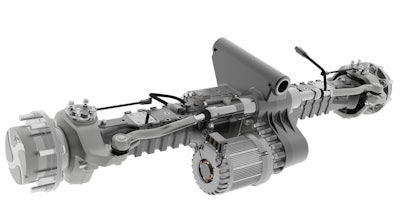
As electrification grows in many heavy-duty vehicle segments, it is also creating uncertainty regarding the future of componentry such as those used in drivetrain systems. How will it affect axle designs in the future? Will the gearing industry be impacted at some point?
John Bennett, VP and CTO at Meritor Inc., spoke on the topic during the Motion + Power Technology Expo (MPT Expo) in October. He said electrification will likely bring changes to several parts within drivetrain systems including gearing.
“Electric vehicles are very disruptive to just about everybody in the commercial vehicle value stream,” he said.
Every aspect of a vehicle will evolve, from the largest to the smallest components. Freudenberg Sealing Technologies is one of the many manufacturers to have noted this. It says seals will still be necessary in some regards, but there will be fewer and the types utilized will change.
Because of this, the company has begun to diversify its product offerings by investing in the development of batteries and fuel cells, as well as seals for use in electric power systems. Read more in the article “Freudenberg Focuses on Fuel Cell Development.”
Changes to the drivetrain
The most obvious impact of electric vehicles will be seen by those making engines and traditional transmissions. “Your business is going to change dramatically in the future,” said Bennett.
This is already evident by the fact many engine manufacturers have begun to diversify their business, investing in alternatives including batteries and hydrogen fuel cells.
Bennett said less obvious impacts will come to light when optimizing electric vehicle designs. Changes can be made to the front axle and front suspension, for instance, altering their construction from what is typically seen today which could affect aspects such as the amount of gearing necessary.
If integrating an electric motor into an axle the design of the axle changes. There are various ways a motor can be integrated into an axle, and each has advantages and disadvantages that need to be weighed against the target application. The final architecture will ultimately impact the types of gears used, the number of gears and bearings used, and whether a transmission needs to be integrated as well. A well-integrated eAxle may look similar to a conventional axle on the outside but will be very different on the inside.
The brakes change as well and the driveline goes away, explained Bennett. “Every part of the drivetrain and powertrain is impacted.”
He noted there are four important differences between a diesel engine and electric motor which impact the number of gears a battery-electric vehicle (BEV) will have. Advantages electric motors offer over a diesel engine include:
- higher low-speed torque
- faster top speed, up to six times
- wider speed range
- wide efficiency zone.
What this means, said Bennett, is not all electric motors need a transmission whereas a diesel engine does. Therefore, you can replace both the engine and transmission with a single electric motor—which is how most BEVs are currently designed.
Direct drive BEVs eliminate the transmission, and thus any gearing that it would include, and just use an electric motor. Bennett said this is the primary configuration used in China and the simplest method of employing electrification.
Meritor Defense's 3400 eISAS electric independent suspension features a helical gearbox design which offers efficient and quiet operation.Meritor Inc.
Some BEVs, however, do use a transmission; these types of vehicles are starting to gain in popularity especially in North America and Europe where customers value performance, said Bennett. He said there are a few advantages to including a transmission such as being able to downsize the motor.
A smaller motor reduces cost and weight and provides better performance. “Like a diesel engine you get better low-speed torque and better grade climbing,” he explained.
Alexander Eisner, Head of Product Communication, Off-Highway Systems at ZF Friedrichshafen AG, confirms that transmissions for electric vehicles will have fewer gears. For instance, three speed transmissions will be utilized for electric powered systems while four speed transmissions are commonly used in diesel powered equipment. The challenge, he says, will be handling the higher input speeds of electric motors versus those used in diesel powered machines.
Electric motors are being designed to reach much higher rpms than hydraulic motors or internal combustion engines as a means of achieving better power density, explains Rob Kress, Head of Off-Highway Electrification Sales and Strategy at Dana Inc. Because of this, other drivetrain components such as the transmission will need to be modified to handle the faster speeds.
Packaging is one aspect that will be impacted. Kress says drivetrains for electrified off-highway equipment need to provide better packaging since electric motors are typically larger than hydraulic motors. Batteries also take up a lot of space, bringing about further packaging adjustments.
“The ability to use multiple motors for propulsion instead of a single internal combustion engine opens up many opportunities to redesign the drivetrain and optimize vehicle packaging,” adds Kress. “All of these factors create exciting opportunities for drivetrain suppliers. In fact, we are a seeing a larger variety of options and architectures for optimizing each different application.” Dana used a clean sheet design for its Spicer Electrified e-Gearbox to ensure compatibility with faster motors.
He says Dana’s high-efficiency Spicer Electrified e-Gearbox and e-Axle exemplify the new designs required to provide traction for electrified off-highway equipment. The e-Gearbox features a clean-sheet design to ensure compatibility with faster motors and minimize power losses as well as preserve battery energy.
Dana’s e-Axle technology, on the other hand, replaces a traditional off-highway driveline with a configuration that features two independent axles powered by parallel-mounted electric motors for improved efficiency and packaging.
New factors to consider
Jeff Hemphill, CTO at Schaeffler Group USA Inc., said during his presentation at MPT Expo that range is a critical aspect for electric vehicles. Extending range to eliminate anxiety for drivers is a key focus for many vehicle manufacturers at the moment. As such, suppliers providing components for these vehicles need to make reductions in friction loss and drag. “This is even more important in an electric vehicle than it is in a combustion engine powered vehicle,” he said.
A little under 10% of the total energy losses from a combustion engine are due to friction losses in the powertrain. For a BEV almost one third of the total energy losses are friction losses. He said this demonstrates there is a lot of work yet to be done by component manufacturers to reduce drag and help OEMs increase electric vehicle range.
With electric vehicles there are new failure moments, as well, of which hardware manufacturers need to be aware. A typical ball bearing on the shaft of an electric motor, for instance, was found to have its outer raceway process in the outer housing due to the lighter loads and speeds being placed on it.
Hemphill said there are a few things that can be done about this. The outer race of the bearing can be made thicker to eliminate the possibility of race processing, or a key can be placed in the bearing raceway to mechanically stop it. He said it is also possible to just let it slide and ensure no damage is done.
There are a variety of coatings that can be applied to the outer race of the bearing to ensure there is no deterioration to the aluminum housing it is in, as well. “We can get some extremely low coefficients of friction with some of those coatings which helps with the issue of drag reduction,” he said.
An aspect Hemphill pointed out manufacturers will need to be cognizant of is that bearings will be exposed to electric currents in ways they never have before if installed in electric vehicles. “That can create some issues with the lubrication layer between the rolling element and the race,” he explained.
Electrical discharges can occur in the bearing, causing damage to it and the system in which it is integrated. Hemphill said Schaeffler has some surface technologies that can help mitigate that such as ceramic coatings that can be put on the outside of the bearing to provide a high level of resistance. Read the article “Evolving Vehicle Designs Bring New Lubrication Requirements” to learn more about the effect electrification may have on powertrain lubricants.
Hybrid ceramic bearings are also an option to prevent current from passing through the bearing. These are advantageous for high-speed systems because the rolling elements are lighter and therefore better able to perform at high speeds.
Electrification provides opportunities for new packaging and layout of drivetrain systems.Dana Inc.
Future design possibilities
Bennett said Meritor believes the motor will ultimately migrate into the axle. Integrating the motor into the axle opens up packaging space between the frame rails which can help make room for the batteries or other components.
Being able to put the batteries between the frame rails improves safety of the vehicle by keeping them protected in the center of the vehicle should there be some sort of impact to the vehicle. It also helps reduce weight as the batteries do not need to be cantilevered as they would if placed outside the frame rails.
Integrating the motor into the axle also opens up the possibility to reconfigure and optimize the vehicle design. Basically, it gives the vehicle manufacturer the freedom to do whatever it wants, said Bennett. This can lead to completely new vehicle designs in which their appearance is completely different from what is seen today.
With these new designs can also come new packaging and placement of components. In a commercial truck, for instance, the electric motor may be mounted perpendicular to the axle shaft or parallel to it. Either way, Bennett said gearing will still be necessary for these configurations.
Meritor's 17Xe is an electric axle designed for powering heavy-duty trucks up to 44 tons with a single drive axle.Meritor Inc.
Integrating a transmission into the powertrain system may occur in the future, as well. Again, Bennett said gearing will still be a necessary component, though the number and type of gears could change from what is traditionally used today.
For vehicle configurations in which more than one motor is used, such as those where a motor is located at each wheel to individually power the wheels, there may actually be a need for more gearing than usual. Bennett said that while in this configuration the main differential has been eliminated, the amount of gearing necessary is actually doubled
He also noted that there are some direct-drive in-wheel motor technologies available with enough power to drive a vehicle, if used on multiple wheels. This he believes is the most disruptive to drivetrain manufacturers and those who supply components to them because no gears are required in these architectures. Currently this technology is very expensive and thus not widely adopted, but should the costs come down he said it could make a real impact on the industry.
Hemphill said new electric and autonomous vehicle concepts may actually provide opportunities for gear and bearing manufacturers, instead of causing their business to diminish. For concepts such as electric and autonomous people movers or shuttles there will still need to be a gear train to get the power of the motor to the road as well as new actuation possibilities. Smaller gears and bearings may be utilized, but more of them will be required.
“[Change] is going to happen in an unpredictable way, but a big way, and there’s plenty of opportunity for hardware manufacturers,” said Hemphill.
The bottom line is electric vehicles are coming and components will be impacted. “I believe absolutely electric vehicles will impact the gear industry. The number of gears will go down as a result [of vehicle electrification] and the integration of electric motors,” said Bennett.
With the types of electric motors currently being used he doesn’t think the types of gears used will be affected. Noise, however, will become a more important factor for gear designs. As electric vehicles are typically quieter due to the elimination of an engine, there will be an increased possibility of hearing noise from components such as gears that would otherwise be covered up by the sound of the engine.
Kress says that in the short term, gearboxes and elements closest to motors will see the greatest changes as engineers work to improve efficiency, accommodate higher rpms and improve NVH (noise, vibration and harshness). “When electric vehicles become more of the norm in specific off-highway applications over the long term, driveline architectures may change radically, resulting in a more significant impact on all driveline components,” he says.
Bennett concluded by saying manufacturers should not get caught off guard by the increasing transition to electrification. They should look at how their business may be impacted and start planning now for when electric vehicles become more prevalent in the market.
The Schaeffler Mover uses a variety of gears and bearings, demonstrating that new vehicle concepts will provide opportunities for hardware component manufacturers.Schaeffler