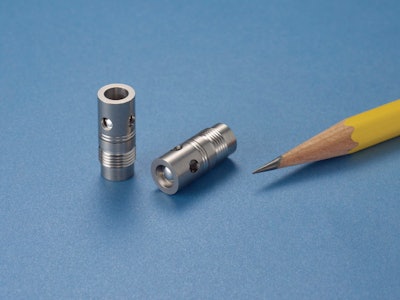
The Lee Co., Westbrook, CT, has been designing, developing, manufacturing and testing miniature precision fluid control components for over 60 years. Founded in 1948, The Lee Co. is known for its expertise in miniaturization. It was that expertise which led a hydraulic system manufacturer looking to solve hydraulic isolation issues in manifolds to its doorstep, looking for a solution with a smaller part than was commercially available.
The situation is common. While mechanically actuating a brake to hold an actuator in place, before the actuator can extend or retract, the brake must be released. If there is no brake, “you can get actuator drift,” explains Serge Doyen, vice president IMH (Industrial Microhydraulics) Group, a division of The Lee Co. “Whenever there is pressure in either of the two lines, you want to release the brake so you can move the actuator.” The same principle applies to a hydraulic motor.
“What the 8 mm shuttle valve does is it isolates the low pressure side from the high pressure side regardless of which line is high and which is low pressure. In other words, you have a directional control valve that is either telling the actuator to do nothing, to extend, or to retract. So you’re switching what would be the pressure line and the return line back and forth depending on which movement you want of the actuator,” he says. “This shuttle valve is shunted across these two lines. The output then goes to release this actuator.”
There are several different manufacturers of selective shuttle valves. The unique part of The Lee Co.’s project, and the reason why other shuttle valve products wouldn’t work was because the customer needed something very small.
“Most shuttle valves are retained with threads and they’re sealed with O-rings which would require a much bigger design,” explains Doyen. “Our shuttle valve is about a third of the size of other shuttle valves that are generally available. We do this by using the insert principle which uses a pin to expand a grooved section of the insert’s body into the housing wall to effect a seal and retain the component. The pin, which has been pre-installed, is driven into the body. Using friction and penetration, the lands bite into the housing material.”
The Lee Co.’s 8 mm shuttle valve features a compact (8 mm dia. by 16 mm long), non-detented design with no O-rings or threads. It can handle flow rates up to 6.2 gallons per minute, or 32 Lohms (a 1 Lohm restriction will permit a flow of 100 gallons per minute of water with a pressure drop of 25 psi at a temperature of 80 F).
Constructed entirely of stainless steel, the shuttle valve features low leakage (1 drop per minute maximum after a 2 minute wait on hydraulic fluid at 6.9 to 27.6 MPa (1,000 to 4,000 psid)) and a maximum working pressure of 28 MPa (4,060 psi).
The shuttle valve is ideal for hydraulic auxiliary functions such as hydraulically released, spring applied brakes and load sensing applications on back hoes, dozers, and vehicles as small as lawn tractors. The 8 mm shuttle valve solution The Lee Co. was able to provide to the hydraulic system manufacturer was for a light utility vehicle.
The development process
“There wasn’t much back and forth. The customer was able to define the function, and then told us the flow rate,” says Doyen. “It took about a year to do the full development until we had the design completely refined. Then we supplied samples, and then spent another year developing the production system.”
All tests for the shuttle valve were performed in-house, including performance and life cycle testing. Since the shuttle valve is a relatively simple device, the testing was straight forward.
The challenge was to design a valve that had low leakage, since the shuttle valve is a metal-to-metal design with no O-rings. Since minimizing interflow leakage is also important, testing was required to ensure a low shuttling pressure.
Lee’s internal standard life cycle test includes 500,000 impulse cycles at 4,000 psi and an aggressively high pressure rise rate in excess of 100,000 psi/sec. Most equipment operates at much lower pressure rise rates, but The Lee Co. tests aggressively to ensure a large service life margin.
The Lee Co.’s 8 mm shuttle valve allows hydraulic systems manufacturers to reduce the size and weight of their equipment, explains Doyen. “In addition, the absence of O-rings and threads means no leaks and no seal replacement.”