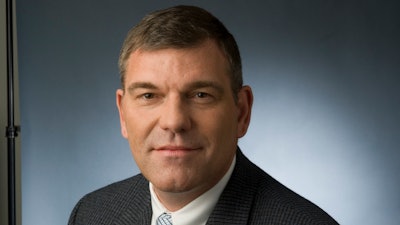
Responses from Nathan Sheaff, founder and CEO of Sciemetric Instruments
The Industrial Revolution 4.0 (IR4.0): Data, Connectivity and Automation
What does “Industrial Revolution 4.0” mean to your company?
Our team works with manufacturers to help them increase yield, improve quality and optimize their processes. We do this by adding advanced technology, sensing and analytics to the plant. That means we’ve been doing pieces of what’s now called “IR4.0” long before we even knew what to call it, by measuring, recording, analyzing and digitizing the data generated by all the processes on a line.
In some industries, such as off-highway, this was often a tough sell, because production volumes weren’t high enough to force the need for greater automation, which in turn, drives a willingness to adopt new technology. For the longest time, factories in many industries were underfunded with the philosophy of “let’s make it as cheaply as possible,” but this has changed. Manufacturers have come to appreciate the value of squeezing all they can out of their technology and their data to make better parts because this can save them a fortune. Plant managers are finally getting the latitude to innovate, to invest. This validates what we’ve been saying for years and helps us refine the message we take to the market.
What role do any of the following branches within the IR4.0 play within your company and/or product designs?
Big Data (Smart Data) – acquisition, management, extrapolation and presentation
I’ve been in so many factories where data is siloed, where you can’t correlate or organize it to understand causal effect. Data by itself is useless – it’s a means to an end. In this context, that end is to make better parts or eliminate a warranty recall. If your data is trapped in silos, or unorganized and lost in that deep, dark data lake, it’s not doing you any good. In reality, we’ve been working in the big data space for 20 years or more with real-time, multi-terabyte databases. When we talk about big data, it’s about how to organize and structure it so you can squeeze value out of it fast. We’re acquiring the data from many machines, sensors and processes on the floor, and managing it by putting it into an organized data model. Google showed us how you can unlock value from data quickly if you organize it so that its accessible and easy to correlate and visualize.
Automated Systems and Vehicles
We don’t look at this in terms of fleets and vehicles out on the worksite, but in terms of tooling and processes and machines in the factory. What we try to do is gather all the pertinent data from all the automated processes so you have a digital flight recorder that allows you to retrace your steps and analyze for continuous improvement.
Are there other branches or areas of focus?
It’s long been common in manufacturing to look at statistical averages, to look at lots of hundreds or thousands of parts in a pool, rather than at single parts. But this approach doesn’t help you track down that one in a thousand that could lead to a warranty claim or a mass recall. What we do is provide manufacturers with a digital fingerprint for every part made – the means to track the attributes of a part right down to the individual serial number. It takes this kind of big data analysis and scientific process to understand and catch failures early, find root causes and prevent costlier problems down the road.
What is the opportunity potential, and what benefits are you already seeing?
It’s a great pity when a latent defect that should have been caught in the plant sneaks through – like a $600,000 truck that’s shipped to Indonesia brought down by an oil leak caused by a missing bit of silicon or a faulty hose clamp. But better tools for measurement, data analysis and data visualization are already helping manufacturers dramatically improve yield and reduce warranty claims. In the off-highway industry alone, billions of dollars can be saved by avoiding defects, to increase production volumes and improve deliveries. Almost all customers can fix a problem if they know what to fix, but they need help to pinpoint the root cause. This requires better access to the data, with the right dashboard and real-time reporting so they can take action now, rather than be stuck waiting till tomorrow by which time they may have already passed a thousand more faulty parts.
How do you foresee the IR4.0 affecting the industry as a whole? Are there any new or improved opportunities it will enable?
The people who embrace IR4.0 and all that entails are going to be big winners. It’s a fundamental change in the landscape that can’t be ignored. Companies that embrace it, challenge their employees and architect this technology into their processes early will be the winners by a long shot because it will take years. Even though it seems easy, it’s not as simple as just plugging in a server and collecting some data from a bunch of sensors. There’s a lot of things that have to change in how some plants operate. The early adopters will gain a great advantage as they optimize their processes and the laggards are going to have a hard time catching up. They won’t be able to compete because the other guys will already be faster, better and cheaper.
Challenges on the Horizon
What new challenges have arisen that effect the way your company designs or manufactures its products? How it does business? How it goes to market? How it differentiates itself from the competition?
We’ve been heavily investing in R&D and engineering for years and engaging with a host of manufacturers to understand what they need, what they want to see and how they want to see it, to do their jobs better. It often comes down to speed – collecting more data faster, analyzing that data and generating pertinent reports, faster. We’re past the point where we need to experiment to give a customer what they ask for because we’ve already invested the time to understand their reality.