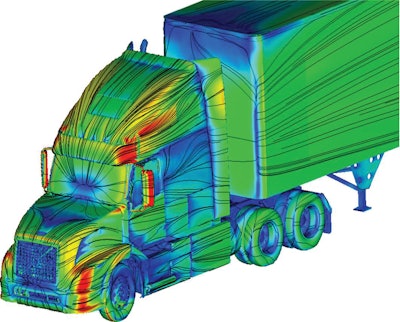
A vehicle’s efficiency has always been an important aspect of its design and is even more so today as gas prices continue to rise while emissions regulations grow more stringent. The transport industry has been especially cognizant of this because of how significantly the efficiency of a vehicle can affect the company’s bottom line. According to the U.S. Dept. of Energy (DOE), Class 8 trucks haul approximately 69% of all freight tonnage and use more than 20% of the fuel consumed in the U.S.
In 2010, the DOE’s Vehicle Technologies Program initiated the SuperTruck Program, a DOE-funded industry cost-shared project. The goal of the five-year program is to design a heavy-duty Class 8 truck which demonstrates a 50% improvement in overall freight efficiency measured in ton-miles per gallon. To ensure there is total vehicle improvement, 30% of the efficiency must come from the tractor and trailer, while the other 20% should come from the engine. Along with the overall efficiency, each vehicle’s engine needs to show 50% brake thermal efficiency as well as a path to 55% brake thermal efficiency.
In January 2010 the DOE awarded three cost-shared projects to Cummins Inc., Navistar Inc. and Daimler Trucks North America LLC. Volvo Group joined the SuperTruck program in June 2011.
Cummins
Cummins Inc., Columbus, IN, was one of the first companies to get involved with the SuperTruck Program. While Cummins is the team lead, the company is working very closely with Peterbilt Motors Co., Denton, TX, as well as various component suppliers to develop a fully integrated vehicle.
Scott Newhaus, Assistant Chief Engineer of Product Development Responsible for the SuperTruck Program at Peterbilt, says working on a project like this is exciting because it’s about the entire vehicle. “It’s not just the tractor, it’s not just the engine,” says Newhaus. “It’s the whole system working together, which is really exciting for us.”
Responsible for the vehicle’s engine system, Cummins has been working with Modine Mfg. Co., Racine, WI, to develop a waste heat recovery system to increase efficiency. The refrigerant-based system collects exhaust heat from various sources, such as the turbocharger or aftertreatment system, and expands the collected heat across the turbine to keep the engine cool.
Cummins is also working to further optimize the engine by reducing parasitic pump power, as well as increasing the efficiency of the engine’s turbochargers by looking at the combustion process.
Improvements to the aftertreatment system will ensure the system does a better job of cleaning up NOx (nitrogen oxides) to meet emissions regulations, says David Koberlein, Cummins’ Principle Investigator for the SuperTruck Program.
Improvements from Peterbilt include reducing loads through the use of lighter weight materials, such as aluminum. Adjustments to the aerodynamics of the tractor and trailer are also in the works to reduce the vehicle's drag. Peterbilt is working with Delphi, Troy, MI, on a solid oxide fuel cell (SOFC) for idle management. Additional technologies include an advanced transmission by Eaton Corp., Ann Arbor, MI, to reduce energy lost through the shifting process as well as driver displays. Newhaus says the driver displays will be an important piece of the puzzle, “ensuring [drivers] know what’s going on with the vehicle and how to react with the vehicle to gain the maximum efficiency.” As the team’s end user partner, U.S. Xpress of Chattanooga, TN, is providing feedback on whether the technologies developed for the SuperTruck will be a valuable commercial investment for customers as well.
Weight is added with new technologies for improved emissions and fuel performance. Vinod Dugul, a consultant for Cummins, says the entire team is working to reduce overall vehicle weight through the use of new technologies and materials. Peterbilt’s Newhaus says weight is no longer an issue, though optimization is a continuous process.
Integrating all of the components and systems has also posed some challenges for the team. However, Wayne Eckerle, Vice President of Research and Technology at Cummins, notes that the whole is greater than the sum of the parts. Working on the whole vehicle at once allows good system integration. If each system were worked on individually, the team wouldn’t be able to get the results it needs to meet the program's goals.
Koberlein says so far, the team is on track with the goals set by the DOE, and is even surpassing them. “The engine efficiency is pretty successful,” says Dugul. “We have our new truck with most of the technologies in place, and we are going to spend the whole of 2012 improving upon those, demonstrating our goal of meeting greater than 50% freight efficiency.”
Daimler
Daimler Trucks North America, Portland, OR, got involved with the program as a means of leveraging its R&D efforts and accelerating development of advanced efficiency technologies, says Derek Rotz, Senior Manager Advanced Engineering. “SuperTruck offers a funding platform to research high risk, high reward technologies which may not have otherwise been possible to investigate,” says Rotz. Working with Daimler is Detroit Diesel, Detroit, MI, who will bring engine expertise, as well as several national laboratories and industry partners.
Rotz notes that as part of Daimler’s comprehensive approach, improvements to external aerodynamics, the use of lighter weight materials and low rolling resistance tires are being investigated. On the engine side, the team will look into parasitic losses, engine controls and waste heat recovery systems for improved efficiency.
Reducing parasitics—engine power used for powering something other than the engine, such as a water pump—will be key to improving freight efficiency, says Kevin Sisken, Manager-Technology Programs and Analysis at Detroit Diesel. Sisken says any reduction in power requirements of additional devices provides a one to one increase in available engine power, “which has a direct correlation with the engine and vehicle fuel consumption levels.”
Other engine system improvements include the potential use of predictive engine controls and a two-step piston bowl. Predictive controls will enable the engine to stay at its best possible fuel economy map when transitioning between different speeds and loads, says Sisken. With the two-step piston bowl, the bowl changes how fuel mixes and interacts with air during the combustion process. “There is significant complexity and trade-offs during the combustion process,” says Sisken, “[and] the two-step piston has shown positive trade-offs on both fuel economy and emissions in bench testing.” Often, fast combustion can provide good fuel economy but causes an increase in NOx. With the two-step piston bowl there is an opportunity of providing increased fuel economy without increasing emissions as well.
Also under investigation is the use of a hybrid electric powertrain to help improve efficiencies by recuperating brake energy and working as an idle reduction system. High voltage batteries will provide electrical power to the vehicle for systems used when the truck is not in motion, such as climate control, preventing the engine from idling and producing additional emissions. Daimler is looking into using a SOFC for idle reduction, as well (See sidebar on pg.14). Prototypes of both the hybrid system and SOFC are being integrated into a functional vehicle to determine which idle reduction technology will be the best fit.
Designing and integrating the various technologies into one vehicle has not been easy. Rotz says the complexity and newness of the technologies causes technical uncertainty and requires rigorous testing. “The nature of the program forces engineers to work outside their comfort zone since there is little ‘tribal knowledge’ that can be drawn upon,” says Rotz.
Despite the challenges, Rotz says Daimler is on its way to meeting the project’s goals. Most of the work to date has been theoretical analysis via modeling and simulation of possible vehicle and engine systems. Rotz says system design, bench testing and on-road tests are now taking place to validate efficiency and performance of the theoretical analysis.
Navistar
As the principle investigator for its team, Navistar Intl. Corp., Lisle, IL, is responsible for engine and overall vehicle development as well as vehicle integration. The company is working with nine industry partners, such as Robert Bosch LLC (Bosch), Farmington Hills, MI, who will develop higher pressure fuel systems for the SuperTruck. Dennis Jadin, Director of Advanced Vehicle Technologies at Navistar and head engineer for the SuperTruck Program, says Navistar’s current diesel engines run at 2,200 to 2,500 bar. However, Bosch will provide a fuel system with pressures up to 2,900 bar, which Jadin says is necessary to meet the efficiency goals of the program.
To meet the 55% brake thermal efficiency goal, Navistar has been working with Argonne National Laboratory, Argonne, IL, on a dual fuel technology. The system uses gasoline injection for certain areas of the engine operation and diesel for others. Jadin says lighter loads will typically be addressed with gasoline, heavier loads with diesel and a mix of both fuels when necessary.
Further engine improvements will include combustion optimization through the use of the higher pressure fuel system and a waste heat recovery system to power the truck’s various electronics. Navistar is investigating two methods of waste heat recovery, says Jadin; electric turbo compounding and organic Rankine cycle (ORC). Electric turbo compounding uses exhaust heat to spin a turbine on the engine which is connected to a generator that creates electricity. The electricity is turned into useful horsepower and put back in the engine shaft to operate the truck’s electric motor. ORC, on the other hand, takes exhaust heat and boils a fluid via a heat exchanger on the exhaust. The boiling fluid and steam are moved through a nozzle and mechanical device to turn the turbine connected to a generator.
Jadin says both of these waste heat recovery methods paired with the electric motor help to create the hybrid technology Navistar will be using in the truck. The hybrid drive motor and generator sit behind the engine and completely eliminate the need for a transmission. “It’s all electric,” says Jadin. He continues that the system is designed to gradually accelerate the truck up to 40 mph with just the electric power, and once the truck hits road speed (55 mph) the diesel engine will take over. Many of the vehicle’s accessories have been electrified, as well, such as the power steering and air conditioning to save engine power.
While hybrid technology offers many benefits, these benefits can be nullified by the additional weight they bring to the vehicle. “A hybrid might bring improvements of 10 to 15% in fuel economy,” says Jadin, “but it comes with a penalty of weight, adding upwards of 2,000 pounds.” He says this potential weight gain must be kept in mind so that ton-miles per gallon is not affected. To counteract the additional weight, Navistar is using more aluminum; and Meritor, Inc. Troy, MI, will be providing a lighter weight rear drive, tractor bogie and disc brakes.
Radical changes to the shape of the truck’s cab and trailer have been proposed for aerodynamic improvements, including using more coattails and skirts. One method that will provide a large improvement will be through the use of a moving fifth wheel. Attached to the frame, the wheel physically moves the truck’s trailer 18 inches forward to eliminate the gap between the cab and the trailer. When the vehicle enters an urban area and has to slow down, the wheel automatically increases the gap. The entire fifth wheel system is automatic and does not require driver intervention.
According to Jadin, one of the biggest challenges of the program is commercialization. While efficiency is the goal, so is creating commercially viable products. He says the team intends to add close to 2,000 new technologies to its SuperTruck, which in a real-world scenario would be very costly for customers. “What technologies are worked on and what technologies are finally commercialized could be two different things,” says Jadin. Getting the new technologies ready and optimized for cost and packaging can be difficult and often take years. “Some of these technologies that we are validating might not see production until 2020,” he says.
However, participating in this program helps prioritize what technologies to produce. “It’s great that the DOE has given us a path to evaluate [technologies],” says Jadin. Rankine cycle, for an example, is expensive, complex and the fluid used is difficult to work with, but Jadin says as Navistar continues to investigate the technology further, the complexities could start to diminish. The program also enables the company to advance technologies that had previously been book shelved and bring them into production between 2014 and 2017, somewhat aligned with the impending U.S. Environmental Protection Agency (EPA) greenhouse gas (GHG) legislation.
The Navistar team is still working out many of the simulations, laboratory and dynamometer testing for its SuperTruck technologies. Jadin says the team is about half way through this stage and testing has shown they are reaching the 50% freight efficiency and 55% brake thermal efficiency goals. Jadin says the improvements will raise fuel economy 6% from about 5 or 6 miles per gallon to 7.5 to 9 miles per gallon. He says fuel economy testing is about to begin and the team “[is] on a good path to attaining our goal in the next couple of years.”
Volvo
Volvo Group, Gothenburg, Sweden, joined the SuperTruck Program in June 2011. Pascal Amar, Senior Project Manager overseeing Volvo’s involvement in the project, says that being involved with a project like this enables the participants to define what technologies are feasible to produce to meet regulations as well as customer needs. “Unlike the passenger car segment, where high volumes can support significant vehicle demonstration and development, the cost of heavy-duty demonstrator vehicles is extremely prohibitive, so most feasible technologies are already implemented in production vehicles,” says Amar.
Freight Wing Inc., Seattle, WA, is one of the many industry partners working with Volvo, bringing aerodynamic improvements to the truck’s trailer. Freight Wing intends to utilize its latest advancements in fairings and skirts as well as make alterations to the shape and size of the trailer to help improve efficiency. Grote Industries, Madison, IN, is providing flat and flexible marker lamps to minimize power consumption and drag resistance. Amar says Grote is also looking at the potential for wiring harnesses to further benefit from reduced lighting power demand.
The use of lightweight materials and complete vehicle aerodynamic optimization are two improvements being made to the exterior of the vehicle. Internally, Amar says Volvo will investigate several technologies including powertrain waste heat recovery, engine “downspeeding,” and reduced driveline friction and parasitic losses. Advanced Driver Assistance Systems (ADAS) will be used as well, says Amar, to demonstrate their ability to help improve freight efficiency.
Like many of the other teams involved in the SuperTruck Program, Volvo is evaluating the use of hybrid technologies, but only as an auxiliary power supply to run systems such as heat or air conditioning during overnight rest periods. Amar says hybrid technology is not being considered for other aspects of the vehicle because it would not provide the net efficiency improvement required by the program. He notes that hybridization can offer efficiency for diesel vehicles that frequently stop or idle, but because this generally isn’t the case for Class 8 trucks, hybrid is not the way to go.
Amar says the use of simulation software has been vital to determining which technologies to utilize in the truck design. “While simulations can facilitate design efforts, they will play a central role in ensuring that the correct technology package is selected,” he says. Simulations enable the team to evaluate numerous concepts and combinations. “Simulations also provide us with a virtual test vehicle which we can modify and put through its paces in the early phases of the project. This will help guide us through the challenging task of calibrating all systems simultaneously,” says Amar.
According to Amar, the Volvo-led team is on its way to achieving the 50% freight efficiency goal set by the DOE.