiates itself from the competition?
The new challenge is moving from looking at 3D simulation to also include system simulations for complete design process. Clients are looking to develop a full virtual vehicle, using digital sign-off before they start building first prototype. For complex vehicles, this can have thousands of different tests which are normally done in a test environment that now needs to be done in a virtual environment. STAR-CCM+ provides great range of automation today which allows for these systems to be built quickly, and enables design space exploration. With multidisciplinary simulation co-simulation, our clients can use design exploration to look at trade off in design while simulating real world operating conditions. Our automation tools, design exploration, and advanced physics are much more robust than our competitors.
What new challenges do you see the industry as a whole facing, and how is your company looking to address/provide solutions with which to solve those challenges?
The biggest challenge when simulating real-world conditions is the computational effort needed to calculate long thermal transients (90-plus minutes). Typical simulations can run for days to hours, depending on the level of detail being investigated. A lot of our efforts are spent finding methods to accurately predict real world events, but minimizing computer efforts.
Some methods we are working on to solve these issues are to improve scalability on large process counts. We also have licensing which enables customers to run on thousands of cores with no additional cost. There are also methods of co-simulation between fluids/solids, so we can use the time domain most efficient for the physics needed. The third area is to add advanced multi-phase physics to help reduce computational costs. That includes finding efficient ways to model the impact of water particles onto surfaces to forming puddles on the vehicle, for example.
Has the rate of technological advancement (such as the rapid emergence of data products) had any impact on business decisions, development, or product performance and client expectations?
The biggest impact is the increase of computational power available to our customers that can really enable digital design. The computer power becomes a lot less expensive than building a physical prototype. It then enables our client to look at design space exploration, and discover better designs, faster.