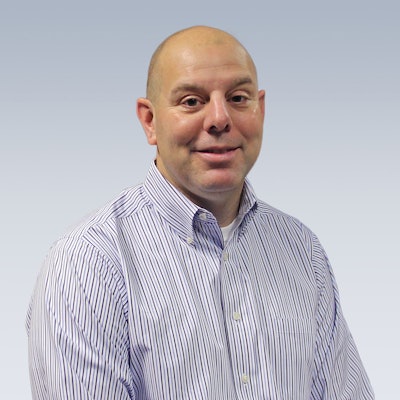
Global Markets, Government & Trade
What are the key global markets your company sees as growth opportunities and why?
Bosch Rexroth continues to see a strong fit to the mobile hydraulics industry with our focus on construction, agriculture and material handling equipment. While most mobile machines remain in our wheelhouse of applications we see the continued stronghold in those applications as the mobile market begins to spring back after the global pandemic.
How would passage of an infrastructure or other similar bill in the U.S.—or the equivalent in other countries—benefit the industry?
This would be a key determining factor in how quickly the overall mobile market begins to ramp up. Demand from the rental markets and end users of mobile machines for these infrastructure projects would drive OEMs to deliver new equipment potentially replacing an aging or less efficient machine. In turn, this drives suppliers to the OEMs and the suppliers of the suppliers as the economic engine turns again. The parallel effect is efficiency to market, using innovation and state of the art design for both the machine and the methodology of making the machine.
Diesel, Electric & Other Power Alternatives
How does your company see alternative fuels playing a role in the heavy equipment industry in the coming years?
Alternative fuels will continue to play an emerging role in the mobile/heavy equipment industry. However, the key challenge for any alternative energy source is the ability to convert to usable energy on the equipment in an effective and efficient way. Additionally, the equipment operation, duty cycle and the ability to replace the energy it uses for its operating location will determine the emergence and acceptance in the field.
What role is electrification—or other alternative energy/power systems—playing in your company’s design initiatives?
The end user demand or acceptance of electrification as well as the machine functionality, duty cycle and operation location, truly dictate the drive of the electrification topic and design for OEMs to the market. As a supplier and partner to these OEMs, Bosch and Bosch Rexroth are always investigating and working on innovation opportunities for components and systems that optimize the transfer of available energy and ultimately torque to perform functional movements on a machine. Whether this is via electric generator and motor combination for propelling a machine or an electric motor driving a hydraulic pump for flow to a valve for implement movement via a cylinder, the system design must utilize the right combination of components to optimize the efficient and effective transfer of available energy. Our design initiatives are shaped by this as more and more opportunities for electric and hybrid diesel/electric systems are demanded.
READ MORE: State of the Industry 2020
Data, IoT & Connectivity
How will the role of the Internet of Things (IoT) and data continue to progress in the coming years?
IoT has continued to progress beyond just fleet management or location data. In this digitalization era more and more data and information is available to process. However, the role of data must be purposeful and bring value to the beholder. Big Data is not necessarily the answer. Useful data that is being used to understand the status or location of a machine or available for calculation for preventive maintenance. That said, the continuing progression to the point of having every machine “connected” will be normal. One can see that with the adoption, progression and understanding of being connected and the data available could make “normal” mean that the warranty of a machine will depend on a machine being connected or your rental rate or operation from a rental company may be based on the data provided back to them on how you are running the machine. When the information and connection/telematics (informatics) is available and useful, it makes IoT the standard. It’s here and it’s now.
What challenges remain or lay ahead for the continued adoption of data, IoT and connectivity related technologies or systems?
The feature-cost benefit is the biggest challenge. As in most cases the end user of the machine, or likely a rental/fleet manager, will drive the adoption of connectivity and data. Useful, purposeful data that adds value to where a machine is located or how it is performing are simple enough to obtain, but there is more than this that could be available to evaluate. The challenge is therefore being able to react to the wants and needs of the person responsible for the machine. Of course, being able to troubleshoot any issues with the machine remotely is a nice feature to have in place such as diagnostics over the air (DOTA), but simple features such as an email or text alert when the machine is operating outside of a valid area of operation or when a filter needs changing or a fluid level is low are important items for the longevity and life of the machine. In some cases these are needed to maintain warranties on machines.
However, with the ability to be connected to the machine remotely, operational parameters on the machine can be changed (POTA – parameterization over the air), software upgrades can be pushed to the controller on the machine (FOTA – flash over the air), or even possibly the fleet manager wants to look at different data that is available on the machine (SOTA – over the air update to the connectivity unit). All of these are benefits and critical items related to the adoption of the machine being connected. But with that brings the additional challenge of safety and security. Listening to the needs is one part, but understanding that a machine could be hacked or when one should upgrade software on the machine when it is in a safe state or position, is a critical feature that must be considered. Working with the OEM to make available the right information, in the right time and for the right purpose is critical to the adoption. Again…useful, purposeful data that brings value.
Challenges & Opportunities
What are the biggest challenges facing the industry currently, or do you see the industry facing in the coming years?
Electrification remains a challenge for the industry. Rotational movements such as propelling a machine have moved much faster with the technique coming over from known, successful platforms in the automotive world. The challenge here still remains replacing the energy that you have used as duty cycles and operation location of a machine determine the longevity and use case. Meaning how quickly before I need to restore potential energy so I can keep working. On the implement side, the challenge is still to replace the power density of the hydraulics. Pumps driven by an electric motor, yes, but movement by a cylinder will still be needed. These are the technical factors but the geo-political environment as well as infrastructure bills both in construction and landscape of the agriculture industry with commodity markets, milk prices, land values, etc…may just be a bigger challenge then technology itself.
Are there any technologies or trends which you are currently excited about in the heavy-duty vehicle industry, or most looking forward to seeing in the coming years?
The digitalization and electrification trend driven by the end user of the machine will continue to shape the future. The benefit-cost ratio of moving towards electrification of the machine with the optimization of the most effective and efficient way to replace the energy you are using is the challenge. Will diesel engines still be the most effective and efficient way on the machine immediately or connection to an electric source and battery storage when not in use? It’s both exciting and challenging as the need for these machines doesn’t go away, but the innovation is what drives the technology leaders. It’s not achieving the end that is exciting, it’s the journey!