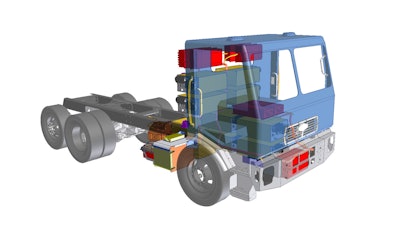
Eight years ago, Jim Castelaz, now CEO and founder, launched Motiv Power Systems with a mission – to free truck and bus fleets from their dependence on fossil fuels. A former fellow with the Department of Homeland Security, Castelaz noticed that trucks, buses, and heavy commercial vehicles were not only the workhorses of our economy, but also the most dependent on fossil fuels.
“While looking at that market segment and how the vehicles were built, I saw an opportunity for energy independence. There were a lot of specialty vehicle manufacturers with varying routes, but they all essentially used the same set of core components from a few major suppliers,” says Castelaz. The need was in the increasingly complex nature of the software necessary to control electrified vehicle systems.
“As vehicles go electric, the complexity of the vehicle is shifting away from the mechanical and toward the software, and that’s an area where we felt many vehicle manufacturers wouldn’t have internal expertise,” Castelaz says. As a result, Motiv was formed and a model was developed to create a scalable all-electric powertrain kit complete with software. OEMs can now easily drop in a Motiv all-electric powertrain into their existing vehicle platforms to offer an all-electric version of their vehicle models.
“Our expertise is around the software; our value proposition for a vehicle builder is that they don’t have to build custom software to have an electric vehicle option available to their customers. It is the same idea as computers or phones - each manufacturer does not need to develop its own software but instead can use Android or Windows, respectively,” Castelaz explains. For a prototype, any vehicle design team could create a basic software platform, but for commercial viability on a vehicle model, there is software infrastructure that needs to be developed to allow for software updates, support diagnostics, and create industry-acceptable safety parameters.
System hardware and software
“We have one technology platform – the electric powertrain platform and the operating system of the vehicle, plus our power electronics and controls,” says Castelaz.
At the heart of the powertrain’s scalability is a Motiv Adaptive Power Converter (APC), a voltage converter to move the power between the battery and the vehicle. This core component gives Motiv the ability to integrate any number of battery packs with different chemistries, voltages, and current charge and discharge specifications. The technology also allows Motiv to use commercially available battery packs.
“We have school buses fitted with four battery packs, and we have garbage trucks with upwards of 10 or 12 battery packs. Our scalable system allows us to scale the amount of energy storage on the vehicle as is appropriate for the weight of the vehicle as well as the route style. It is really the only solution available to avoid either customer battery pack design or custom vehicle design - both of which introduce cost, time and reliability and supply risk,” says Castelaz.
The other significant part of the powertrain kit that allows for scalability is the software. The powertrain software system networks all of the system components together into a central powertrain control unit which communicates with the instrument panel and ABS module in both the chassis software and the driver-facing software. “The batteries have their own controllers and battery management system, we have our own controllers and high voltage accessories that have control units, and we created the powertrain central control unit to allow them to talk to one another and other vehicle systems,” explains Castelaz.
“We also have administrative software to create a secure channel for firmware updates over wi-fi, diagnostic software, and configuration management to allow the end-user fleets to change any parameters like top speed depending on the vehicle profile.”
Motiv uses the same software on all vehicles versus the more conventional approach of designing customized software for each different vehicle application. “Our single software product is in very diverse routes already, from delivery trucks to school buses,” Castelaz says.
In the vocational vehicle space, where there is a high mix of vehicle types for a broad range of applications, each application may not have the critical mass to justify the cost of custom engineering. That’s why the Motiv common software operating system and flexible battery pack kitting makes for an affordable alternative for small-volume OEMs that want to offer an all-electric version of their vehicle models.
Applications and expansions
Due to the restrictions of current battery technologies, the Motiv system does not yet support long-haul applications. Instead Motiv looks to applications running up to 85 miles per day. This targets more urban and suburban vocational vehicles. However, the electric powertrain system is not limited to the on-highway market. “We have had many inquiries from the off-highway segment. Our core software is applicable for vehicles in construction, agriculture, and mining, for example,” Castelaz says.
One factor affecting the company’s active participation in off-highway applications is the lack of incentive funding for end-user fleets that want to pursue electric zero-emission vehicles. Conversely, for on-highway fleets there are substantial dollars to be awarded.
While Motiv currently has a robust portfolio of tested and proven battery, motor, and high voltage accessory options available to place into an electric powertrain kit, some may not be robust enough for the more rugged off-road industry. However, “we could find the correct subset of hardware that would work for off-road application routes and then be able to use our proven powertrain software to minimize the development timeline,” confirms Castelaz.
According to Motiv, approximately one third of the 8 million fossil fueled trucks and buses in the U.S. are ideal for electrification. These are the vehicles which drive on planned local routes such as school buses, garbage, and delivery trucks, and shuttle buses, with frequent starts and stops for regenerative braking energy reclamation, as well as an overnight storage depot with the infrastructure necessary for charging the vehicles.
As the popularity of vehicle electrification and emissions elimination continues to grow in the public eye and pull the electric vehicle progress forward, there is also continued regulatory pressure for emissions regulations, national security, and oil dependency pushing fleets toward alternative power sources. Motiv is already demonstrating its ability to offer low-volume, specialty application vehicle electrification using its common software platform and powertrain kit for those OEMs wanting to dip their toes in the water without taking on the development themselves.