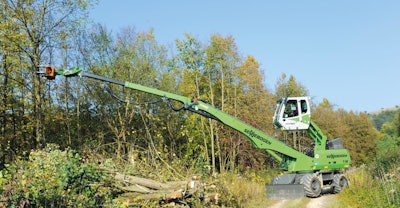
For two of Sennebogen and Albach’s newest pieces of machinery—the Sennebogen 718 and Albach Diamant 2000—offering increased mobility and improved operator safety were key elements of their design. “The whole project started when customers in the tree care industry came to us looking for a solution to cutting trees…they were looking for something of a certain size that would be easy to move around and take the operator away from [having to] climb the tree,” says Constantino Lannes, President of Sennebogen LLC, in regards to the development of the Sennebogen 718 material handler.
He says at the beginning, the company considered using one of its existing material handler designs, but was limited by the fact the machine would need to be able to move around the tree it was working on without having to continuously reposition the machine. This led to the development of the 718’s telescopic stick. Operators can park the material handler in the best position for the job and telescope the portion of the stick which grips and cuts the tree. Once cut, the stick’s telescopic capabilities can be used to safely bring the tree to the ground. “You’re not letting it fall and perhaps damage other vegetation,” says Lannes. The SENNEBOGEN 718's telescopic stick has a reach of up to 13 m (43 ft.), eliminating the need for a person to stand below the tree in order to cut it.Sennebogen LLC
A separate hydraulic pump is used to drive the attachment at the end of the stick so that it is fed independently from movement of the machine. This was another important aspect of the machine design as attachments such as processing heads and saws tend to require a lot of oil flow, says Lannes. It’s important to productivity on the work site to keep the attachment working continuously; having its own pump provides 100% assurance it is being fed the right amount of oil at the right pressure at all times during operation.
Making a more mobile machine
Compared to other tree services which go in and clear several trees at a time, for instance for a new housing development, the tree care industry cuts selectively and must have the ability to move around other trees and vegetation without causing any damage. Because of this, creating a machine which could easily maneuver around a work site, as well as from one location to another, was an important part of the 718’s development. “The whole idea was to make a very powerful machine so you could cut bigger trees, but at the same time [make it] compact,” says Lannes.
Making the machine more compact was key to achieving this. The company did so by changing the way it assembled to machine, placing the engine in the travel direction, parallel to the boom and stick. Lannes says this is opposite to most competitors who typically place the engine across the back of the machine in front of the counterweight. Doing so makes the machine narrower, and therefore better able to maneuver between trees.
He also notes that by having the engine mounted on the side of the machine, it’s easier to access for maintenance. The swing gears and other main components of the machine were also placed on the side for ease of access and servicing.
Use of wheels on the 718 aid its mobility, as well, enabling it to quickly travel from one work site to another without having to be transported on a truck. Wide in size, the tires work in tandem with the compact size of the machine to ensure it has a lower overall weight to reduce ground pressure, another important factor for the tree care industry.
Mobility was also key in the development of the Albach Diamant 2000 as Lannes says there was no chipper on wheels of this size which could move by itself that existed in the market. “The idea was to design a machine that is highway legal, has a high travel speed—45 mph—[so] you can move from work site to work site,” he says.
Watch a video of the Albach Diamant 2000 in action.
The Albach is able to automatically switch from transport to operating mode at the touch of a button. Once put into operating mode, the machine’s outriggers are lowered for stabilization, the loading crane is lifted, and the tree receiving table is lowered. The spout which discharges chips into a truck on the other side of the machine is lifted, as well. All of this is automated so there is no risk of it being forgotten by the operator, such as lowering the outriggers which would cause the machine to become unstable, and therefore unsafe.
Staying safe within the operator cab
By placing operators in the cab of the Sennebogen machines, they are removed from having to manually cut or chip any trees. When using a chipper, for instance, manually pushing a tree or branch into a machine that is rotating at a high speed increases the risk of the person using it getting hurt. Sitting in a cab instead ensures their safety, as well as comfort, on the job site.
It also enables operators to have better visibility over the work site and monitor the progress of the task at hand. Both the 718 and Albach feature hydraulically mounted cabs which elevate, and swivel seats so operators can easily adjust their sightlines.
The telescopic stick of the 718 helps with safety, as well, by providing extra reach—up to 13 m (43 ft.)—eliminating the need to have a person standing below the tree to cut it. One of the risks associated with cutting trees is that they have the potential to fall in an undesirable direction—causing potential harm to people, other plants, etc. But with the operator several feet away in the machine cab, gripping the tree with the telescopic stick, he or she is kept safe should the tree being cut fall in the wrong direction.
Comfort is also an aspect of operator safety, which is why both machine cabs include heating and air conditioning, as well as an air suspended seat. In addition, hydraulic joysticks are employed for ease of machine control. The Albach Diamant 2000 chipper automatically converts from transport to chipping mode at the push of a button.Sennebogen LLC
Within the Albach cab, operators can monitor work progress via software developed by Albach. Lannes says the advantage of developing it in-house is that the software can be specific for the kind of operation for which the machine is designed. It provides 100% monitoring of the chipping operation, 100% monitoring of the crane feeding the chipper. Performance data of the chipper is also provided including how many tons per hour of chips are being produced, the quality of the chips, and safety of the operation at hand, specifically whether all sensors are working correctly and the machine is not being overloaded. “[It ensures] you’re doing everything according to the design characteristics and your machine will live a long time,” says Lannes. All information is displayed on a touchscreen within the cab.
In addition to improved safety, removing the manual aspect of tree cutting and chipping with the two new machines can help lower the number of people needed on a job site, reducing operating costs. “But most important is you take [people] out of the danger area around the machine,” concludes Lannes.