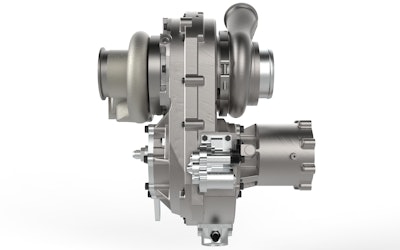
The SuperTurbo for Class 4 through Class 8 trucks and heavy-duty mobile equipment includes three technologies in one: superchargers, turbochargers and turbo-compounders. During a recent conversation, Mark Herbst, CEO, and Tom Waldron, executive vice president, shared more information about this technology that is currently undergoing the design validation process (DVP). It is slated to enter pilot production programs sometime during 2023 and 2024.
Tell us about the SuperTurbo: What it is and how is it different from other engine boosting devices on the market?
Tom Waldron: The SuperTurbo is a mechanically driven turbocharger. It is capable of exchanging power to and from the engine crankshaft and, effectively is an on-demand boost device. The SuperTurbo gives an engine the exact amount of air it wants wherever and whenever it wants it. The different functions the SuperTurbo provides is found in superchargers, turbochargers and turbo-compounders. However, the SuperTurbo can provide the same functionality of these three devices in one package.
Tom Waldron, executive vice presidentSuperTurbo Technologies
When a vehicle is at highway cruise or higher power operating conditions, the power from our turbine will exceed the compressor power needed which allows us to put the excess power back into the engine crankshaft. This process results in an improvement in fuel efficiency and reduction of carbon dioxide (CO2) emissions. This process is commonly referred to as turbo-compounding.
This booster or turbocharge is automatic and not a manual operation?
Tom Waldron: The way that the system functions is that the engine tells the SuperTurbo how much air it wants which is commonly known as a boost signal. The SuperTurbo reacts to the boost signal by changing the speed of the compressor to provide exactly how much air the engine requires. Like variable geometry turbos, they answer requests from the engine for their vane position. Engines making requests from their boosting systems or their electric, directly actuated waste gates is not uncommon. Other types of boosting systems do this. However, what the SuperTurbo offers is a precise and rapid response and error-free management for the engine.
Why did SuperTurbo Technologies and Linamar Corporation decide to partner and bring this technology to market? Why was the partnership needed?
Mark Herbst: Our primary focus at SuperTurbo is on developing the technology, preparing the design for commercialization and engaging with the commercial vehicle engine original equipment manufacturers (OEMs). We never planned to produce the SuperTurbo ourselves.
Over the years, we have been evaluating who the potential manufacturing partners could be. We have considered other turbocharger manufacturers, for example, or other suppliers to the automotive industry.
Mark Herbst, CEOSuperTurbo Technologies
However, Linamar is well positioned to migrate the SuperTurbo from low volume prototypes to high volume. Their innovation hubs operated under the name McLaren Engineering can produce SuperTurbo prototypes and develop the assembly process, tooling and test programs that can eventually be transferred to Linamar high-volume manufacturing facilities in different regions of the world. We work with the McLaren facility in Livonia, Michigan. Since the beginning of this 2022, this facility started assembling SuperTurbos based on the assembly process we provided in 2021. Their team has been determining how to improve the process and developing tooling, fixtures and programs to facilitate the migration to higher volume production.
At the Livonia facility, the team can produce up to 8,000 to 10,000 units per year. Then when the requirement to increase arises, we can transfer to one of their lower cost higher volume facilities, typically outside the U.S. The Linamar team is a good fit because of its core competencies and capacity to move from low- to high-volume production.
With the low-volume production, they work out any issues and build efficiencies into the production. Once that is done, they move it to a higher volume production facility?
Mark Herbst: That's correct. We started working with the Linamar team in August 2021 when we provided them our documented assembly process. They built several SuperTurbos with us in Colorado in November and since then have been optimizing the assembly process at their facility in Livonia. The Linamar team brings extensive experience of building prototypes to then migrate to high-volume assembly. They know how to develop assembly and testing processes to control quality, decrease costs and remove inefficiencies. They will play a significant role in our success.
The press release about this new product stated that the sale of the SuperTurbo was contingent upon testing with Linamar. Is there more testing to be done, or is the testing complete?
Mark Herbst: We engaged with AVL in April 2021 to oversee the DVP. AVL is well-known in the automotive industry and recognized as a leader in providing design, engineering and testing services. AVL collaborated with us for more than eight months to evaluate the SuperTurbo design as compared to the durability objectives for the device. AVL then developed a series of tests that will take place on electric rigs and engine dynos to validate the durability of the SuperTurbo. These tests began in early 2022 and will be completed sometime during Q1’23. The tests are being conducted in the SuperTurbo’s dyno cells in Colorado and at the Linamar/McLaren facility in Livonia. Successfully completing these tests will provide confidence to the industry that the SuperTurbo will meet automotive industry requirements.
Are you doing any field testing with OEMs right now?
Mark Herbst: We have successfully completed many different tests with OEMs in their engine dyno cells to validate the value that the SuperTurbo brings to their engines. These tests have been focused on validating the functionality of the SuperTurbo and the improvements it makes to the OEM’s engine. Most of these tests are conducted under strict non-disclosure agreements with the OEMs, preventing us from making public announcements of our work with them. We have previously publicly announced that we are working with Caterpillar on a program in Peoria. Passing this durability test will give OEMs the confidence that SuperTurbo is ready for a pilot program and can be slotted for high-volume production.
Can you give us some specific applications for the SuperTurbo?
A different view of the SuperTurboSuperTurbo Technologies
Additionally, you heard Mark allude to Caterpillar. There is large value for our technology in the off-highway and construction industry. On-highway, we're focused on CO2 and fuel efficiency. However, new regulations for on-highway vehicles add pressure regarding criteria pollutants, especially NOx from the California Air Resource Board and the recent announcements from the Environmental Protection Agency. The industry is working to get in compliance with those future regulations. The SuperTurbo can significantly help reduce NOx. It can also help significantly reduce particulate matter from the engines, improve fuel efficiency and reduce CO2.
The calculation for the off-highway value is typically based on work performed, which includes dirt moved over time and cycle times. Those work-performed measurements come down to the responsiveness of the vehicle and the responsiveness of the engine. A system like the SuperTurbo, through the efficient supercharging function, can reduce cycle times and more effectively move dirt over time. This is how off-highway manufacturers make money good equipment that functions at its peak and gets the most work done as possible.
We also see customers downsizing engines. With our Caterpillar program, the engine is a large downsize. They are taking a 13-liter engine and installing it into the same equipment that previously had an 18-liter engine. If you can make the engine much smaller because now you have this rapidly supercharged response from the SuperTurbo, then you can save money and fuel by downsizing.
The SuperTurbo is also applicable in the marine space because it helps boats quickly get up on plane.
Which fuels is this technology directed toward, and which may be more effective or evolutionary?
Tom Waldron: The technology is fuel agnostic and has been previously tested on engines using diesel, gasoline and natural gas. Since 2012, our primary focus has been on commercial vehicle diesel engines for on highway and construction. Much of our focus has been on the reduction of pollutants, improved efficiency and CO2 reduction.
However, during the last year, we've seen rapid growth across the industry for hydrogen as a fuel. Using hydrogen includes unique challenges. Many hydrogen engines have a lean burn strategy. To burn lean through a full cycle, you need to hold very high lambda (air-fuel ratio). Because our technology is an on-demand air system, it’s perfectly situated to fill that need for hydrogen engines.
Here is an example. A hydrogen engine will want to hold lambda to more than twice as much air as a car compared to fuel, and the boosting system’s ask is taxing. If a transient operation or acceleration is required and the high airflow must be held, there just isn't enough power in the exhaust. So, our tech can borrow some power and act like an efficient supercharger. We can hold that lean burn through the full cycle, which means those engines aren't going to have big spikes of NOx, which happens if lambda is not properly controlled. We can do a diesel-like engine in terms of response, while holding high airflow and minimizing the NOx created from the hydrogen engine. What we developed for diesel over the years can be directly applied to these new hydrogen engines and immediately address one of the core problems that they see, which is exciting. The activity this year has been intense when it comes to OEMs working on hydrogen.
Hydrogen is an exciting new trend in the industry, isn’t it?
Tom Waldron: It's great. As a turbocharging company, of course, the extended lifespan of engines and the value that they create are important to us. Being able to adapt from diesel and natural gas to a carbon-free fuel like hydrogen is important. The entire world is waking up to the fact that hydrogen engines are the quickest and easiest path to decarbonization.
The SuperTurboSuperTurbo Technologies
Why should OEM engineers be interested in this technology?
Tom Waldron: We're giving them a lever they didn't have before, which is precise air control. Engineers have always been able to precisely control and calibrate the fuel. With the SuperTurbo, they can precisely control and calibrate the air as well. The SuperTurbo also provides other benefits which allow for the reduction of harmful emissions, improved fuel efficiency, compliance with new regulations and reduced operating costs.
When do you anticipate the product being available for purchase on the market?
Mark Herbst: Successfully completing the DVP durability tests and having a strong production partner in Linamar demonstrates to the industry that the SuperTurbo will be ready for pilot production. Our expectations are to enter pilot production programs sometime during 2023 and 2024 and begin to migrate into low-volume production after that.
What are you most excited about regarding this technology?
Mark Herbst: As Tom mentioned, one is the whole hydrogen area, where everything we've done for the last 10 years for diesel applications is relevant to hydrogen. The SuperTurbo for diesel is the same exact SuperTurbo that will go into a hydrogen engine. Because of the rapid transition to hydrogen, OEMs have open minds to any innovative technology that will allow them to get the hydrogen engines compliant and into the market quickly. So, I'm excited about that. And the other is the fact that we can point to a great company like Linamar, who is signed up to produce the SuperTurbo. Since this announcement, we’ve been presenting to the OEMs, and the reception has been positive. The OEMs now acknowledged that they see a path to production. That's been a long time coming, and it’s pretty gratifying for me to hear.
Tom Waldron: Mark is right on that. The hydrogen growth is exciting. The ability to decarbonize our industry is huge. But I look at our life as a stool. One leg of the stool is the performance and its value. We’ve sent the SuperTurbo around the planet to different manufacturers for testing, and everybody has seen the performance and its value. However, the other legs of the stool are, is it durable, and what is the cost of the technology, and is the production secure? We needed to put the other legs of the stool in place. We started by showing the value and performance. Then we had to address the other things. It has been a process. You have an idea. You create the first prototypes. You start demonstrating your work with the manufacturers, and they see the value. Then that allows you to progress into the commercialization and the industrialization steps to envision getting to the start of production.
The industry doesn't move fast. This is commercial vehicles. It's methodical and slow moving. But once you're in, you're in for a long haul. These engines don't get revamped continuously year after year. It’s a great market for us to be in, but it's a difficult market to penetrate. That's why you don't see tons of new tech. You really must have something valuable to move in this space, and it takes a lot of investment dollars to get this done. SuperTurbo Technologies has been lucky to have strong investors who believe in the value of the technology who have supported us through the process. It’s great that, after a decade of development, we can see that the commercialization steps moving forward, and we're around the corner from production.