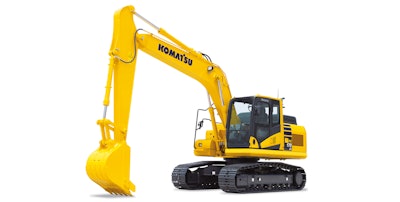
Komatsu Europe International N.V. introduces the PC170LC‐11 hydraulic excavator to the European market. Featuring all the advantages of the latest Komatsu “‐11” range, it further leverages Komatsu’s leadership in technology and innovation with an environmentally friendly EU Stage IV engine, up to 3% improved fuel efficiency and up to 5% increase in power output during boom raise and swing. The cab’s design was upgraded, safety and serviceability enhanced, productivity maximized and operating costs were reduced.
KOMTRAX telematics and the Komatsu Care maintenance program, offer top fleet management and support, protect the machine against misuse and guarantee maximum efficiency and uptime.
With an operating weight range of 17,900‐19,100 kg, the PC170LC‐11 hydraulic excavator is an ideal machine for safe work on multiple job sites. Its Komatsu‐designed SAA4D107E‐3 EU Stage IV emissions‐certified engine is more environmentally‐friendly and maintains the proven performance of the previous series while reducing daily costs and fuel consumption. Productive, dependable and efficient, it has a net horsepower of 121 hp (90 kW).
Alex Visentin, Product Manager at Komatsu Europe International states, “The new PC170LC‐11 is a versatile machine with many options. It represents a good choice for many customers looking for the best match between size and performance. Significant advances in fuel consumption were made, along with enhanced productivity thanks to an increased power output and improved lifting performance.”
Komatsu EU Stage IV emission certified engine
Komatsu’s new EU Stage IV engine integrates SCR (Selective Catalytic Reduction) to further reduce NOx emissions using the AdBlue additive. With an advanced electronic control system that manages the airflow rate, fuel injection, combustion parameters and aftertreatment functions, the engine optimizes performance, reduces emissions and provides advanced diagnostic capability. Customers benefit from lower fuel consumption with no loss of performance.
To ensure product reliability and durability in demanding conditions, Komatsu developed the entire system, including the control software, which is critical to the effective operation of the aftertreatment system. This control system is also integrated into the machine’s on‐board diagnostics systems and in KOMTRAX, Komatsu’s standard telematics system.
Higher Power output = Greater Productivity
A 5% increase in power output during boom raise and swing, with the same engine speed as the previous Komatsu PC170, gives the PC170LC‐11 higher productivity along with a 3% average fuel saving, faster cycle times when loading, and precise work in combined movements.
Highly efficient hydraulic system
Enhancements were made to the hydraulic system for reduced hydraulic loss and improved efficiency. All major components on the new PC170LC‐11 including the engine, hydraulic pumps, motors and valves are exclusively designed and produced by Komatsu. This integrated design uses a “closed center load sensing” hydraulic system that takes hydraulic efficiency to the next level using variable speed matching: engine speed is adjusted and optimal power and efficiency ensured, no matter the job.
Operator environment
The PC170LC‐11 comes with 3G communications, improved operator comfort, and new safety features.
The new viscous fan clutch system controls optimal cooling fan speed, reduces fuel consumption and also contributes to lower in‐cab noise, down to 68dB(A) the quietest in‐class. A comfortable work environment further helps operators to maximise productivity. The proportional control joysticks, which are standard, allow precise operation of attachments with comfort and ease. The addition of a new Neutral Detection System reduces the risk of inadvertent operation.
The ROPS certified cab, specifically designed for hydraulic excavators, is mounted on viscous isolation dampers for low vibration levels and gains strength from a reinforced box structure framework. A standard heated high back air suspension seat comes with newly designed fully adjustable armrests for improved comfort. In addition to the standard radio, external devices can play music through the cab speakers thanks to an auxiliary input. The cab also has two 12V power ports for the operator’s convenience.
A high‐resolution 7 in. LCD widescreen colour monitor features enhanced capabilities and displays information in 26 languages for global support. The operator can easily select up to six working modes to match machine performance to the application.
The new monitor panel provides information on AdBlue fluid level, Eco guidance, operational records, fuel consumption history and utilization information. For improved safety, a standard rear‐view camera gives the operator a wide landscape view of the area directly behind the machine and is now incorporated, along with the gauges, as the operating default screen.
Komatsu’s optional “KomVision” can further enhance safety through a system of multiple cameras. Jobsite surroundings can then be checked on the monitor prior to carrying out any operations.
Convenient maintenance and serviceability
The PC170LC‐11 provides easy service access to help reduce costly downtime. The new model has guardrails on both sides of the upper structure for easier accessibility. The radiator and hydraulic oil coolers are mounted side by side, making it easier to maintain and service when required.
The excavator is equipped with the exclusive Komatsu EMMS (Equipment Management Monitoring System), which has enhanced diagnostic features that give the operator and technicians greater monitoring and troubleshooting capabilities. EMMS also continuously monitors all critical systems, preventative maintenance, and provides troubleshooting assistance to minimise diagnosis and repair time.
The Komatsu Diesel Oxidation Catalyst (KDOC) has an integrated design allowing this simple system to remove soot using 100% “passive regeneration” without the need for a Diesel Particulate Filter (DPF). Unlike a DPF, the KDOC does not have a scheduled replacement interval and is designed for long life with no maintenance required. Less complexity and truly seamless operation for the operator means lower owning and operating costs.
Komatsu uses a Variable Geometry Turbocharger and an Exhaust Gas Recirculation valve, high‐pressure common rail fuel injection for precise air flow management and more complete combustion, eliminating the need for a DPF.