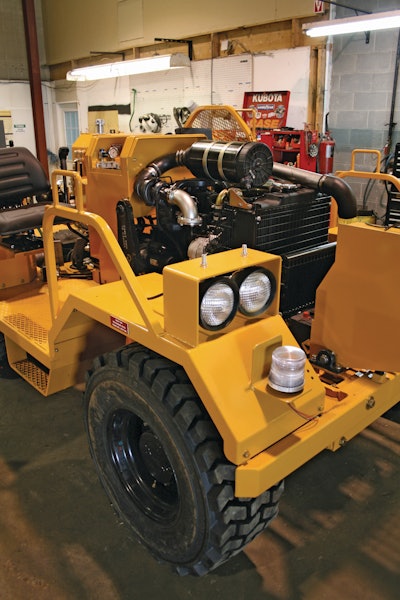
The deep hard rock mines lining Ontario's Sudbury Basin feature some of the toughest working conditions in North America. There are more than 3,000 miles of mine tunnels under the region's lakes and trees — some of those miles start at the bottom of a shaft more than 8,000 ft. below sea level. Down there, moisture-laden air mixes with ambient rock temperatures hovering around 100 F. Factor in long ramps with grades of more than 20%, narrow tunnels walled with unforgiving igneous rock and the occasional puddle holding enough sulfuric acid to consume a screw — Pebble Beach, this is not.
Equipment builders get no breaks, even in that environment. Whether using a production or support vehicle, mine operators expect maximum availability from their equipment. An equipment failure in a narrow tunnel 5,500 ft. down and two miles from the elevator, or cage, to the surface can be very expensive and downright inconvenient. Mines also want the machines to be safe and easy to maintain.
Utility vehicles, as ubiquitous in mines as telehandlers at a Las Vegas casino construction project, must be able to move quickly so as to not impede a truck loaded with nickel-bearing ore worth thousands of dollars. Utility vehicles must be extremely reliable and easily serviced. If a production machine is down, the supervisor's 4x4 will have to wait and likely keep working until its turn comes up.
Once workers leave the cage, it can be a long drive through the tunnels, or drifts, to the development work (such as extending a drift en route to the ore body), or the stope (where ore is being removed). Work areas are spread out, and supervisors must keep an eye on each location. A utility vehicle can easily add up more than 100 miles a day.
Covering 1,400 sq. miles five hours north of Toronto, the amalgamated City of Greater Sudbury is the hometown market for Industrial Fabrication Inc.'s utility vehicles. The Minecat 6000 Series is the company's flagship model. It's a heavy-duty multi-use vehicle that can be ordered in many different variations, such as a two-passenger lube truck and a seven-passenger personnel hauler with ROPS/FOPS protection, each on the same common platform.
The 6000 Series grew out of a line of modified farm tractors Industrial Fab acquired in 2002. For several decades, tractors were mining's preferred foundation for underground utility vehicles. A new tractor was purchased and stripped, its agriculture-specific bits replaced with components designed for mine work.
"They were relatively low-capital cost in the early days," says Daryl Rautiainen, vice president, Industrial Fabrication, "but they were plagued with reliability and durability issues which drove up operating costs. Many of these utility tractors were costing as much in maintenance as large production equipment."
Over the years, as more equipment suppliers built their utility equipment on farm machinery the tractor-based Minecat became a "me too" product. Nothing put the utility vehicle apart from its competition. Pat Berube was hired as engineering manager to help raise the bar on Industrial Fab's vehicle line.
"We realized that the most successful machines in the mining industry are the ones that are purpose-built for their application." says Berube. The decision was made to explore the opportunity of building our own purpose-built machine."
Berube's team talked extensively with end-users during the design stage. He did not have to leave the city to meet with potential customers. There are 15 mines and more than 100 years of continuous mining experience within the city limits. Supporting that work are nearly 300 firms focused on mining supply and service (MS&S) ranging from specialized fasteners to equipment design and world-class system developers. It's a virtually unparalleled concentration of hard rock mining experience.
When developing a new product "you have to talk with customers and learn what they want," says Berube. "If you don't listen you won't be successful. Getting the end-user involved early gives them ownership in the final product, as well."
That approach seems to have worked; the new-generation Minecat has been a strong seller, finding work in the United States and as far away as Indonesia.
Berube sat down with local mine specialists again when he started work on Industrial Fab's latest product, intended to fill the role a full-size pickup would play on a pipeline project. The purpose-built philosophy worked for the design of the new-generation Minecat and was carried forward on the new project.
Introduced in June at Nevada's Elko Mining Expo, the Minecat UT99 is designed and built from the ground up for supervisors and other workers who no longer want a modified sport-utility vehicle or pickup. After its debut in Nevada's gold country, the UT99 prototype was trailered to the Stillwater Mine near Nye, MT. The Montana mine has already ordered several UT99s. These machines will be supported by a sales and service operation, Industrial Fabrication USA Inc., which opened in 2006 in Winnemucca, NV.
The new truck is used to travel quickly between a surface office and a distant stope. In a mine vehicle, speeds can reach 20 mph. Typical speeds in a mine are usually half that. The UT99's top end can be limited to the specific mine's requirements for safety purposes.
Berube's team specified robust parts, including MICO's new wet enclosed disk brake (May 2007 issue), mine-grade wiring, an Iveco Motors (FPT) 99 hp MSHA-certified engine, automatic transmission and a dedicated hydraulic system.
"In Sudbury there are many local people specializing in all of the different aspects of mining," says Rautiainen. "You're never too far from someone who can help you with an issue. You can't do all of the development on your own."
Paul Ballard is part of that local knowledge base. He's president of Fluid Power House, a full-service hydraulic component distributor that specializes in one of mining equipment's key safety systems — brakes.
"If there's a diesel engine on the machine, we are interested in assisting with product development," says Ballard. "The estimate is there are 3,000 pieces of diesel equipment underground in the Sudbury Basin," including production and utility vehicles. "Manufacturers are specialists in certain areas of the machine and usually turn the brake work over to us. We guarantee everything, which takes much of the risk away from the OEM."
Fluid Power House is invisible to end-users. OEMs call for replacement parts. "We keep a lot of parts in stock. When a machine is down, there is no waiting around for a part to come in. A guy will stop in to get a part, and we'll give it to him and sort the paper work out later."
A movement toward standardized vehicles wherever possible has helped with parts availability. OEMs are encouraged to use common components. Ballard can stock a relatively small number of products to support 90% of the applications. "Everyone benefits from standardization," he says.
Deep impact
How Sudbury developed into a mining technology center can be linked to a number of factors. Common elements in every explanation are a direct hit from a meteorite (about 1.8 billion years ago) that created one of the highest concentrations of nickel-copper sulfides in the world, and the two oldest and largest mining companies in the area.
They were formerly known as Inco (Creighton Mine started producing ore in 1901; today production areas are more than 8,000 ft. deep) and Falconbridge (80 years of history in Sudbury). Last year Inco was acquired by Brazilian mining giant Companhia Vale do Rio Doce (CVRD) and became CVRD Inco, while Falconbridge attracted Switzerland's Xstrata plc. The Sudbury division is now Xstrata Nickel.
Clusters of companies that work together to solve industry problems do not develop overnight. Mining activity throughout the basin increased after the 1940s. Mines required custom-built equipment to meet unique applications and standards. Synergy between individual mines owned by the same company was rare. Between different companies it was worse. Still, improving production efficiencies — especially when nickel prices bottomed out — was always important. Local suppliers were busy supporting activity in and around Sudbury and expanded along with their customers. Mine firms were in a position to support research in mineral extraction techniques and technology, and when something worked they became a customer.
A unique entrepreneurial spirit — grounded in practical solutions while shooting for the moon — developed which still exists today.
"In Sudbury you can dream up the weirdest machine and find the people in the neighborhood with the right skill sets to make it work," says Ballard. "We all know each other. There's a level of trust that works well. But up until a couple of years ago we really didn't tell the world about what was going on here. OEMs competed with each other for the local market, and that was good enough."
New business outside of Sudbury was not being tapped. Small to medium-sized companies often didn't have the resources to market their equipment outside the area, and when times were good (like they are today) there was really no incentive to do so, anyway. One of Sudbury's large companies has 800 pieces of equipment underground, and replaces 100 units annually.
When Ballard opened the area's Fluid Power House office five years ago, one of the first calls he made was to Dick DeStefano, today executive director of the Sudbury Area Mining Supply & Service Assoc. (SAMSSA), an organization he helped create in 2003 to market Sudbury's expertise to the world.
SAMSSA's mission can be summed up as follows: "When mines in Nevada or South Africa look for a new product, we want them to come to Sudbury first," says DeStefano. When it comes to mining, Greater Sudbury offers one-stop shopping.
DeStefano worked as a strategic planning consultant for private corporations and cities in Canada helping them grow and diversify. He returned to Sudbury ready to retire at a time the city was looking for a way to lessen its economic dependency on the cyclical mineral extraction industry. DeStefano was among a group of people who began to appreciate the potential of Sudbury's already active technology cluster.
Rather than ignoring its strengths, they would embrace Sudbury's mining expertise. Diversification would come by sharing its MS&S knowledge with the worldwide market, be it partnering with OEMs or researching techniques for deep ocean mining.
Hundreds of millions of dollars are being invested in seeking new ore bodies that will easily sustain the area for another century. But due to ongoing productivity improvements in mining, thanks to the very technology the area's engineers create, Sudbury's strongest growth potential may not be in mines, but in MS&S. Two years ago, a SAMSSA study showed there were 17,000 people employed in MS&S companies in Greater Sudbury and neighboring cities. There are less than 10,000 working directly with mineral extraction (from a peak of 26,000 in 1971).
"In a cluster there needs to a unifying source saying we should be responsible for each other," says DeStefano.
"Sudbury's companies worked in isolation." A non-profit, SAMSSA has been working to be that unifying force. It acts as a clearing house for news and offers its member companies marketing assistance and worldwide contacts.
Looks great now
With mineral prices soaring, mining is king in Greater Sudbury. Its nickel, copper and other minerals are exported worldwide.
It's not always been this way, however. In the early 1970s the city was an environmental disaster. Extensive logging, forest fires and pioneering nickel smelting techniques decimated most of the vegetation around the city.
It's green today, and in the process of repairing years of damage, the city won a number of environmental awards. The MS&S base could add reclamation experience to its resume. Today CVRD Inco's Superstack, once the tallest free-standing chimney in the world and still the city's dominant landmark, emits steam from the giant Copper Cliff smelter.
In the 1970s the Sudbury mining camp was transforming into a city. Community colleges and universities opened, each offering some form of mining degree as well as the curriculum found in any other large city. Mines could look to Sudbury for graduates who knew the language. But low commodity prices in the 1990s reduced mining and exploration in northern Ontario.
In 1993 Darryl Lake was the dean of health science, trades and technology for Cambrian College, a community college that began teaching in Sudbury in 1967. Lake recognized that Sudbury's brightest students typically left for the bright lights of distant cities. With mines downsizing, encouraging the small- to medium-sized enterprises (SMEs) to take root in Sudbury seemed to be the best way to reverse the trend and stimulate the local economy.
Inspired by technology innovation centers in Finland, the Northern Centre for Advanced Technology, Inc. (NORCAT) opened for business in Cambrian's basement in 1995. NORCAT got its own 32,000 sq. ft. building on the campus in 1998.
Thanks to healthy raw material prices (as of Oct. 5, nickel is at $13.62 per pound), mining is hot. At OEMs throughout Sudbury every square foot of the factory holds parts and machines being welded and bolted together for customers waiting (up to a year in some cases) to put them to work.
"Suppliers are so busy putting product out the door they don't have time to figure out how to make their machine better or to develop a new idea," says Dale Boucher, manager-prototype development, NORCAT. Expertise from the center's staff is accessible on a fee basis to help with developing new concepts. It can perform feasibility studies and assist with fabrication and testing. "When it gets to the production stage my department gets out of the way."
ORCAT can give an entrepreneur additional help, like writing a business plan or marketing. Mechatronics is the group's strength.
NORCAT rents laboratories and shop space for small companies to get started. When NORCAT celebrated its 10th anniversary in 2005, it had been involved with 150 new products. Half of the 41 companies it had helped start were still in business. In recent years NORCAT's roll has expanded from simply helping SMEs get started to where it also plays matchmaker, seeking large companies that would benefit from the skills possessed by local SMEs.
NORCAT's headquarters are at capacity, too, but relief is on the way. In September NORCAT CEO Darryl Lake announced that CVRD Inco had reinforced its support of the organization with a $2 million donation for NORCAT's new 40,000 sq. ft. Innovation and Commercialization Park. Construction of the building on the college's property is expected to be done by the summer of 2008.
NORCAT's work reflects the community. Three-quarters of its activity supports the mining industry. The new center will allow NORCAT to expand into other areas. "Although mining will undoubtedly always be a big part of NORCAT's work," says Lake, "we want to look at technology in general. We'll look for ways to take something used in forestry, for example, and adapt it to mining."
Adit makes it easier
NORCAT's laboratory work is balanced by its mine training and testing facility in the former Fecunis Mine, located on Xstrata Nickel land in Onaping, an hour northwest of Sudbury.
Safety indoctrination is required for any person employed by a mine or working as a contractor underground in Ontario. CVRD Inco and Xstrata Nickel look to NORCAT for training.
The month-long course for the hard rock miner common core program begins in front of the computer and moves to safety training at NORCAT's underground mine. This is followed by hands-on work where students go through the cycle of drilling, blasting, scaling, bolting and mucking. More than 2,000 students each year go through the program, which is taught by miners with decades of real-world experience.
While extracting paydirt isn't the goal of NORCAT's mine work, the mining is real. Students don headlamps to open drifts and ventilation passages following a plan. The mine gets deeper with each wave of students. The longest drift is 750 ft.
"We realized it wasn't a real mine if we weren't selling product," says Joe Morin, mine manager, NORCAT Underground Training Centre, "so now we sell the mucked rock to local contractors." NORCAT's LHDs are used to load on-highway trucks from a stockpile outside the mine.
The primary application of the mine is training, but it's also available to equipment manufacturers. The NORCAT mine can be rented for product testing or photographing new machinery in its natural habitat.
"The mine is unique because it is the only one like it open to the public," says Boucher. Others around the world are owned by a mining company or another OEM, and it's difficult to get access to the rock. We allow people to come in and rent the space. If a company needs it secure, we'll have the students open a drift or a room."
NORCAT Mine is an adit, a horizontal tunnel accessible through an opening in the side of the hill. There are no ramps or cages to contend with. More importantly, there's no danger of getting in the way of a haul truck.
Partners for efficient mining
Throughout its history CVRD Inco has performed an extensive role in product development. In 1982, Inco's Copper Cliff North Mine was established as a research mine. Advances were made in machinery automation as well as computer and laser technology.
Dr. Greg Baiden was a member of the Inco team that built one of the world's largest automatic guided vehicles in 1988, an electric truck with a 70-ton payload. It was put into production in the mine and used four years. The side-dumping locomotive-like truck traveled on 16 wheels. During its working life the tires were changed once, such was the level of electronic control, and the truck experienced only one failure. A track along the mine's roof guided it through the tunnels.
The truck was ahead of its time. It was eventually scrapped and has not been reproduced. "It would work today," says Baiden, chief technology officer at Sudbury's Penguin Automated Systems Inc. "There are some things I would change because the technology has advanced. Today laser scanners would replace the track, allowing the machine to travel throughout the mine."
The technology used in mining rarely gets the nod it deserves. "There's the perception that mining guys couldn't possibly be doing this type of stuff. It's quiet work with practical applications."
Before autonomous machines become popular, Baiden thinks it's more likely the industry will move into teleoperation, where vehicles are run by people in a cab replicator far from the production area. "Nobody is ready to press a button on 150 tons and let it go to work. Mines need time to gain confidence with that level of autonomy."
Mine pro shop
Inco established Continuous Mining Systems (CMS) in 1984 to design and manufacture mining machinery to improve its own productivity. CMS heralded one of the first steps away from extraction to technology and product development.
When Bob Lipic acquired CMS in 1994 and combined it with three other companies, his goal was a diversified mining equipment company that would ride out the highs and lows of the industry. Today he's president and CEO of that company, Mining Technologies Intl. (MTI). MTI is a major manufacturer of production equipment, the counterpart to Industrial Fab's utility vehicles. MTI designs and manufactures scoops, trucks, self-propelled drills (jumbos) and electric locomotives. MTI also produces scoop buckets and other wear parts, while a plant in nearby North Bay produces hydraulic cylinders for MTI's own equipment and other OEMs.
Although one of the largest home-grown manufacturers in Sudbury, "MTI is small enough to have the flexibility to offer products our competitors may not be able to provide," says John Dales, purchasing manager, MTI.
Progress has been made in standardizing equipment design and component selection, but it's still difficult to produce a one-type-fits-all machine for the Sudbury area, much less the world. The mines require different features for each location.
"There may be 30 items special to their machine that you don't use for another customer," says Bob Denton, account manager, MTI. "It ranges from painting the steps red to installing special lights or horns. If you're going to sell equipment into that mine, you have to comply."
Introducing cutting-edge features in mining isn't easy. "This may not be the place to introduce the newest technology simply because it's available," says Dales. "Often the newest technology is not applicable. In underground mining they want to be able to fix the machine with a crescent wrench."
The reluctance for adopting new technology like electronics should start to wane as components are proven to survive in a mine, and when users understand their advantages. Everett Henderson's work is helping to move the industry that direction.
An alumnus of CVRD Inco's product development team of the 1980s, Henderson started Minewise Technology Ltd. five years ago. The company's products and services involve diverse applications ranging from traditional vehicle electric sub-systems and remote controls to specialized video techniques particular to underground mining. Current projects include advanced vehicle traffic control systems, specialized material handling and dynamically controlled ventilation systems.
The fix-it-with-a-wrench approach may have slowed adoption of CAN bus systems in the mines, but in some cases it is already there. "With the use of electronic engines, CAN is more common in mining than people understand," says Henderson. "They use new engines and diagnose their problems, but no one really says a CAN bus is doing the integration. They just want it to work.
"We are trying to implement the technology in mines because the standards are powerful and will increase machine function. When adding tools we could tap into the CAN system and bring value to the end-user with an attachment that interacts with the engine. When we can explain the benefits of having fewer harnesses and a better response from hydraulic or the ease of making equipment available via remote control, operators will see the benefits."
The Northern Bermuda Triangle
Today CVRD Inco is still involved in product development, albeit in a different capacity. Most of the equipment in Sudbury leaves the factory fully assembled. If it's going to be lowered in a cage, a few tricks must be performed. Depending on the size of the cage, this can mean tearing the machine down, lowering the pieces on the cage and rebuilding it underground. It's an extra process that can cost the mine as much as $30,000.
CVRD Inco wanted to prove new machines above ground. It created a ramp with a 20% grade in an old open pit mine near Sudbury.
It's been called the Bermuda Triangle of the North because things happen to vehicles on the ramp test that never occurred in the past. The vehicles are pounded repeatedly by worst-possible situations that replicate real-world conditions. The Canadian Standards Assoc. (CSA) and other groups spell out specifications like safe stopping distances. CVRD Inco's test uses the standards, then cuts them by a third to make up for extended maintenance intervals.
What has grown out of — and continues to be — a way for CVRD Inco to ensure the equipment it buys is up to the conditions it will be working in has become a valuable asset to equipment manufacturers. For a fee, OEMs can use the ramp test to prove vehicles before moving into full production.
The guys at Industrial Fab have spent some time out on the ramp, which offers a nice view of the countryside while exposing man and machine to the effects of windchill.
"If something is going to go wrong you want to know about it early, says Industrial Fab's Rautiainen. "Part of that includes the customer in the design process. We can't afford to design equipment and not have it work." Testing is important, too. "With the ramp test facility we can get a successful product out faster."
Traditional support vehicles have a three-year turnover rate, says Berube. "After that time its condition has run out beyond its economic life. We have worked to extend that. Minecats have been working for five years because of the chassis design, approaching 10,000 hours. Ten years ago it would be having serious issues after 3,600 hours."
From Sudbury to the moon
Some of the research being performed in the Sudbury Basin — a geologist's dream created by a rock hurled in from outer space — isn't focused on the Earth at all. At NORCAT, Boucher's staff has connected mining to the space industry.
Several years of work with space drill prototype development led to a $3 million three-year contract from the National Aeronautics and Space Administration (NASA) to build a drill that can sink its bit 1 m into the moon's surface. Lunar mining is seen as a way to sustain exploration work. Shipping raw material into space is cost-prohibitive.
Working with Electric Vehicle Controllers Ltd., a local company, research has involved developing a highly abrasive moon dust simulant and installing a cryogenic test chamber that chills metal down to -235 C. Boucher will be required to test the drill in moon-like conditions, for which a room has been cut out by mine students for a hypobaric chamber.
Technology discovered along the way to the moon has applications in terrestrial work. NORCAT was recently approached to help one of the mine companies develop a special drill bit for its smelter, while EVC has retained the underground rights to use a business-card-size moon drill controller.
"The work on the space project has been a collaborative effort," says Jim Richard, vice president of technical sales, EVC. "NORCAT has a network of entrepreneurs that can transfer this technology back to other industries."
NORCAT hosts the annual Planetary & Terrestrial Mining Sciences Symposium, where sessions cover subjects like rover payloads and machine guidance.
Penguin Automated System's Baiden is research chair for robotics and automation at Sudbury's Laurentian University and chief technology officer at Penguin, the company he started last summer. Much of his work has centered on getting the operator out of harm's way, regardless of where that harm is located.
"We have been looking at deep ocean mining," says Baiden, "where people are never going to be able to work safely. Submarines have communication umbilicals attached to them. In a mining operation with multiple machines things would get tangled." Technology developed by Baiden's group allows subs to be run together, wirelessly, communicating between them and a boat.
"Much of this work is going on under the radar screen. It's unusual for mining guys like me to get calls from space agencies and the military." That is changing. The impetus behind the submarine project was a telephone call. Knowing Baiden's expertise with teleoperation, the caller asked him to help solve some challenges standing in the way of orbiting space solar power.
"Construction on such a big project would have to be done through teleoperation, as sending thousands of workers into outer space would simply not be practical. One of their biggest hurdles was how to direct the construction equipment from Earth.
"Because I have a mining background, we took a practical approach. Instead of building tanks costing millions of dollars, we're using the lake in front of my house, and the lab is a pontoon boat. Mini submarines act as the space craft. The water gives weightlessness. Once the technology is proven by the mini submarines floating in the lake, it can be scaled up to space work."
There's more to come. "Sudbury is an interesting place right now," says Baiden. "There is a renaissance going on centered on mining equipment."