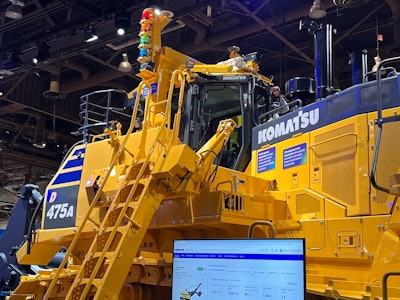
MINExpo 2024 in Las Vegas dominated three of the four main halls at the Las Vegas Convention Center with everything from dump trucks, excavators, drills and much more on display for the thousands of attendees.
The exhibits, at their biggest, felt a little more like a theme park in the best sense. It wasn’t just about seeing the exhibits; they encouraged interactivity. There is definite perspective when someone sits in a 75-foot-tall machine that weighs several hundred tons and costs millions of dollars.
These machines are digging deeper and deeper into the earth and are responsible for many of the elements and minerals people have come to depend on. The job is getting tougher, though, and companies are trying to balance their immediate needs while ensuring the machines are operating safely and efficiently.
The global mining challenge, according to Komatsu Mining Business CEO Peter Salditt is: “As the world electrifies, there is a need to sustainably obtain more minerals from increasingly complex environments.”
Automation also can help companies navigate these complex environments and augmented reality (AR), simulation and remote monitoring are making the process easier.
A key example is their Modular ecosystem, which was on display at MINExpo, is a set of interconnected platforms and products designed to simplify existing workflows and create a single source of truth for the common data gathered across their mining operations.
Brian Fox, senior vice president of mining strategy and innovation for Komatsu said about automation, “It’s not a linear path. We need to listen to customers to prioritize their needs.” He added the mining industry’s pathway to automation is helping it catch up with the advances happening in the automotive industry.
Those needs are constant and need a quick and rapid response to minimize downtime. At the Scania booth, sales manager Andres Kohring described their assistance platform, which is designed to provide solutions to customers in the United States and Canada within 24 hours.
He also explained how their DC motor series is designed to be modular and easy to replace without causing the consumer to do a rip-and-replace, which is far more expensive and adds to downtime. Kohring said this was part of their larger objective, to focus on four key areas: Performance, sustainability, reliability and transition. All four, he explained, are supposed to work together to keep consumer costs down while also allowing Scania the ability to remain active with their customer base.
They also displayed an AR tool through a tablet that allows the user to virtually take their DC13 engine—a model—apart and analyze the changes the company has made to their design as well as information about the engine itself.
Improving energy efficiency and performance
Technology improvements aren’t just limited to large machines and engines. The components from within.
For example, Erik Larson, a product sales manager at Parker Hannifin highlighted the company’s Force Command Electro-Hydraulic Linear Actuator (EHA), which is designed for mobile construction applications and uses a brushless motor. He said the user also has full command over the speed and sensing of the stroke and can extend and retract at certain speeds.
Larson said additional benefits include longer life expectancy, improved efficiency gain and lower power consumption.
Another product designed to improve life expectancy was the CENTAMAX from Regal Rexnord. It has torsional flexibility and elasticity to help shift critical resonances below operation speed. The drive is then subject to only minor continuous vibratory torques, protecting and extending the life of the engine.
Rene Klimach, global product manager for Regal Rexnord, explained how the vibration is harmful to a drivetrain and can lead to gear issues and cause friction and abrasion. Keeping the critical resonances safe through calculations can help users understand there are certain RPMs they don’t want to operate at.