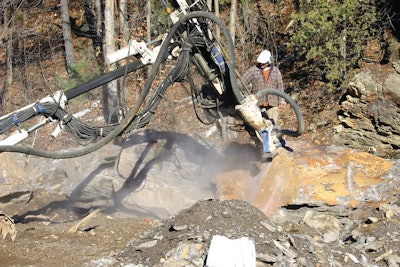
In 10 years of writing and editing articles for this magazine, the photo choices have never been as gruesome as they were for this article. Fortunately, illustrations of the bodily harm done by a tiny, high-pressure hydraulic leak aren’t suitable for a product development magazine. Most readers don’t need to see the unlucky operator to understand the severity of the injury. Words and phrases like “amputation” and “death from fluid injection” carry enough weight. I don’t need to see the photos, either. I know it looks bad.
The Europeans and Australians understand the dangers, too. Regulations are on the books to govern what OEMs should do to prevent personal injury when a high-pressure hose bursts in close proximity to a human, but it is a safety concern that is still largely overlooked by standards in the United States. It’s known as a line-of-sight burst because anything or anyone directly in front of the hole will be subject to a needle-like stream of oil.
As hydraulic systems become more complex, and pressures and temperatures rise, the potential for an operator or bystander to be exposed to leaks and bursts increases. It’s a danger that companies such as Gates Corp. and Suburban Mfg. are working to eradicate.
While research and meetings continue in the U.S. to create line-of-sight protection standards for the future, there are solutions available now. This is especially important for those OEMs looking to sell product to countries where risk evaluation includes preventing fluid injection.
A failure is not typically due to a poorly made hose. “When you see a hydraulic hose failure, 90% of the time, it is not the fault of the hose. It doesn’t matter what brand of hose it is,” says Yelena Gray, product development engineer, Advanced Materials Group, Gates, Denver, CO. “Installation errors at the factory, the machine’s operational environment, hose application and poor maintenance can all increase a hose’s chance for failure.”
Leak, burst barriers
The LifeGuard hose sleeve system from Gates is a tightly woven inner layer that elongates to absorb the energy of a leak. The sleeving can contain 3,000 psi pinhole leaks at 212 F for up to five minutes. It is also tested for up to 6,000 psi burst containment for added safety. The outer layer restrains the escaping fluid and redirects it to the clamped ends of the hose. A pool of fluid alerts the operator to the failure.
Marty Bauer, product applications engineer, Gates, says that before LifeGuard some customers required that hoses running next to the operator have a sleeve over them. “We used an abrasion sleeve, which we made clear was not designed for line-of-site protection.” The idea was that the sleeve would prevent any rupture, which was believed to be caused by abrasion. Testing has since proven that theory false.
“From a legal stand point, it satisfied the requirements, but it did nothing to protect the operator from a burst or leak,” says Bauer. “The rules are beginning to change, since significant injuries have been occurring in the field due to higher pressures.”
In developing the LifeGuard product, says Gray, “there were no U.S. standards on which to base the tests and product design. We had to develop our own pass-fail criteria based on our experience. We mimicked the applications and failures we saw in the field to design and prove the product.”
Suburban, a diversified manufacturer in Monticello, MN, recently introduced its Diamondback sleeve to give protection from line-of-site bursts. The product is a natural progression from its Sidewinder abrasion sleeving, which has been offered for more than a decade.
Sold in 300 ft. rolls, the Diamondback sleeve is tightly woven using a proprietary engineered fiber and then heat-treated to shrink it by 8%. If a hose bursts, it impacts the sleeve but is contained within, protecting the operator and the environment from fluid injection and spills. It is rated for 4,000 psi working pressure pinhole leaks and 16,000 psi bursts.
With no finalized domestic standards to target, Suburban designed the Diamondback product to meet the European Union’s Machinery Directive 2006/42/EC and New South Wales, Australia, government’s MDG 41: “Guideline for Fluid Power System Safety at Mines.” The latter specifically says “all hazards must be identified and dealt with so they are eliminated or controls established to minimize the risk,” and highlights fluid injection specifically.
Until such protection becomes mandatory in the United States, selling the product has required doing some educating to the dangers involved in the placement of hoses. “We usually have to share a fair amount of information when talking with engineers at OEMs, usually some of the highlights of the foreign directives that pertain to hose failures,” says Randy Brolander, sales and marketing manager, Suburban. “We encourage them to buy the standards to understand what is happening over there.”
When Suburban’s sales team talks with an OEM seeking certification to sell product in Europe, they are likely already aware that risk assessment includes hydraulics, electronics and drivetrain systems.
“In the next year or so more application engineers will know about the requirements,” says Brolander, “and they will have to apply redundant hose covering or they will never get their machines certified for sale overseas.”
No longer an afterthought
Gates considers LifeGuard to be in the operator protection category rather than fluid power, and the product does add extra cost to a hydraulic system. It is not intended to be used on every hose throughout the machine. Application engineers at Gates look at all types of hydraulically-operated pieces of equipment to ensure that the operator, technician and bystander will never be within a hydraulic hose’s line-of-sight.
Common applications for LifeGuard are “anything with a boom on it,” says Bauer. “The boom is the operator’s best friend, and they are often right out there next to the hoses.”
The best case-scenario for line-of-sight hose sleeving it to design it into the machine. “That is what Europe is pushing,” says Brolander. “They don’t want it to be an afterthought.”
There is an environmentally friendly aspect to this type of hose sleeving, as well. Gates sees strong potential for LifeGuard in agriculture, where fluid leaks can damage crops. “It isn’t designed specifically to protect environment after a hose failure, but the sleeving does isolate the fluid so it doesn’t spray out 30 ft.,” says Gray.
Environmental concerns are something the safety directives don’t touch upon, says Brolander, but it is “always a concern on jobsites these days. Crews have to dig up and incinerate dirt contaminated by a large oil spill. Diamondback sleeves hold fluid well without wicking or saturating, minimizing the environmental impact from a leak.”