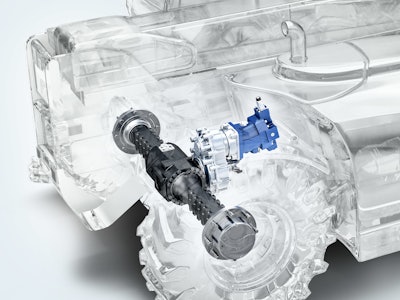
With the new function modules from Bosch Rexroth, vehicle manufacturers achieve considerably lower costs during the integration and application of hydrostatic travel drives. The modules combine innovative functions with standardized safety features. In addition, Rexroth developers have examined all of the module components and their interactions with each other to further improve robustness.
During the engineering and design configuration of hydrostatic travel drives, vehicle manufacturers have to comply with the applicable Machinery Directives as soon as they plan to market construction machinery in Europe. Bosch Rexroth assists in reducing the cost for manufacturers, as the company has already carried out risk analyses according to relevant standards for an entire range of software function models, and have thereby determined the required Performance Level b and c, and the C standards applicable for the application. The standard hardware and software configuration of the function modules fulfills this Performance Level. Hydrostatic travel drives control with standard safety functions is integrated into the DRC travel drive software. Vehicle manufacturers can equip their wheeled loaders or telehandlers with innovative drive solutions with reduced engineering costs. The “2+1” travel drive module thereby ensures a reduction in fuel consumption of up to 20% without tractive-effort interruption during operation. The diesel engine with a power output of up to 130 kW drives an axial piston pump, which is connected to a variable motor and a fixed motor. The driving speed range changes automatically and travel speeds of up to 40 km/h can be achieved. The software integrated into the control unit prevents loss of tractive-effort and thereby noticeably improves comfort for the operator. This function module is suitable for construction and agricultural machinery with an operating weight of 6-16 tons and tractive forces of up to 120 kN.
The Shift on Fly function also fulfills the functional safety requirements according to DIN EN ISO 13849 and controls manual and automatic shifting of the gearbox. Rexroth has incorporated an optimized shifting strategy into the software, which enables safe gearbox shifting in different driving situations. Short, synchronized shifting operations increase comfort. In addition, it ensures additional driving and comfort functions that are adapted to the system. The function module with hydraulic pump, hydraulic motor, control unit with software, coupled with a gearbox, enables increased efficiency for the entire drive. Both “2+1” and Shift on Fly cover a wide power variation through different combinations of various pump and motor sizes.
Additionally, with the innovative Hydraulic Start-Stop (HSS) function, Bosch Rexroth supports manufacturers of compact construction machinery and wheeled loaders in the reduction of noise emissions. The function module automatically switches off the diesel engine during standstill phases and automatically starts it again when required using previously saved hydraulic energy. The torque required is therefore immediately available. The solution consists of an axial piston variable pump, a valve block, a compact accumulator and a BODAS control unit with preprogrammed software.