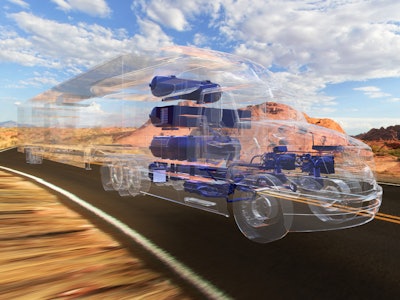
The use of hydrogen as a fuel source has been growing in recent years as vehicle manufacturers continue to shift their efforts toward the development of more sustainable and emissions-reducing power sources. Hydrogen is an attractive option as its only emissions are air and water, making it a truly zero-emission fuel.
Hydrogen can be burned in internal combustion engines or used in fuel cells to power electric motors and other components. This second area is where much of the development efforts have been focused for vehicle applications; heavy-duty vehicles in particular are seen as an application which could benefit from using hydrogen fuel cells as they do not require as a large a space claim as batteries.
According to Stephan Olsen, Director of Product Planning at Kenworth Truck Co., there are three zero-emission technologies available today to generate power—nuclear, battery and hydrogen fuel cells. He says nuclear power has not yet been developed for transportation applications, and batteries can be heavy, reducing payload capacity in heavier duty vehicles. Batteries also require a significant amount of time to recharge.
Hydrogen fuel cell vehicles, on the other hand, are able to carry sufficient fuel for a full day of regional operation, says Olsen, and can be refueled in under 30 minutes. “Hydrogen is the most plentiful element on earth, and is available virtually everywhere,” he adds, helping to further enhance its appeal.
Amanda Lyne, CEO of ULEMCo Ltd., adds that hydrogen can be made from a variety of sources including renewables such as wind and biomass, and as a by-product from industrial applications. She says these aspects help make hydrogen an important energy storage and long-term renewable fuel option.
Development efforts
Several companies have announced use or development of hydrogen fuel cells in recent months. In September, Nikola Motor Co. announced the electric drivetrain for its all-electric Class 8 truck in the U.S. and Canadian markets will be powered by a custom-built hydrogen-electric 800V hydrogen fuel cell. Trever Milton, CEO of Nikola, said in a press release announcing use of the fuel cells that the hydrogen will be produced via zero emission solar farms built by the company.
In May of this year, Kenworth announced several projects focused on developing low- and zero-emission trucks. One of those is a hydrogen fuel cell version of its T680 day cab. Work on the program, called the Zero Emission Cargo Transport Demonstration, is supported by a grant from the U.S. Dept. of Energy (DOE) Office of Energy Efficiency and Renewable Energy (EERE) with Southern California’s South Coast Air Quality Management District (SCAQMD) as the prime applicant. The hydrogen fuel cell version of Kenworth's T680 day cab utilizes Proton Exchange Membrane fuel cells to provide sufficient power in a small package size.Kenworth Truck Co.
An electric motor will be used to drive the rear tandem axle through a four-speed transmission. The motor will be powered by lithium-ion batteries, the fuel cell or both technologies, says Olsen. The fuel cell will also recharge the batteries, eliminating the need to plug the vehicle in between trips.
Olsen says a Proton Exchange Membrane (PEM) fuel cell—provided by Ballard Power Systems—is being utilized as it is the best means at this stage in development to use hydrogen fuel to power the truck. “This technology can provide sufficient power in a small enough package to make it viable for exploratory use in trucks,” he says.
He adds that PEM fuel cells are more efficient in producing electric power than burning the hydrogen and using the combustion energy to drive a generator.
PEM fuel cells use a membrane to separate the anode and cathode, explains Olsen, with hydrogen being supplied to the anode side and air to the cathode side. Use of special catalysts on the anode enable the hydrogen molecules to be processed so their protons pass through the membrane. Once they reach the cathode side, the protons are processed by another catalyst with oxygen molecules from the air to form water molecules. “Meanwhile, the electrons left over after removing the hydrogen’s protons pass through a circuit external to the membrane, providing the electrical power output of the fuel cell,” he says.
The truck is expected to run in regional operation within the Los Angeles basin, having a minimum range of 130 miles depending on load and duty cycle. Thirty of those miles will be all-electric, says Olsen.
Toyota Motor North America Inc. also announced earlier this year its plans to test a hydrogen fuel cell powered truck at the Port of Los Angeles. Known as Project Portal, Toyota will conduct a feasibility study to determine the potential of using fuel cells in heavy-duty applications.
The Toyota vehicle will utilize the company’s Mirai fuel cell stack currently employed in its hybrid passenger cars. Knowing the need to expand emissions-reducing technologies to all vehicle types, Toyota decided to test the fuel cell’s use in a Class 8 truck as it is the largest application in the U.S. in which to apply the company’s fuel cell technology says Tak Yokoo, Senior Engineer, Toyota R&D North America. Once it’s understood how the technology works in a heavy-duty application, it will be easier to have a pathway for extending it to the entire vehicle transportation industry.
Toyota will use two Mirai fuel cell stacks in its prototype truck, along with an electric motor, battery and other necessary power electronics. When running at a steady state, the fuel cell will provide the power necessary to move the vehicle. Once extra power is needed, such as for acceleration or pulling a heavy trailer, the battery will be used in tandem with the fuel cell. As soon as a steady state is reached again, the fuel cell will recharge the battery. The engine compartment of Toyota's hydrogen fuel cell operated prototype truck.Toyota Motor North America
Yokoo says one of the things that sets the Toyota prototype truck apart is the size of battery it will employ. Pure battery electric Class 8 trucks typically use a large battery of about 300 kWh, he says, and even some fuel cell versions have one in the 100-kWh range. However, the Toyota truck will only need a 12 kWh battery. This is because the fuel cell will be used the majority of the time to power the vehicle. “Any kind of vehicle when driving constant speed uses less than 200 kW of power,” he explains. And that power need can be met by the two fuel cell stacks, each of which develops 118 kW of power (236 kW in total).
Even when the battery power is needed, it’s usually not for an extended period, often less than 1 minute, says Yokoo. As such, the company attempted to find the minimum size battery which would provide only the necessary extra power.
Both the Kenworth and Toyota trucks have on-board hydrogen storage tanks to ensure a continued fuel supply for the fuel cells.
While many are focusing on hydrogen fuel cell development, ULEMCo is working on the engine side of things, converting them to use hydrogen. The company has the ability to covert engines to 100% hydrogen operation, but that is usually done with spark ignition engines which Lyne says are less efficient than diesel compression engines. In addition, she says that when hydrogen burns in an engine precautions need to be taken to manage NOx (nitrogen oxides).
Because of this, much of the company’s work is in developing dual-fuel engines operating on a mix of diesel and hydrogen. Lyne says ULEMCo can convert any conventional diesel engine to dual-fuel; the benefit of doing so is the engine being able to still operate on diesel when no hydrogen is available. “By using a mix of fuels and an efficient engine we can provide an optimized solution,” she says. “Also, by having the capability to run as a conventional diesel engine when hydrogen is unavailable, the vehicle or off-road equipment can still perform its duties.”
Lyne says the core of the company’s technology is its engine control unit (ECU) and hydrogen supply system consisting of hydrogen storage, pressure regulators, pipes and safety measures. The system works by injecting hydrogen into the air inlet of the engine and controlling the ratio of diesel and hydrogen to optimize the engine for performance, emissions and fuel use.
Larger vehicles are the main focus for the technology as there is more room onboard the vehicle for hydrogen storage. Last year the company converted a bin lorrie in Scotland to dual-fuel operation. Most recently it announced a collaboration with H2B2 to accelerate the commercialization of hydrogen fueled vehicles in Spain and the UK. H2B2’s work is in economic, green production of hydrogen while ULEMCo and its customers provide an avenue for that fuel to be used, making the two companies a good fit for the partnership. ULEMCo converts engines in heavy-duty applications to dual hydrogen and diesel operation to enable use of either fuel based on refueling availability.ULEMCo
For now the company is focusing on conversions as OEMs consider their strategies on hydrogen, Lyne says. “We are looking to get whole type approval status for our approach (currently this is not technically possible in the regulations), and continue to explore options for the longer term.”
Hurdles yet to overcome
Refueling infrastructure is one of the biggest challenges associated with making hydrogen a more commonly used fuel source. While availability of public refueling stations is growing, Lyne notes it’s from a small base of sources. The lack of scale in the supply chain of infrastructure equipment also makes the capital cost of facilities high in comparison with those for conventional fuels. “However, there are options for back-to-base fleet operations or off-highway sites with sufficient vehicles or equipment to achieve a comparable cost with diesel,” she says.
“Hydrogen fueling stations for heavy trucks are virtually non-existent today,” says Olsen. “There will need to be a considerable investment in refueling infrastructure before the use of hydrogen commercial vehicles can become widespread.”
Kenworth sees three major hurdles to be overcome in order for hydrogen fuel cell trucks to become more commonplace. The first, says Olsen, is the size of fuel cells. He notes the one currently being used in Kenworth’s prototype truck fills the entire engine compartment. However, the company’s suppliers are working on improving power density to provide more power in a smaller package.
Fuel cell cost is another challenge; they are expensive due to the precious metals being used by the catalysts on both the anode and cathode. “With improvements in the efficiency of these catalysts and the rest of the system, along with increased production volumes, they are expected to come down in cost over time,” Olsen says.
The final hurdle is the on-board hydrogen storage tanks as they take up a lot of real estate on the truck chassis. “Hydrogen is a very small molecule. Even though there is three times the energy in 1 kg of hydrogen than in 1 kg of diesel fuel, hydrogen’s tiny molecules want to take up a lot of space,” explains Olsen. “Even compressing hydrogen to 350 bar or 700 bar (5,000 psi or 10,000 psi), it still takes up a lot of space on the truck chassis – by the time the tanks are wrapped, plumbed and mounted in a cabinet on the truck, the hydrogen fuel storage system takes up 30 to 40 times the amount of space as a diesel fuel tank containing the same amount of energy. We are looking into ways to make more efficient use of space with the hydrogen tanks on the truck.”
Even with these challenges, many see the value in hydrogen as a fuel source, and so will continue to develop and enhance the necessary technologies to make it a viable option.
In January, 13 leading energy, transport and industry companies formed the Hydrogen Council, a global initiative focused on providing a united vision and long-term ambition for hydrogen being an integral part of the energy transition. Daimler, Shell and Toyota are among the members of the council. At its launch, the members confirmed their ambition to accelerate investments in the development and commercialization of the hydrogen and fuel cell sectors. Investments are estimated at a total value of €1.4 Bn/year.
With so much interest from manufacturers, fuel providers and other organizations, hydrogen’s future appears it will continue in a positive direction.