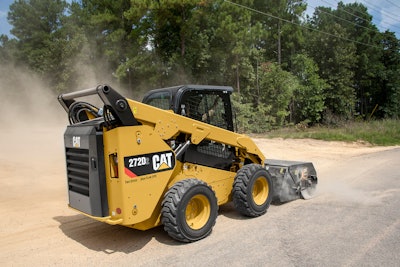
The new Cat 272D2 Skid Steer Loader, 297D2 Multi-Terrain Loader, and 299D2 Compact Track Loader—along with their more powerful XHP counterparts—build on the engineering advances in performance, operator comfort, visibility, control and machine security of their D Series predecessors. Now standard on all six D2 Series models is the exclusive Caterpillar heads-up Advanced Display, and all feature a new engine-compartment sealing system for enhanced airflow debris control. Non-XHP models have increases in rated operating capacity (ROC), and XHP models now maintain their excellent ROC numbers without external counterweights. All models have a vertical-lift loader linkage and use a Cat C3.8 engine meeting U.S. EPA Tier 4 Final/EU Stage IV emissions standards.
In addition to providing a theft deterrent system, the Advanced Display accommodates up to 50 operator security codes that allow each operator to adjust the machine to suit individual operating preferences. A full-color, 5-inch LCD monitor enables on-screen adjustment of implement response, hydrostatic drive response, creep control speed, ride control activation speed, language preference and gauge layout selection. Electronic instrumentation includes fuel level, DEF (diesel exhaust fluid) level, hydraulic and engine coolant temperatures, and tachometer. An available rearview camera, standard on the XHP models, displays high-resolution images on the monitor to comfortably increase the operator’s field of vision for increasing job-site awareness.
With increases in Rated Operating Capacity of up to 8%, the D2 Series models provide excellent lifting performance for heavy loads and/or handling larger hydro-mechanical work tools. The 272D2, 297D2 and 299D2 models deliver ROC ratings of 3,400, 4,700 and 4,600 lbs., respectively, at 50% of tipping capacity. Ratings for the 272D2 XHP, 297D2 XHP and 299D2 XHP are 3,650, 4800 and 4,725 lbs., respectively, at the 50% rating. For applications that require additional lifting capacity, all six models can be equipped with optional bolt-on external counterweights.
The C3.8 engine, rated at 98 gross hp in non-XHP models and 110 in XHP models, now uses a selective catalytic reduction (SCR) system for control of nitrogen-oxide (NOx) emissions to meet Tier 4 Final/Stage IV emissions standards.
The SCR system requires no maintenance other than periodic addition of DEF. The DEF level is easily monitored via the digital gauge provided on the standard Advanced Display. All D2 models have a lockable door cover for the DEF fill point, located on the right side of the machine. The DEF fill is identified with the industry-standard blue cap and has a smaller filler neck to deter filling with an incorrect fluid.
Sealing around the rear engine enclosure and cooling package is now standard for all D2 models. The standard sealing package (rear engine door, rear bumper, cooling package grill, cab/cooling package) provides enhanced protection against material ingestion in applications with a high volume of airborne debris. The hydraulically driven demand fan operates only when required, saving fuel and reducing sound levels
An optional reversing fan provides added value to customers operating in high debris applications. The reversing fan, with both an automatic and momentary purge capability, aids in the removal of material from the rear door intake screen to maintain maximum air flow to the cooling system.
Premium D2 Series features retained from D Series predecessors include the one-piece sealed and pressurized cab (Cab One), electro-hydraulic controls, premium seat choices, lift arms, available electric work-tool coupler, and available Intelligent Leveling features, such as dual self-leveling, electronic snubbing, return-to-dig and work tool positioner. The new 272D2, 297D2 and 299D2 models offer a battery disconnect option. The battery disconnect allows the battery to be isolated for machine service, minimize battery drain during storage or for additional machine security. The battery disconnect is standard for the 272D2 XHP, 297D2 XHP and 299D2 XHP models.
The steel track option is best suited for customers that require improved traction due to working in challenging underfoot conditions that may contain high concentrations of protruding objects (such as boulders, stumps, demolition debris, etc.) and/or using heavy work tools, working on slopes and/or working near transitions.
Undercarriage suspension is standard on all D2 Series MTLs and CTLs and isolates the undercarriage from the machine frame using torsion axles. The torsion axles allow independent up/down movement to distribute the load and absorb shocks and vibrations. This results in higher operating speeds, better material retention and increased operator comfort. Both the 299D2 and the 299D2 XHP can be equipped with an optional sealed and lubricated steel track system. The 15.7-inch (400 mm) triple grouser steel track delivers additional traction and/or track life in applications not ideally I suited for a rubber track.
The 297D2 and 297D2 XHP Multi Terrain Loaders features the unique dual-suspension undercarriage. The Dual Level Suspension offers a “second level” of suspension, in addition to the torsion axle suspension, using oscillating roller wheel assemblies. These roller wheel assemblies will independently pivot when they encounter an obstruction providing more track on the ground, better load retention, improved operator comfort and one of the smoothest rides in the industry.
The new D2 Series models provide easy, ground-level access to all routine service points. With more stringent emissions requirements, good fuel system maintenance has become even more essential. With the customer in mind, the D2 Series (and D Series) models feature an electric priming pump with automatic air bleed for the fuel system, easing the task of replacing and priming the fuel filter/water separator. For added safety, a dead-engine/boom-down actuator is repositioned for easier access and the boom arms incorporate a lift arm brace that can be installed and uninstalled by one person.