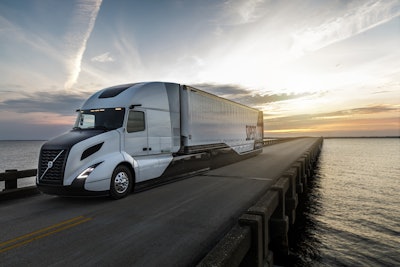
Volvo Trucks North America has unveiled an innovative SuperTruck demonstrator whose combination of advanced aerodynamics, vehicle and powertrain technologies achieved a freight efficiency improvement of 88% – exceeding the 50% improvement goal set by the U.S. Department of Energy (DOE) program.
From the top-of-cab solar panels powering its battery and interior lights, to its ultra-light aluminum frame and highly advanced 425 hp 11-L proprietary engine, the SuperTruck concept vehicle allowed Volvo engineers to push the boundaries of heavy truck efficiency. The sleek tractor-trailer combination boosted fuel efficiency by 70% – exceeding 12 mpg, with some test runs showing more than 13 mpg – in road tests, and powertrain brake thermal efficiency reached 50%.
“With the support of DOE’s SuperTruck program, Volvo Trucks has presented an exciting vision of trucking’s future,” says Göran Nyberg, President of Volvo Trucks North America. “Even more impressive is the fact that these tremendous gains were made against a base model Volvo that already in 2009 averaged 7 mpg.”
The SuperTruck program was a five-year DOE research and development initiative to improve freight efficiency – meaning more payload carried while burning less fuel – by 50% compared to 2009 base model trucks. The DOE recently selected the Volvo Group to participate in DOE’s SuperTruck II program, which will target a 100% improvement on a ton-mile-per-gallon basis, and a powertrain capable of 55% brake thermal efficiency.
Volvo’s aerodynamic SuperTruck has a shorter front end than conventional trucks on the road today, and the hood has a sharper downward slope. Lightweight fairings run the length of the tractor and trailer, and cameras have replaced rearview mirrors. Its redesigned chassis is made almost entirely of aluminum, which halved the chassis weight and contributed to an overall tractor-trailer weight reduction of 3,200 lbs.
An enhanced version of Volvo’s I-See, a new feature that memorizes thousands of routes traveled and uses that knowledge to optimize cruise speed and keep the I-shift automated manual transmission in the most fuel-efficient gear possible, was an integral part of the fuel efficiency gains seen during SuperTruck on-road testing.
A key part of the overall efficiency gain is the downsized 11-L Volvo engine, featuring advanced fuel injection, cooling, oil and turbo-charging systems, as well as new “wave” pistons and other improvements. The SuperTruck powertrain includes a complex Rankine waste-heat recovery system, which converts heat normally wasted in exhaust into torque, boosting fuel economy by helping to power the vehicle.
“The order of magnitude efficiency leap achieved by our SuperTruck is a testament to the outstanding work done by our team and our partners,” says Pascal Amar, principal investigator for the project. “We started by rethinking everything, and we discovered that with every layer you peel back, you uncover new opportunities.”
While not every technology demonstrated in the Volvo SuperTruck will be commercialized, three of the engine advancements developed through SuperTruck research – the wave piston, turbo compounding system and common rail fuel injection system – are already featured in Volvo Trucks’ 2017 engine line-up. Likewise, a number of SuperTruck-derived aerodynamic improvements – like flared chassis fairings improving air flow around the drive wheels, a redesigned bumper and turbulence-reducing deflectors – can be found on today’s Volvo VNL tractors.
“Our work through this program is paying dividends for today’s customers through the SuperTruck innovations we’ve already integrated into our products,” says Nyberg.
Not every idea made it to the concept vehicle. Working with suppliers and academic partners, the team explored the performance and safety of a number of lightweight materials. While some of these, like recycled carbon fiber, were not used in the SuperTruck, the knowledge gained in material science will be applied to future programs.
Volvo used computer-aided engineering to reimagine nearly every part of the tractor and trailer without costly prototyping. While the VNL “body in white” was mostly maintained in order to save time and ensure structural integrity, everything else – including the front end, the cab exterior pieces, the chassis fairing and the roof – were completely redesigned to maximize the aerodynamics of the tractor-trailer combination.