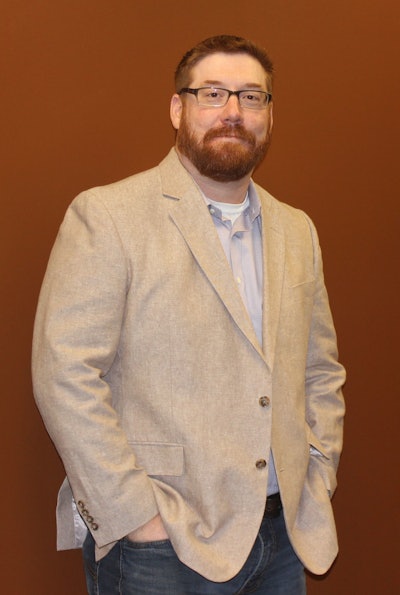
responses submitted by Mike Terzo, CEO/CTO, Hydrapulse Inc., and Rob Kindt, CMO, Hydrapulse Inc.
Global Markets
In previous years, the BRIC countries were the primary areas of focus for global expansion and investment. Since then, Brazil and Russia’s prevalence seems to have waned. What do you consider to be the strong markets for opportunity around the world?
MT: Our focus is on the electrification and hybridization of off-highway equipment. The markets that we see as the largest growth opportunities are in North America, China, and Europe. Markets that are embracing the continued integration of electronics and fluid power are best situated for growth in the next two decades. Companies in these markets understand how advanced technology can provide increased revenue and value to have a strong and sustained growth.
Are there new regions of interest? What particular industry or equipment type are you looking to expand in these regions and why?
MT: Our entire focus as a company is the emerging electrification of mobile equipment. We are not talking about electrification in the sense that off-highway vehicles are going to run solely on batteries, rather, how electrification of fluid power, drivetrains, and auxiliary functions can be expertly integrated into vehicle platforms to address a given markets’ needs. One example is the need for higher and more coordinated motion control on agricultural vehicles. Farmers are looking for ways to increase yield, reduce the amount of chemicals applied to the land, and more efficiently deal with the labor shortage. A traditional fluid power architecture presents many challenges whereas an electrohydraulic solution with precise, closed loop control can help OEMs design their vehicles for these specific needs.
Politics & Government
What potential policies are you keeping your eye on that could impact (or have already impacted) your company, for the better or worse?
MT: Tariffs certainly will play a role in the short term but what we are seeing is driving our long-term approach to the off-highway market is the emissions and energy regulations coming out across the world in various forms. For example, California passed SB 32 in 2016 which requires a 40% reduction in emissions by 2030 and they just passed SB-100 which requires the entire state to be 100% renewable energy by 2045. Keeping politics aside, these types of regulations have historically had huge impacts on the off-highway markets (EPA Tier 4 for example) and are set to continue that trend.
How have or will these policies (or lack of policy) hurt or benefitted your business?
MT: The tariffs have definitely hurt our business from the increased cost of goods standpoint but we have quickly adjusted. We are a small company so these types of adjustments are much easier to handle than larger companies. The various existing, new, and proposed emissions standards for off-highway has definitely helped our business. Since we are in the business of vastly improving the efficiency of off-highway equipment and fluid power systems in particular, we can provide solutions and/or advise to OEMs that are grappling with new standards.
With the benefit of the Tax Cuts, how have you used this to reinvest in your company?
MT: Here in California, the federal tax cuts have not had the same effect as other states and we have not seen much on the business side that impacts us either negatively or positively.
Diesel vs. Electric
Do you think there will always be a place for diesel powered equipment for heavy-duty applications? Why or why not?
MT: Currently, there is no cost-effective means of having a drop-in replacement of diesel. While we can electrify some or all of the functions on an off-highway vehicle, we still need the prime mover to generate the power (either electrically or mechanically). While it can’t be denied that as alternative fuel infrastructure is improved, the use cases for CNG, hydrogen, etc, gets better and better, there is just no getting around the torque and energy density of a diesel engine. We hear pretty often about “when battery technology catches up…..” that we can have all-electric off-highway vehicles and diesel is a thing of the past but that is just not reality right now. Therefore, we have focused on providing technology that can not only significantly improve the energy efficiency of current fluid power systems, but also operate on the high DC bus voltages of current and future hybrid or all electric vehicles.
What would electric power sources have to achieve in order to replace the diesel engine for heavy-duty applications?
MT: The shortcomings in an all-electric application has to do with the battery storage capabilities, available current (amps) for a given size, recharge time, and of course, cost. This means that battery costs and density would need to make major improvements to be able to power off-highway equipment. Even if the battery “magic bullet” was found today, it most likely would take a decade or more to scale up to any meaningful volume. And even if this happened, one could imagine the automotive industry taking precedence in the supply chain. So what we are seeing is that there is a large demand and growth opportunity in technology that can provide stepping stones from diesel to all electric, such as hybrid systems.
How do the diesel bans in several major cities around the world play into the direction your company is taking for electric vehicle development, if at all?
MT: Since our company completely focuses on the electrification and hybridization of off-highway equipment, these types of policy changes do not affect our business strategy. Our parent company currently has a project being funded by the California Energy Commission to demonstrate non-diesel hybrid power systems for heavy-duty, off-highway equipment to address these exact types of challenges.
What do you think is the next step for emissions regulations after Tier 4 Final and Stage V?
MT: Next steps for emissions regulations after Tier 4 and Stage V will be the eventual banning of diesel engines which we see already happening. The ability to do this is a long way off, but it is already creating a huge push in alternative fuel systems, energy storage technology, and all-electric solutions that will open up lots of opportunity for companies in heavy equipment and fluid power.
How are you looking at engine system design and development for the future? Modularity? More integrated sensors? More compact design?
MT: While the growth on the engine side over the last several decades has been focused on the large power platforms (200 hp+) we are focused on the smaller displacements that can work in hybrid applications. Since these types of systems downsize the diesel engine, we see that smaller engines that have full J1939 control will be growing in popularity and use. Also one of the most important aspects we see coming out of the engine manufacturers are multi-fuel platforms that can allow us to run either diesel or gas, or even CNG, with the same reliability that is required in the off-highway market. Engines need to be easier to integrate into a platform and provide more flexibility of fuel sources.
IoT & Connectivity
How is your company investing in IoT services and opportunities?
MT: Our company’s product is designed from the ground up to take full advantage of the IoT. We have invested our core development efforts to be able to have easy software integration into the multiple IoT platforms that are emerging. While we do not think that the IoT is a primary market driver right now, since its still uncertain in most applications how an OEM can actually monetize the value of the IoT, it is critical to be able to provide our customers with future-proof integration ability. So in short, we see IoT has a large growth potential opportunity. It is still unclear as to how big that potential is. In the meantime, we will continue to invest in gaining as full and deep of understanding of the IoT and its advantages as possible.
If you have already implemented some IoT opportunities, how has it affected your company? What are the long-term hopes or goals?
MT: Our long-term goals with IoT are to keep our products running longer, more efficient, and provide a better solution for our customers. We hope to perfect predictive and scheduled maintenance for our customers while providing data that is the most useful for their particular application. We see that every customer has a different need and finding the dataset that can make them more successful will be the best long-term goal.
Do you see a path toward the use of AI, VR or AR in your manufacturing processes, or even on board the vehicle itself?
MT: In regard to our products, we don’t see a valuable path forward yet for VR or AR but we do see some very good use cases for AI. We are implementing machine learning into our products at the chip level to provide benefits that up until now have been unheard of in the fluid power industry. This will absolutely be on vehicle but we feel it will have the most value for the automation of specific functions and/or other micro-value drivers that have not even been thought of yet. The constant march of automation will most likely accelerate leading to semi-autonomous vehicles and any component that provides an easier way to do this will be well positioned for growth.
How do you see connectivity and machine learning changing the vehicle landscape in the next decade?
RK: Connectivity and machine learning will revolutionize the industry over the next decade. It will happen at different levels. For an OEM, that could mean more visibility into their supply chain, predictive maintenance, or enhanced performance abilities.
Machine learning can help us tune our pumps for longer life, better efficiency, or a better supply chain flow for our customers. The “smart pump” will be able to see trends over time and make adjustments on the fly. For instance, if the pump sees a new pressure spike on initial start-up, it may choose to ramp power for the first 50 milliseconds in order to eliminate the pressure spike. This would lead to improved seal life, or even overall system longevity. This may happen with the instruction of the user or be allowed to happen unknown to the operator. Modern cars and trucks do this all the time such as the constant tuning of the fuel/air mixture, transmission performance, or aftertreatment system.
What concerns do you have with these technologies, their integration, and their means vs. ends, if any?
RK: Technology added to mechanical systems that have been perfected over the last 100 years is going to have an uphill battle and be fraught with potential setbacks. New technology must add performance and value apart from anything else. The user experience must be enhanced, not burdened with complicated feedback and/or maintenance requirements. And in our industry, above all else, must be dependable. If we merely adopt technology due to the current buzz of the industry without fully understanding its value, the end will not justify the means.
Automation & Smart Systems
What smart systems or components does your company currently offer? If they are application or industry specific, include that detail in the explanation.
RK: We make the HydrapulseTM smart hydraulic pump for both mobile and Industrial applications. The Hydrapulse was a ground-up rethinking of a fluid power pump that pairs a brushless permanent magnet motor, motor controller, software, and hydraulic pump together into a single compact unit. This allows for power-on-demand performance, plug-and-play simplicity, and inherent proportionality of hydraulic systems without the use of inefficient valves and manifolds. This leads to significant improvements in energy efficiency, which can be up to 80% savings in many applications.
The Hydrapulse also has onboard sensors to monitor fluid flow and pressure along with fluid temperature and numerous other metrics. We have also integrated an IMU to monitor vibration and other accelerations that can provide valuable feedback for our customers. Any of this data can be stored locally on the device’s memory or sent outside of the device for further analysis. Along with unprecedented fluid power control, this information provides invaluable information on the real-time status of the system.
How will that portfolio be expanding in the near future? What customer/industry demands drove these future developments?
MT: We are currently launching the Hydrapulse into the market for 2019. This is our main product line and exclusive focus of the company. Eventually the product line will encompass sizes from 1.5 kW (2 hp) up to 30 kW (40 hp) and is the result of almost a decade of research and development. There are many factors that have driven the development of the Hydrapulse. For some customers, easier troubleshooting and simpler maintenance are the driving factors. For others it’s the energy efficiency, reduced noise, or power-on-demand that is most important. But overall, the Hydrapulse is a ground-up rethinking of a fluid power system and how the industry as a whole can integrate the demands and trends of energy efficiency, hybridization, electrification, IoT, simplicity, labor/skills shortage, policy changes, Industry 4.0, AI and machine learning. By simplifying a fluid power system, OEMs can adopt advanced technology to address their market needs. We are taking cues from the automation industry for control, and the modern electronics industry for ease of use. Our goal is to make fluid power more accessible as an option inside and outside of our industry without needing decades of specialized knowledge to design a hydraulic system.
How do you see the timeline of vehicle automation unfolding in the coming years?
RK: Vehicle automation is already here. Most agricultural equipment is at least partially automated and more advanced than most people realize. Most types of off-highway equipment have automated specific functions of the machine. Fully autonomous functionality is still a decade or two, at minimum, away but OEM’s are already rapidly automating anything where the ROI can justify it.
Where do you see the greatest opportunity for automation, either on-board or in the manufacturing process?
MT: We see the greatest opportunity for automation at the function specific, on-vehicle level. For example, doing more of the historical off-board functions such as fruit sorting or packaging actually on the vehicle. The second area we see large growth potential is in the automation of the supply chain. Companies like Amazon have driven so much growth and technology in this front and we are just now beginning to see this trickle into our industry. Hopefully the era of 12-30+ week lead times will come to an end.
Managing the Data Trend
Since the onset of Big Data several years ago, how has data become an integrated part of your design and development process?
RK: Data has driven our development process and will continue to drive the evolution of our products in the future. We will use the data to make updates on the units in the field, as well as drive our decision-making process for future revisions.
What challenges remain or lay ahead for the continued and accelerated flow of data?
RK: More and more devices are coming with sensors and are able to collect all kinds of different data metrics. The next step will be distilling that information into something usable and valuable for each company. A lot of times the biggest value from collected data is not obvious right away. The biggest challenge our industry will face will be who owns the data and who is willing to share that data for the mutual benefit of the industry as a whole.
Challenges & Opportunities
What excites you about the future of the heavy-duty vehicle market?
RK: We are excited to be a part of the fluid power industry during a time of major change and upheaval. We feel there have been few times in history when there is this much change occurring in one industry that can provide huge opportunities for those willing to take risks and lead the way. Those that do not accept the inevitable shift will slowly phase themselves out of market share.
What ancillary sectors outside your core market or area of expertise are you keeping tabs on and why?
RK: We are keeping a close eye on battery development as well as other energy storage systems such as super capacitors. Energy storage is the largest hurdle in hybrid and electric drive operations for the heavy equipment industry. Its is yet to be seen if graphene, VA, or nano-tech are anything more than buzzwords in the OEM off-highway market.
Where are the challenges you are either currently dealing with, or foresee down the road?
RK: We are seeing major challenges in finding skilled personnel to fulfill our growth plans and develop out our team. We are also seeing extended lead times for raw materials, mechanical components, and electrical components. The global supply chain and its complexity are impacting all facets of manufacturing, which by the way, is helping push the need for automation in order to keep up. Automation is the long term solution to the current supply chain issues affecting all manufacturing.