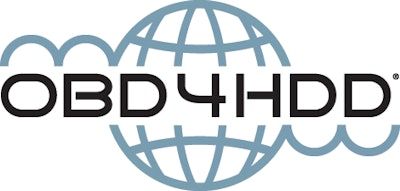
The heavy equipment industry has truly become an international marketplace as equipment and component manufacturers continue to expand their presence across the globe. Companies are no longer limited to operating in one region or country but instead can expand across continents to gain new customers and provide more localized service to existing ones. “The world’s getting smaller. When you look at some of the larger companies, they’re not just U.S. companies any longer, they’re international,” says Mark Benishek, Technical Director at the Association of Equipment Manufacturers (AEM, association information, 10093568)
However, with this expansion has come the need to develop design processes and standards which are consistent across the globe to ensure continuity, safety and reliability of products. “It [doesn’t] matter anymore if you have a tractor built in the U.S. and you buy an implement that was built in the Netherlands,” says Benishek. What matters, he says, is the two pieces of equipment need to work together properly, and organizations like AEF are helping to make this happen through the development of international guidelines.
While entities such as the International Organization for Standardization (ISO) develop global standards—which it should be noted are voluntary consensus standards which manufacturers are not required, but encouraged, to follow—these sometimes aren’t enough to meet all of the needs of the international marketplace. To help fill the gap, many associations have taken it upon themselves to create best practices and standards for the global industries they serve.
Making two ends meet
As agricultural equipment, particularly tractors, has become more sophisticated in recent years through the increased use of electronics, customers discovered that if they bought an implement from a different manufacturer than that of the tractor, the two pieces would often not work properly once connected to one another. Seeing how this issue affected customers, a group of agricultural equipment manufacturers joined together with AEM and the German manufacturers association VDMA (association information, 10278036) to form the Agricultural Industry Electronics Foundation (AEF, association information, 10281014).
AEF focuses on further expanding the ISOBUS standard (ISO 11783) to help create compatibility between electronics systems. According to Benishek, who is also Secretary of AEF, ISOBUS lays the groundwork for electronics systems to properly communicate with each other. “AEF has worked hard to develop guidelines that provide more definition to the ISOBUS standard by splitting the complex ISO standard into so-called functionalities,” he explains. “The main reason was the different levels of implementation of the ISO standard in the past. The latest guidelines will make it easy for customers to find out what functionalities the standard will support.”
The latest AEF project to be released is the AEF ISOBUS Conformance Test tool and AEF ISOBUS Database (learn more, 11145167). With the conformance test tool, manufacturers will be able to determine if their equipment complies with the ISOBUS standard. If compliant, the manufacturer can then upload to the international ISOBUS Database the information about the equipment’s ISO compliance. “The idea is that as we fill up this database with all the equipment that is ISO certified, people—dealers and farmers—would be able to go to a screen, pull this information up, and actually see what functions on this tractor will work with implements,” explains Benishek. “There are some features of the database which will also help you with diagnostic issues if there are problems.”
Equipment determined to be ISOBUS compliant by the conformance tool will have a decal applied which says ‘AEF Certified ISOBUS.’ This will enable better recognition of which pieces of equipment will be compatible with one another. Launched in September of this year, AEF expects the decal will be visible on equipment being displayed at Agritechnica 2013 (event information, 10265518).
In addition to its work with ISOBUS, AEF has begun developing guidelines for camera networks and high voltage drivetrains within agricultural equipment. “We think there may be a future for some high voltage, electric vehicles even in farm equipment,” Benishek says. AEF has set up a project team to investigate the directions high voltage drivetrain technology may be headed and begin building a framework from which guidelines can be developed. By having these guidelines early on in the development stages of the technology, manufacturers will be able to design compatible systems from the very beginning. “The whole idea here is to work together to provide products that work as expected for the customer as we move into the future with new products and new ideas,” says Benishek.
Communicating on the same level
CAN in Automation (CiA, association information, 11118466) was established in 1992 to promote the use of CAN (Controller Area Network) technology in various markets. “We help mainly the system designers and system integrators to get standardized products on the market so they can buy from different sources and not [be dependent] on one supplier,” explains Holger Zeltwanger, Managing Director of CiA.
Once established, CiA undertook the development of the international CANopen standard. Similar to J1939 established by the Society of Automotive Engineers (SAE), CANopen provides a common consensus of specifications for CAN systems to help ensure design commonality on a base level so that CAN systems can easily be integrated with other systems, components and equipment. “We developed the CANopen standard and hold the specifications,” explains Zeltwanger. “We submit them also if necessary to international standardization parties, [and] some of our specifications have been internationally standardized by IEC or by ISO.”
According to Zeltwanger, anyone from component suppliers to OEMs to universities can be a part of CiA and provide input on the development of CAN standards. Having a broad range of people with varying interests involved in the process provides a wider breadth of input that helps ensure the standards will meet the needs of everyone. Zeltwanger says that while the majority of participants are still suppliers of CAN systems, more OEMs are getting involved every day. “[OEMs] want to influence those standards and they want to make the CiA organization independent of those suppliers,” he says. “We appreciate when [OEMs] are members of CiA…[it makes us] consider the objectives of the OEMs. Otherwise, the suppliers would do what they want and that is not a good idea.”
Zeltwanger explains that while suppliers want standardization to an extent, they also want to keep the details of how their CAN technologies work proprietary. OEMs, on the other hand, want CAN systems to be highly standardized to make it easier for them to incorporate the systems into their designs as well as easier to fix when necessary. “We should always find a compromise between both,” he says, which is where CiA steps in as a neutral party that takes into consideration the wants and needs of both sides to develop standards. And because CiA writes and maintains all of the standards documents, the chances that a single party will suddenly make changes to the standard are eliminated. “That is why so many OEMs are afraid of proprietary standards,” says Zeltwanger, “because they never know if their supplier decides one day to disappear. [The OEMs] want to keep the business going and this means you need some neutral instance that maintains the specifications.”
CiA’s newest project involves the development of standards for CAN-FD, or CAN flexible data rate, the next generation of CAN technology that has slowly begun making its way into the industry. According to CiA, its new standard will focus on specifying physical layer implementations for various applications; standardization of CAN controller user interfaces which support old and new CAN protocols to help simplify development of low-level driver software; and harmonization of system design when incorporating the old and new CAN communication technologies into a network system architecture. Zeltwanger says CiA has submitted its new standard to ISO for international standardization.
Designing healthier operator cabs
Formed in 2012, the International Society of Environmental Enclosure Engineers (ISE3, association information, 11132210) brings together OEMs, cab designers, occupational health and safety professionals, inventors and business people from around the world to focus on the society’s mission which is to reduce lower lung disease caused by work place exposure to respirable pollutants explains Jeff Moredock, Managing Director of ISE3.
In order to achieve this goal, ISE3 members work together to promote either existing methods or develop new ones that lead to a common sense best practices approach to designing, testing and certifying operator cabs. As part of this approach, ISE3 aims to encourage the development of enclosures which meet applicable standards for enclosure air quality. “ISE3 will promote any standard, technology or research that, when applied in the real world, improves enclosure effectiveness,” says Moredock. “The goal is to achieve effective real world performance that can be continuously maintained on machines operating in their working environments.”
Through its Comprehensive Scoring Method (CSM), ISE3 has provided a means in which enclosure manufacturers can have their designs objectively scored for air quality performance. The CSM uses a single number to show the effectiveness of an enclosure in protecting operators and electronics from respirable dust. ISE3 provides certification services to manufacturers by sending a trained technician to objectively test and score the cab using the CSM method. The ultimate goal is to offer a means of providing consumers with critical information about the enclosure, similar to the Environmental Protection Agency (EPA) sticker on the window of new cars. This will enable them to make an informed decision about whether or not they want to purchase that enclosure.
In addition to the CSM, ISE3 has developed a Best Practices Handbook outlining the various components currently used in the design, construction and use of environmental enclosures, and how these components work to either improve or compromise air quality in enclosures. Pairing use of the handbook with the CSM helps provide a better means of developing as well as using and maintaining operator enclosures.
Fluid power standardization
Originally organized to help bring more standards to the fluid power industry, the National Fluid Power Association (NFPA, association information, 10055830) works with ISO through the technical committee ISO/TC 131 to help develop standards on an international level. “Standards are the technical language of trade,” says Karen Boehme, International Standards Development Manager at NFPA. “International standards for fluid power help trade between nations and between suppliers and customers by providing global technical agreements that can be used to communicate and specify requirements.”
The main goals of the fluid power standards include:
- ensuring the safe and efficient use of fluid power components and systems;
- reducing unnecessary variety; and
- assisting communication about the technical aspects of fluid power (e.g., graphical symbols, circuit diagrams, supplier literature).
“Those who purchase products that conform to ISO standards have confidence that they know what they are getting, and manufacturers that make products that conform can expect to find a broader market for those products,” says Boehme.
NFPA brings together members of the U.S. fluid power industry—everyone from component suppliers to OEMs—to provide input on international standards development. Taking into consideration the thoughts of those who work with the technology is important as they have a first-hand perspective on how it operates and will be the ones incorporating the standards into their designs. Manufacturers can get involved by volunteering to be a part of one of NFPA’s U.S. Technical Advisory Groups (TAG) to ISO/TC 131. Serving as secretariat of the U.S. committee that provides the U.S.’s input into standards developed by ISO/TC 131, NFPA is directly involved in getting the input offered by its members and U.S. TAGs to the ISO technical committee.
Boehme explains that much of the work developing ISO fluid power standards is driven by national fluid power associations like NFPA, and as a part of ISO/TC 131 it often works with other associations such as VDMA in Germany and the British Fluid Power Association in the United Kingdom. She adds that ISO/TC 131 also coordinates with other ISO technical committees that use fluid power such as the committees for earth moving and agricultural machinery.
Among other projects, NFPA is currently assisting with the development of ISO/DIS 16908, focused on providing a standard method of thermal conditioning and cold start-up simulation testing for hydraulic filter elements. “The standard will allow for users of hydraulic filters to specify cold-start performance requirements,” says Boehme. NFPA is working with 12 other nations—mainly China, France, Germany, Italy, Japan and the United Kingdom—on the development of the standard, which is at the Draft International Standard stage at the moment. Boehme says the standard is expected to be published by mid-2014.
On-board diagnostics
The On-Board Diagnostics for Heavy-Duty Diesel Special Interest Group (OBD4HDD SIG) is an international non-profit organization which works to identify and inform the engineering community about on-board diagnostics (OBD) technologies for heavy-duty equipment.
Members consist of representatives from heavy-duty vehicle manufacturers and suppliers, and are organized into six focus groups:
- Diagnostic Communication
- On-Board Emission Monitoring
- Diagnostic Strategy
- Off-Board Diagnostic Tester Architecture and Technology
- Legislation and Harmonization
- On-Board Diagnostic Infrastructure
According to Peter Subke of OBD4HDD SIG, the majority of the organization’s members have an engineering background. “They are involved in the development, testing, production and the service of vehicles, machines and sub-systems being controlled by electronics,” he says, which gives them a keen understanding of how the OBD technologies work and the ability to properly explain them to others within the industry.
As part of its efforts, the organization publishes various documents designed to bring a common understanding of OBD technologies to the industry. Topics include information on emission control systems, OBD diagnostic protocols, legislative requirements as well as abbreviations and glossaries of common terminology. “Principle for success is the exchange of technical information between the SIG members as well as the elaboration and publication of documents for a common understanding of the HDD-specific aspects of the technology,” explains Subke.
Though it has no plans to develop any standards related to OBD but rather focus on disseminating information about it to the industry, Subke says OBD 4HDD SIG supports organizations which do develop standards including SAE and ISO, as well as legislative bodies such as the EPA, CARB and EC.