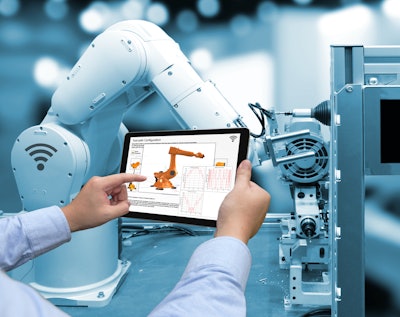
The complexity of vehicle and system designs has been growing for several years and seems to be accelerating. New technologies are always emerging thanks to processes like additive manufacturing (3D printing) and regulatory changes. The Industrial Internet of Things (IIoT) is also ushering in a new era of connected systems, causing system and vehicle designers to take a step back and reevaluate design from its inception, and not just as a new iteration of a previous design.
The goal for software developers is simple: Enable engineers to leverage a simulation tool's capabilities early on and throughout the development phase as comprehensively as possible. Maplesoft
Engineers are looking to address a multitude of issues, be it incorporating sensor technology, image processing capabilities, applying artificial intelligence (AI) and deep learning algorithms, or being able to test a high number of scenarios and driving conditions in a safe lab environment. They want more design iterations in less time, all while handling large volumes of data in an in-vehicle computing or lab infrastructure. Additionally, vehicle software must be safely and remotely updated in a secure computing environment. All of these challenges and more are being addressed by software engineers.
“There are a lot of exciting things happening now in engineering simulation,” says Arnold Free, Chief Commercial Officer at CM Labs Simulations Inc. “The need to perform millions, if not billions, of hours of testing during the design of automated systems requires faster-than-real-time, cloud-based simulation engines that can deliver the performance needed. Simulations can now be connected in real time to provide a complete system-level simulation of mechanical dynamics, contact, sensors such as LIDAR and operations modeling. This can be combined with power-systems models, [and] hydraulics models to create a complete system-level virtual twin.” See the sidebar below to learn more about The Digital Twin.
Regardless of the type of software – be it for designing, testing or controlling a vehicle system – the software involved is expected to take on more processing power than ever before, with no signs of reversing or slowing down. “Software gets bigger; it takes more lines of code, is harder to test and harder to validate,” explains Laurent Bernardin, Chief Scientist and COO at Maplesoft.
“Take the powertrain system, for example. A hybrid or electric powertrain has way more system complexity than compared to an internal combustion (IC) engine,” says Bernardin. “That complexity translates to the software, as it has more variables and parameters to manage.” On an electric hybrid powertrain, for example, the valve timing for the IC engine is controlled, but now also when the electric motor needs to kick on, and when the IC engine has to start recharging the battery versus powering the wheels.
Maplesoft’s model predictive control (MPC) technique, for example, can be used to represent the behavior of these complex systems. “The control software would contain a model of the entire powertrain. The software can predict the pending acceleration needs, a turn coming up, and the current charge of the battery, and run a future simulation to determine the most efficient set of parameters for the best possible path for controlling the powertrain,” explains Bernardin.
The code can be generated automatically and efficiently, which is important for running control software in real time. “For the powertrain, the software is embedded in the engine model and the results need to be immediate. With rising complexity in models, it’s incredibly important that the code generates quickly. The faster it is, the more complexity that can be allowed,” says Bernardin.
Mahendra Muli, Director of Marketing and New Business Development at dSPACE Inc. agrees. “The volume and complexity of embedded software in vehicles has grown significantly.
“For the electrification market, we have solutions to develop and test electrified powertrain components like batteries, motors, and charging systems. There are many innovations coming to the market from new wide-bandgap switching devices, battery management systems, and motors, as well as new [renewable] energy sources requiring smart control of grids,” Muli says.
CM Labs Simulations Inc.
The company has introduced hardware platforms for controls prototyping, as well as solutions for hardware-in-the-loop testing of radar, LIDAR, and camera-based systems which incorporate the effects of lighting and sensor types within the simulation. “Additionally, we are supporting increasing the bandwidth of test systems by enabling simulation and testing by using a high-performance computing infrastructure,” says Muli.
The heavy-duty vehicle space is becoming increasingly complex. Enhanced machine features like prognostic maintenance through predictive analytics, varying degrees of automation and operator assistance, and enhanced performance expectations via machine learning systems all require more advanced engineering software and expertise.
Beyond that, companies like Integrated Test & Measurement (ITM) are seeing its design engineer customers expect to get real world data immediately with little effort or cost. “With that in mind, we have tried to move toward making our solutions network based and easily accessible,” says Mark Yeager, Software Manager, Integrated Test & Measurement.
Easy accessibility requires more online searchable data management. ITM is working to make its data more searchable by embedding statistics within the files and adding this data to online databases. In the future, ITM’s Yeager expects software products to be simple, online and with mobile device tools.