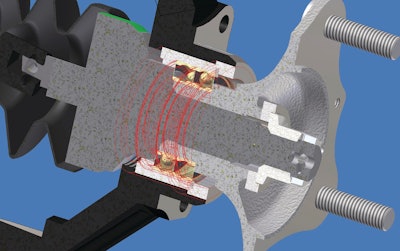
In Alaska, all-terrain vehicles (ATV) have the potential to be operated much more on a daily basis than they might in the Midwestern states. In many remote villages ATVs are the primary mode of land transportation during the summer. In Alaska they're also used for subsistence — the harvesting of fish, animals or other wild, renewable resources for use by residents of the state's vast rural areas. And with 700 miles of ATV routes just within the state's national parks, they're also used for recreation.
Steve Phillips lives in a rural Alaskan village, and the area where he rides his ATV for both recreation and subsistence is comprised of mountains and sea shore — a nice mix of difficult terrain that can wreak havoc with the moving parts of his ATV, particularly the wheel bearings. Every four to six months he found he was changing wheel bearings, which was not only time-consuming but also revealed one of the downfalls to rural life — it can be difficult to acquire replacement parts.
Phillips began searching for a solution to the wheel bearing problem. He carried parts of the ATV into his house, and eventually basic drawings were made. Phillips hired an engineer in Fairbanks, AK, to develop the prototype and ensure that the design worked the way Phillips believed it would.
The prototypes did work, and the result is the recently patented Speed Bearing, which reportedly reduces the time associated with traditional wheel bearing assembly replacement by 75%.
The system consists of a stainless steel insert that holds a standard steel bearing, which in turn fits in a modified knuckle made of forged steel.
The design has the potential of reducing down time in other industries, as it can be scaled up from an ATV application to one that could be used on landscaping, construction or agricultural equipment. "It's a practical concept," says Shane Chapple, vice president, Phillips Enterprises, LLC, Anchorage, AK, "and the design can be transferred to other applications fairly easily."
Speed Bearing can reduce time in the shop. "In Alaska there's a lot of oil development. If a machine on the Slope breaks down, that's time down, and production goes down."
Replacing a Speed Bearing does not require the removal of brake drums or housings. The axle nut and wheel is removed for access to the bearings. The insert that encapsulates the ball bearings screws into the threaded knuckle. Phillips Enterprises has developed a socket tool that fits on a standard ratchet to facilitate the removal of the modified bearing. The tool is used to spin the bearing out.
Testing the design in the Alaskan bush, Phillips discovered the new wheel bearings were lasting longer, too. "The amount of time the bearings lasted in the ATVs went from four to six months to 10 to 12 months," says Chapple, "doubling the life of the bearing."
While Chapple concedes that not every ATV sees the harsh conditions Alaska can dish out — "it isn't like people everywhere else hop on their ATVs and drive 40 or 50 miles a day" — the young company's natural test track does mirror the working environments of other off-highway industries.
"If you go 'up the country' to look for moose or go fishing," says Chapple, "it's not uncommon to drive your ATV 20 miles in and 20 miles back out."
Because the design of the insert insulates the bearing, it takes some of the pounding, and debris intrusion is reduced.
Phillips Enterprises is a small company and is hoping to partner with other manufacturers to license its technology. "It is a new idea, and sometimes new ideas are met with a little skepticism," says Chapple, "but we hope that the manufacturers will take a look at it and decide that it is a product that will work in many different applications."