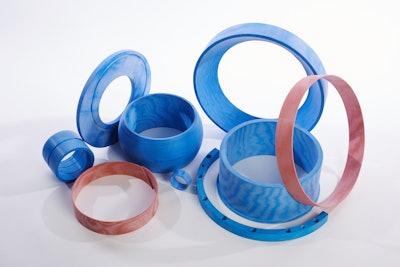
Composites—the combination of two or more materials—have found their way into several industries within recent years due to the many advantages they can provide. According to Andy Hessler, President of Brokkr Technologies Inc., composite materials have the potential to reduce component cost, part mass and the time it takes to get a design to market. “They can also increase reliability when their tribological characteristics are taken advantage of,” he says.
Fluid power is one such industry that could benefit from the use of composites; while already used by some manufacturers, material advancements have increased the potential uses and benefits that could be achieved.
There are a wide range of material composite choices, making it necessary to spend time investigating the full range of possibilities, as well as cost and performance balance. Composites and plastics can be processed in ways most metals cannot, allowing a greater range of freedom to optimize shapes for strength and material performance, and to tailor the design to fit a particular manufacturing method. Polygon says there is significant market opportunity to be gleaned by incorporating composite materials into cylinders, such as reducing weight, improving corrosion resistance, and being electrically non-conductive.Polygon Company
Tim Girardi, Applications Engineer at System Seals Inc., says one of the main reasons to use a composite versus a singular material is the ability to blend and manipulate the materials to get the benefits of both materials. He explains that a material may be chosen for its lower friction rate properties, but when used by itself has a high wear rate. Combining it with another material which has a low wear rate, however, enables the manufacturer to get both of the desired properties—low coefficient of friction and low wear rate.
System Seals uses composites as a means of improving performance primarily for internal bearings, bushings or guide bands says Girardi. Among those improvements it is looking to achieve is reducing metal failures, extending seal life, and reducing leakage rates. The company is also interested in lowering friction and wear rates, as well as reducing costs, through the use of composites. Girardi says in some cases, integration of composite materials can reduce a cylinder’s size in the given application.
The type of composites used will vary by application, though Girardi says typically for fluid power applications the material will be a combination of a resin—such as a nylon, polyester or phenolic—and a reinforcement or filler such as glass or carbon fibers, PTFE or a woven fabric embedded into the resin. “One of the things we really tend to go away from for most of our fluid power applications is glass-filled nylons and phenolics,” he says. “Our testing has shown they really don’t perform very well.
“For composite bearings, we typically recommend our polyester composites because they have been optimized to reduce wear, friction and fatigue in addition to increasing yield strength, modulus and operating temperature limits for most applications,” he says. “They also benefit from being compatible with a wide range of hydraulic fluids.”
Hessler says higher performing composites such as polyetheretherketone (PEEK), polyamide-imides (PAI) and polyetherimides (PEI) are being used more in demanding applications. These composites have strength characteristics that are comparable to many cast and sintered metal parts commonly used in hydraulic components. “They also have tremendous chemical stability and can operate in higher heat applications without deterioration,” he says.
“Each application comes with its own set of constraints of cost, reliability and performance,” he says in regards to determining if a composite will be suitable for a particular application. “What works in one area may not work in another…manufacturability, availability, as well as cost have to be taken into consideration.”
Composites in the fluid power industry
Hessler suggests pumps of all varieties stand to benefit greatly from being made of composite materials where weight and cost are a concern. And any component that relies heavily on the frictional characteristics of brass is also a good candidate for conversion to composites. This is because many composites will be equally as strong as brass with similar or better coefficients of friction while offering lower part costs. “Hydraulic cylinders can also benefit from further development, especially as there exists the ability to integrate position sensing into the cylinder housing itself,” he says. “That alone can have a dramatic effect on many systems.”
Polygon Company, which has been making fluid power components using composite materials for over 20 years, is one such company that has been pioneering cylinders with embedded electronics. An example is its Intrinsic Sensing Technology which was created in cooperation with Sentrinsic, an incubated technology entity hosted by Georgia Tech University. Sentrinsic developed the software and electronic interfaces while Polygon provided the chemical, structural and mechanical elements, says Jim Shobert, CEO of Polygon Company. “Sentrinsic had read about Polygon’s previously engineered fuel system tubing for military aircraft that was partially electrically conductive while also insulative,” he says, which provided a basis for the technology’s development.
Shobert says Polygon further enhanced its tubing to have discrete layers, within the same cross-sectional area, that were alternating between being magnetic and non-magnetic. By incorporating an electronic ratio metric calculation, Sentrinsic was then able to measure the magnetic disturbance going on within the tube as a metallic piston traversed the length of that object. “The stated goal was to provide a feedback mechanism embedded within the cylinder itself circumnavigating the prevalent and dominant process of having to gun bore the piston rod,” he explains. While Sentrinsic was unable to commercialize the technology, he says Polygon continues to work in this arena, incorporating multi-tiered approaches.
The process of manufacturing a composite structure, which is done in layers, enables secondary materials such as electronics to be incorporated within the structure and eliminate the need to mechanically affix them as is the case when using metals, says Shobert. “Essentially, these components can be encased within the laminate structure, like building a house with the wiring contained within the wooden truss itself.”
From inception, Shobert says the company has felt there was significant market opportunity to be gleaned by incorporating composite materials into cylinders. In addition to the traditional benefits they provide—lighter weight, improved corrosion resistance, and being electrically non-conductive—Polygon found composite materials have a propensity to improve seal life. This is because of the micro surface properties of the inner bore being undulating rather than peaked, which metallic surfaces are unable to mimic without considerable investments in polishing or honing, says Shobert.
“Conceptually, we also embraced a vision that composites could serve as a platform for embedded materials such as sensors, fluid passages, wiring, foils, thermocouples, magnetic particles, fiber optic, and so on,” which had been partially demonstrated by development of the Intrinsic Sensing Technology.
Steelhead Composites employs the strength of carbon fiber contained within a thermoset epoxy resin matrix to withstand the high stresses in the walls of pressure vessels.Steelhead Composites LLC
One of the challenges with this, however, is the variety of materials that can be incorporated into a component. There are not only numerous fibers—such as fiberglass, basalt and polyester—but also resins that hold the fiber architecture in place. Vinyl ester and epoxy are among the possible options which are thermoset in structure; Shobert says new thermoplastic resins are advancing within the industry, especially in Europe. Polygon recently developed a new accumulator which incorporates thermoplastic resins “which can literally be pounded by a baseball bat or hammer without leaving any delamination, dents or fractures.”
Mike Stewart, Product Development Manager at Steelhead Composites LLC, says a primary advantage of composite materials is their strength-to-weight ratio that can be applied in a specific orientation, as needed for a given design. “At Steelhead Composites, we employ the strength of carbon fiber contained within a thermoset epoxy resin matrix to withstand the high stresses in the walls of pressure vessels with operating pressures up to 10,000 psi (689.5 bar),” he explains.
The company’s vessels also typically include glass or aramid (Kevlar®) fibers on the exterior surface to take advantage of their damage tolerance. “This is an example of applying distinct attributes of composite materials to address unique design requirements even with the same component,” Stewart says. Steelhead Composites is also pursuing the use of thermoplastic resins as a matrix material, which will offer improved processing techniques, as well as enhanced toughness and recyclability.
Stewart says composites can be particularly beneficial in mobile applications to reduce the weight of large, heavy, high-strength components. “Weight savings of up to 75% have been achieved with high pressure accumulators that have the same functional characteristics as their steel counterpart,” he says.
The extremely high specific strength (the ratio of strength to density) of carbon fiber, combined with its ability to be applied in a specific orientation to carry the highest loads makes dramatic weight reductions possible, explains Stewart. In the case of pressure vessels, the highest stresses caused by the contained pressure are hoop (or circumferential) stresses within the walls. By designing the composite overwrap in the hoop direction, that load can be carried very efficiently by carbon fiber reinforcements, much more efficiently than an isotropic material that will require thickness (and weight) additions in all three dimensions in order to support loading in that one primary direction.
Challenges with utilizing composite materials
Girardi says understanding not only the intended application but also what is trying to be achieved in that application is an integral part of working with composites. Engineers want to be sure they understand and take advantage of the materials being compounded together in order to benefit from the desired properties and ensure they perform as desired. An example of different guide band materials in the same application. The product on the left is a System Seals composite guide band, and the one on the right a competitor's that was ill suited for the environment and thus suffered catastrophic failure.System Seals Inc.
Fluid compatibility, for instance, is an important factor to consider. He says certain resins may disintegrate due to the fluid being used in the application which will cause problems immediately. “We’re always looking at those…doing a lot of testing in-house of certain materials in certain fluids so we have a better understanding of these properties and how they perform so we can make better decisions on our composites,” says Girardi.
“Designing for composite materials can require consideration of factors that are distinct from traditional metals, such as stresses carried by the part, the direction of those stresses, surface finish, damage tolerance, operating temperatures, fatigue and wear,” adds Stewart.
There is a limited availability of design software that accurately captures the behavior of composite material, he says, which poses a challenge, as does acquiring the specialized training for engineers to perform analysis of composites. In addition, many professionals have limited familiarity with what composite materials are available and how their properties may affect any particular design.
Shobert says one of the most significant challenges associated with using composite materials is determining how to incorporate them into existing or traditional assembly processes. “The engineering community isn’t confident that a bonded joint can manifest similar properties to that of a mechanical joint,” he explains. “As an industry we have all benefited from Boeing’s ability to advance non-traditional techniques, so this paradigm is changing.”
Traditionally, mechanical approaches have consisted of welding, threading, crimping or tie rods. Polygon, therefore, has collected a significant amount of information on how to mechanically affix metallic components to composites in order to get around previously perceived composite adaptation constraints. “One unique patent we have created, which incorporates a mechanical joint, is to press fit a metallic end into the composite tube and allow the hoop forces of the composite structure to lock the rod end in place,” says Shobert. “Additionally, we have pioneered techniques on winding the fibers around the metallic interfaces, thereby also creating a robust mechanical joint which the engineering community can embrace.”
As with any new or different technology, familiarity is a key challenge to industry adoption. However, Stewart says there is a trend of composites gaining more widespread acceptance due to their use becoming more commonplace in other industries such as aerospace, automotive, marine and sporting goods.
Shobert notes among the significant obstacles to adoption is design variability when building a composite structure. “When working with metals a rich history exists regarding material properties,” he says. “Those of us producing composite structures typically present material properties in terms of ranges, often with significant variability, which is completely dependent upon such things as fiber architecture and material constituents. This is both a very positive design feature as well as a confusing one which requires more market education.”
Girardi says that as System Seals conducts its in-house testing and sees the benefits composites can provide, it tries to make that data available to others. Doing so makes it easier to help a customer understand the benefits which can be achieved. “When we’ve actually applied and used [a composite], we try and share those case studies, as well,” he says.
The process of manufacturing a composite structure is done in layers, enabling secondary materials such as electronics to be incorporated within the structure.Polygon Company
By building upon the benefits and features existing within composite materials, says Shobert, the fluid power industry could find advantages to developing more composite-based components. He notes that in the example of a mobile crane, composites offer the potential to design the hydraulic fluid paths for the boom’s actuation cylinder into the wall of the cylinder. “This is only a small example of the design freedom and flexibility composites afford,” he says. “It simply takes more engineering collaboration between those with the applications and the composite entities with the design capabilities.”
“The risk averse culture that has grown up around the fluid power industry is leaving huge opportunities for other technologies to completely replace hydraulics in many cases,” says Hessler, and points to automotive steering systems being a prime example of this. “What will happen is not that hydraulics will go away…but the scale and scope of what they’re applied to may shift under our feet quite suddenly, leaving us a smaller market to work with.
“Companies that spend the effort to look around the bend to see where the trail is leading will be ready to make the appropriate adjustments to their products before it’s too late,” he concludes.