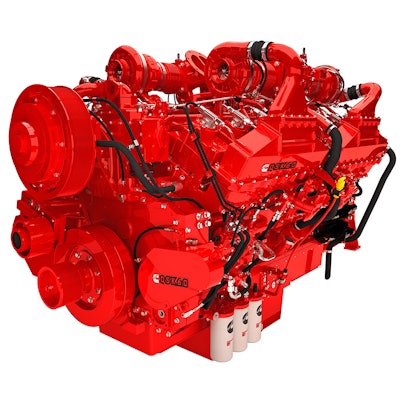
Cummins Inc. is announcing several new initiatives focused on reducing miners' total cost of ownership (TCO) related to engine operation.
Zach Gillen, Cummins Executive Director - Mining Business, says, "Faced with challenging economic conditions, our customers are keenly focused on conserving cash and optimizing equipment operation. Over 60% of a miner's TCO is tied to fuel, parts and service, and we have developed solutions which can be applied in a wide range of mining applications. These upgrades lower fuel and servicing costs, and are available for engines currently in use, providing immediate cost savings to cash-strapped miners around the world."
Cummins' fuel consumption reduction initiative, called Fuel Saver, is currently available for QSK50 and QSK60 engines, with plans to extend it to other high-horsepower engines. There are a number of options to reduce fuel consumption for mining trucks by 1-5% annually, which equates to an average annual saving of $6,000-$30,000 per vehicle. The fuel-economy improvement also generates an equivalent percentage reduction in CO2 emissions of approximately 10 kg (22 lbs.) CO2 per gallon of fuel saved.
"The improvements are achieved through base engine modifications, fuel system upgrades and electronic calibration changes. Our technicians will offer a tailored solution based on the customer's specification to achieve the best possible savings. They are available for Tier 1 and Tier 2 engines in service now," adds Gillen. Cummins is also able to reduce engine-servicing costs with the latest air, lube, fuel, hydraulic and water filtration technology, along with proprietary coolants. Nanofibers with a diameter smaller than a human hair are combined with a cellulose-based media to capture particles at a submicron level before they can reach engine components such as pistons, rings and liners.
Field studies around the world have successfully validated TCO improvements of over 60%, by extending service intervals to a minimum of 1,000 hours. In addition, the NanoNet technology has helped miners reduce costly equipment downtime.
"Our technology leadership, coupled with a collaborative focus on helping customers win, is putting us in a position to deliver market-leading total cost of ownership. Our latest TCO improvements are a good example of our commitment to the mining industry, and we will have experts on our stand at MINExpo to talk with anyone interested in learning more," concludes Gillen.