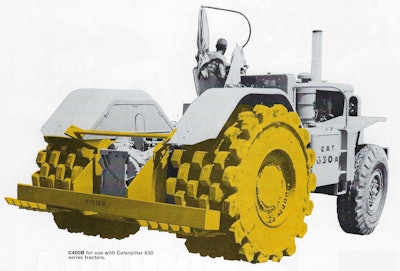
Earthmoving productivity increased markedly as technology and mechanization, especially in motor scrapers and off-highway haulers, evolved. But no matter how much more material could be hauled per cycle or how much faster it could be moved, the equipment working on the fill had to be able to keep up.
Going into the 1950s, most embankment compaction was handled by sheepsfoot rollers pulled by crawler tractors. In some cases, notably construction of the Pennsylvania Turnpike from 1938 into 1940, three-wheeled rollers were used for earth compaction. Either method did the job, but was limited by the speed of the roller or tractor. Even if sheepsfoot rollers were ganged behind a powerful enough tractor, the work was limited by the tractor’s slow speed.
Rubber-tired tractors had a major advantage in speed over crawler tractors, and the rubber-tired tractors that had pulled scrapers often remained useful after the scrapers wore out beyond economical repair. So why not use them for compaction?
Exactly how to do this took many forms. A single-axle prime mover worked well with a towed sheepsfoot or 50-ton rubber-tired roller, combining both speed and maneuverability. The most common idea for the two-axle tractors was to replace their drive tires with sheepsfoot, padfoot or grid compaction wheels. On occasion, they also pulled rollers, with even more speed but less maneuverability than those drawn by single-axle tractors.
Both methods of employing scraper tractors in compaction work suffered a pair of drawbacks. One was that the tractors, especially those with compaction wheels in place of drivers, were doing work they weren’t really designed to do and so were less efficient than a purpose-built compactor would have been. The other was that they didn’t have a dozer to spread material if needed, although some of the two-axle machines received custom dozers.
Industrial tractors were, of course, often used to pull rollers, especially in subgrade and finish grading applications. Two-axle, pulled pneumatic rollers were most often drawn by them. Indeed, today many tractor pull tracks use farm tractor and pulled pneumatic roller sets for track maintenance. In addition, the front axle of some industrial tractors could be replaced by a single vibratory drum.
The Historical Construction Equipment Association (HCEA) is a 501(c)3 non-profit organization dedicated to preserving the history of the construction, dredging and surface mining equipment industries. With approximately 4,000 members in twenty-five countries, our activities include publication of a quarterly educational magazine, Equipment Echoes; operation of National Construction Equipment Museum and archives in Bowling Green, OH; and hosting an annual working exhibition of restored construction equipment. Our 2018 show will be August 24-26 at the Le Sueur Pioneer Power Show, Le Sueur, MN, USA. Individual memberships within the USA and Canada are $35 for one year, $65.95 for two years and $99.95 for three years, and $45.00 US elsewhere. We seek to develop relationships in the equipment manufacturing industry, and we offer a college scholarship for engineering and construction management students. Information is available at www.hcea.net, or by calling 419-352-5616 or e-mailing [email protected].