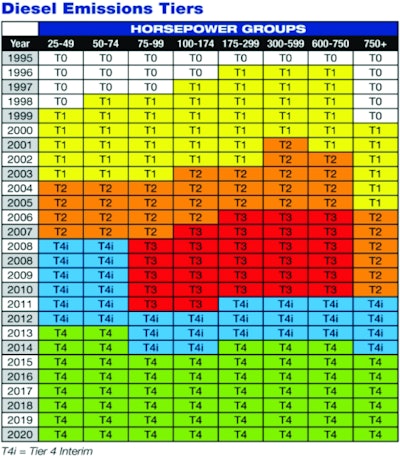
In this highly-connected, app-driven mobile technology world, it’s easy to see why joystick controls and telematics get all the attention as being the next coolest thing. But let’s not forget that the heart of most construction equipment is the diesel engine and based on its current performance and future prospects is pretty cool in its own right.
With growing concern about air pollution, a little over a dozen years ago, air quality regulators and diesel engine manufacturers came together and developed consensus on levels and timeframes for lowering emissions, and a new diesel fuel formulation necessary to meet the challenge of near zero emissions for a diesel engine.
At the outset, getting diesel to near-zero emissions was by no means a sure thing. Today it is clear that the advances in engine combustion, fuel injection, turbocharging and engine control systems and new emissions control options using reformulated and low-sulfur diesel fuels were indeed the right formula. Highway engines came first, with the 2007 standards roughly equivalent to the Tier 4 interim off-highway standard and the 2010 highway standard roughly equivalent to Tier 4 final emissions levels. The destination is the same (near–zero emissions) but the off-road sector is doing it faster—in only six years compared to 10 years for the highway world. The fundamentals of near-zero emissions are the same but the complexities and thousands of machine and operating variables for off-highway engines were the basis for the extended phase in period for off-road engine standards (2008-2014).
Now that we’re in the midst of the Tier 4 transition, how is it going?
Adoption of Tier 4 machines has been tempered by the economic recession; early returns are positive on satisfaction. With demand for construction down and now being slower to recover, the population of Tier 4 machines is still relatively small, but picking up. Manufacturers have done a rather good job of preparing their customers for the dawn of new EPA emissions standards and Tier 4 strategies. And while equipment owners see value in low-emissions engines, they are really looking for returns in performance, fuel efficiency and productivity as the main measure of the new higher-priced machines. Manufacturer claims of 2 to 10% savings in operating costs seem to be bearing out, but time will tell how the new technologies fare on maintenance and durability.
Clean engine emissions demand cleaner fuels, oils and new fluids: Ultra-Low sulfur fuel and Low Ash Oils now standard fare. To meet the very low emissions standards requires first and foremost ultra-low sulfur diesel fuel as the standard. Until 2014 there are still some very narrow and limited phase-in allowances for some small refiners supplying diesel for non-road, locomotive and marine use to continue to sell diesel fuel with 500 ppm sulfur, so in some sense old, higher sulfur diesel fuel could still be around in some applications. But with new Tier 4 technology, the cleanliness of the fuel becomes much more important with tolerances of 2 micrometers and filtration at the 3 micrometer level. Low-ash oil is also the new-normal for most OEMs, owing to meeting near-zero PM levels and the ability to use various catalysts and trap technologies. And for equipment using selective catalytic reduction (SCR), you’ll become familiar with the care and feeding of the new diesel exhaust fluid (DEF) system, the location of the blue filler cap and the need to have a quality supply of DEF available on the jobsite every time you fill your diesel fuel tank.
One size doesn’t fit all. Tier 4 emissions technology is the quintessential example of the “one-size doesn’t fit all” axiom, and is more defined by the levels of emissions achieved than the technology deployed to get there. As Tier 4i and Tier 4f pathways come into focus across the many engine and equipment makers, you realize that not all manufacturers are using aftertreatment systems, particulate filters or catalysts to achieve near-zero PM levels, and not all manufacturers are using SCR to achieve very low NOx levels. Many are using refined exhaust gas recirculation (EGR) as part of their emissions control strategy. Particulate trap technology does not scale well to very large and higher horsepower engines, so you’ll find many of those without the PM filters now standard on most highway vehicles and smaller construction machines.
New systems, fluids and operator training required. The new SCR-based emissions control systems have introduced new active warning and indicator systems on the dashboard that have caused some early confusion and highlighted the need for more attention to operator training. For example, indicator lights may signal an active particulate filters regeneration event meaning that the machine is automatically going into a regeneration mode because temperature and operating conditions are optimal. In some instances, there may be options for operator manual input to temporarily override regeneration for certain operating conditions. There have been instances of uninformed operators pressing buttons and lights on the dash simply because they came on, which then put the machine into an override or manual mode, delaying regeneration events. New dash warning systems are also in place to designate the levels and need for refilling diesel exhaust fluid (DEF) in machines that use SCR technology. For machines using this technology, high-quality DEF must be assured and replenished to ultimately assure continuing operations; typically on a 1:1 ratio based on the size of the machine’s fuel tank.
Different look, feel and sound. While some manufacturers have managed to place emissions control systems like SCR into the current muffler size envelope, other models may have a slight bulge in engine housing or new canisters have appeared, along with plenty of new pipes and control technology that are tucked away in the engine compartments. One interesting comment heard about the new Tier 4 machines is that they are quieter, perhaps due to both in-engine technology as well as after-treatment systems that may provide additional sound-deadening functions. Improved engine performance at high-altitudes without de-rating is also an advantage of some of the new engine technology and advanced turbo-charging that is now standard fare.
Tier 4 technology costs more. Meeting the Tier 4 requirements has meant billions of dollars in engineering and research investments, some highly visible in the form of new hardware and design and some less visible—in the internal combustion design and management ( ECM) systems. Some of these costs are reflected in the higher price for equipment—ranging from 10 to as high as 15% more on some models. Higher costs for ULSD are also an added feature of the new clean diesel system; one which operators are now well accustomed.
Tier 4 technology suitability for all markets. Manufacturers today produce products at varying “tier levels” to serve specific country and customer needs. Tier 4 generation technology requires the use of ultra-low sulfur diesel fuel, however in many instances, ultra-low sulfur diesel fuel is unavailable in developing countries whose emissions standards are also less stringent than the US.
Given the advanced nature of the new clean diesel systems the concept of altering Tier 4 level technology to allow more emissions for use raises immediate concerns from both a regulatory and legal compliance perspective and also a technology and engineering perspective. Engine OEMs certify their engines with EPA and affix a label that serves to legally validate that engine and its emissions certification status, which was done with all parts intact. Engines and emissions technology now operate as one system with complex electronics and feedback controls, so alterations, bypasses or physical modifications to emissions control systems would result in operational and performance problems. In the US, changing any one of those emissions control-related parts or using improper fuel is prohibited by regulation and may subject the violator to prosecution for tampering under the Clean Air Act, punishable by fines of up to $37,500 per day per occurrence.
However, at least one manufacturer has recently announced the availability of a kit to enable dealers under very controlled circumstances to recalibrate Tier 4 engines to work in countries without ULSD and address labeling and compliance issues.
What’s next for diesel equipment technology and emissions?
There are clean air and emissions considerations on the horizon for both new and existing off-road equipment. On the existing equipment/retrofit front, EPA has been quietly rolling out a new national strategy for its national clean diesel campaign (NCDC). This NCDC is the source of grant awards via the Diesel Emissions Reduction Act (DERA) funding for retrofitting and repowering diesel equipment. The FY 2012 grant awards are expected beginning in late August, but the new strategy for awarding projects provides a glimpse into the future where a much higher emphasis is placed on priority areas that are designated particulate matter non-attainment or transitional areas, and/or areas with higher concentrations of diesel particulate emissions according to various EPA clean air databases. EPA’s just-proposed more stringent national ambient air quality standard for particulate matter along with a growing interest in reducing black carbon (“soot”) emissions as a short-term climate forcing agent may result in further action by states and localities in the future to pursue in-use emissions and operational requirements on off-road engines and equipment to reduce PM levels as part of their attainment strategy.
“Green highway construction” requirements that would have required diesel engines meet certain emissions performance standards in federal highway and infrastructure construction with a set aside of 1% of project funds for retrofitting, were ultimately excluded from the recently passed Senate Highway legislation now awaiting Presidential signature. Note that this will not preclude individual projects and states from establishing contractor equipment performance requirements for diesel engine emissions and equipment as part of bid considerations and project awards.
On the new technology front, while it is hard to envision further reductions in the U.S. diesel engine emissions standards that already have PM and NOx emissions near-zero, the latest emissions discussion is being driven outside the U.S. by European interests in what could amount to a “Tier 5” standard that would add a limit on the number of allowable particles in the exhaust in addition to the mass of the particles which is regulated today. A number-based standard is most challenged today by lack of reliable measurement technologies, and could force further changes in particulate emissions control systems as well as engine combustion.
But the more serious emissions conversation now is around lowering emissions of greenhouse gas emissions like carbon dioxide (CO2). Highway commercial trucks are gearing up for meeting new U.S. EPA and DOT mandatory standards for fuel efficiency and CO2 emission standards starting in 2014. For its part, the vastly different off-road equipment sector will achieve efficiency and lower fuel consumption through two main approaches; machine and engine technology and operating productivity. Further efficiency gains are likely from the diesel engine, thanks to further combustion refinements and as second generation emissions control systems like SCR become more optimized. On the machine side, expect to see increased use of hybridization coupled with engine downsizing. As electric motors and energy storage technology become more widespread and lower cost, more hybrid and electric-drive technologies like those currently available from Caterpillar (dozer) Deere and Volvo (wheel loaders) are likely. And the use of lower-carbon fuels like advanced renewable diesel and biodiesel are probably coming on a more consistent, widespread basis in the future; we just don’t know when.
Finally, there is great potential for fuel and emissions savings of the machine at the jobsite. Telematics and precision operator controls and machine-to-machine communications are technologies increasingly proving their value at delivering productivity gains as well as fuel savings and lower emissions with more set for the future.
Just don’t forget that the joystick is connected to a clean diesel engine!