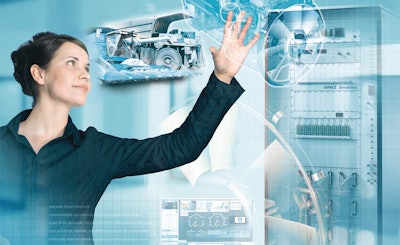
Hardware-in-the-Loop simulation is an integral part of the vehicle development process and is critical to verifying the correct behavior of distributed functions, integrated systems and communications between electronic control units (ECUs). The dSPACE Simulator HIL testing improves ECU software quality.
- Hardware-in-the-loop simulation avoids recall campaigns and loss of corporate image
- Fewer prototypes, fewer test drives, lower costs
- More comprehensive and more systematic tests in a shorter time
- Higher quality, lower risks
- Start of production on schedule using fewer resources
HIL simulation is an integral part of the vehicle development process and is critical to verifying the correct behavior of distributed functions, integrated systems and communications between electronic control units (ECUs).
dSPACE simulators are ideal for function and component tests, system tests, ECU network tests, test benches and regression tests. Simulators are used for all vehicle domains including off-highway, light truck and heavy-duty trucks, and for virtually any application: vehicle dynamics, diesel, transmission, gasoline, driver assistance systems, body electronics, multimedia / infortainment, etc.
Our hardware is scalable from small to large systems. Tailor-made hardware and software solutions available. Integrated signal conditioning, electrical failure simulation and engineering for customer applications also offered.
Why Test ECUs with Hardware-in-the-Loop Simulation?
As software explodes in complexity and size, comprehensive embedded electronics tests are necessary more than ever before. Only a tough zero-error policy can help avoid vehicle recall campaigns. So for many commercial vehicle manufacturers and suppliers, ECU testing has become a key phase in the development process. However, real test drives are expensive. You also have to contend with the necessary vehicle prototypes not being ready on time, so testing is delayed. Simultaneous engineering, in which development processes run in parallel, can be difficult to achieve. These are just a few of the problems inherent in real test drives. Not only are the drives themselves dependent on the weather and on vehicle prototypes; test engineers have to cope with incomplete test results – not to mention the immense costs in terms of time and money. The solution: virtual test drives within a hardware-in-the-loop simulation environment.
Virtual Test Drives
Almost all commercial vehicle manufacturers and their suppliers are now using hardware-in-the-loop simulation. Instead of being connected to a real vehicle for testing, ECUs are connected to a simulator. Virtual test drives can be made long before the first vehicle prototype is available, resulting in enormous savings in cost and time. Moreover, a simulator can handle test drives outside the range of what real vehicles can do, and the tests are reproducible and automatable (lights-out testing). A real vehicle is then used for final testing.
Virtual test drives are an immense task for a simulator, which has to handle a complex system model such as the engine or even the entire vehicle. Real-time capability is mandatory. The sensor signals that need generating are unbelievably complex, and simulating them is another major challenge. dSPACE has years of accumulated know-how in developing simulators, and can give you excellent solutions for all these exacting requirements.
Testing with dSPACE Simulator – for Quality and Efficiency
Hardware-in-the-loop (HIL) simulators with dSPACE technology are in use worldwide. dSPACE Simulator is the key enabler for testing embedded electronics fast, automatically, and efficiently.