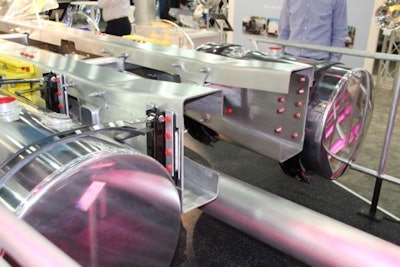
In ground transportation, the motivation to reduce weight differs by the industry. For the on-highway trucking industry, there is a weight restriction for each class, so often the lightweighting effort is focused on maximizing payload. In Class 8 trucks, only 10-12% of the vehicles will reach the allowable 80,000-lb. limit on interstates. These are the vehicles that are motivated to reduce weight and are early adopters of new technologies to accomplish it. The most stringent are the bulk haulers who often reach the maximum weight before the tank is full. Second are fleets carrying refrigerated freight, and freight such as glass, metals and lumber.
Exterior cabs are typically made of aluminum, steel, plastic or sheet mold composite. About 60% of the cabs use aluminum. Years ago, aluminum was the preferred choice because of corrosion resistance, yet over time, the steel protection systems improved dramatically. Now, aluminum bodies are motivated by weight reduction.
On a vocational truck like a concrete mixer, the aluminum body conversion from steel sheds about 200 lbs. (90.7 kg) However, one product manager said drivers often do not select aluminum because of the perceived lack of durability. This same product manager said that aluminum oil pans shatter, so they had to be steel; and he wasn’t sure that differential housings could hold up on concrete trucks.
Strong, cast aluminum like A206 is called “unbreakable” by engineers in the military, as it’s used on the most brutal driveline application—the final drive housings on combat vehicles. It’s also used on differential cases and carriers on tactical vehicles, Baja and rally car race vehicles, and a host of mining housings. There is a high chance that the oil pan was made with aluminum that wasn’t appropriate for the application, and that the right choice of material and manufacturing process would have delivered on both weight reduction and durability.
Polymer-based materials are common for the aerodynamic fairings over the front bumper, fuel tanks and roof. Polymer composites are common for aerodynamic skirts under the trailers, and for covering the wheels. Using injection-molded plastics or reinforced plastics are a great choice for these non-structural applications as they are considerably lighter and lower cost than aluminum.
Lightweighting wheel-end components reduces tare weight and minimizes rolling resistance. Converting wheels from steel to aluminum in the 22 in. size saves about 77 lbs. (35 kg) on the steer axle, and 115 lbs. (52 kg) on each tandem, for a total of 307 lbs. (139 kg) per tractor.
Inside the wheel is the hub, which is made of ductile iron, austempered ductile iron (ADI) or perhaps most common is A356 aluminum made in a permanent mold casting process. A major axle producer said that aluminum hubs are standard product on OEM tractors today and offer a weight savings of about 150 lbs. (68 kg) from iron hubs. They also said that the price premium over iron is $2 per pound, which is low for an aluminum product. Most aluminum products on heavy trucks are priced at a premium of $6 per pound over the baseline ferrous product. The forged aluminum fifth wheel (100 lbs. [45 kg] of weight savings) and the best aluminum wheels sell at a premium of $10 per pound. If there are larger wheels or higher axle and fatigue loads, there are much stronger aluminum alloys than A356 for the hub application.
The frame rails of an over-the-road truck are steel and are often listed by the tensile strength. A General Motors pickup has a 95,000 psi (95 kip per sq. in., ksi) steel frame, whereas on a heavy truck, a tensile strength of 120,000 psi (120 ksi) is common today. Two lightweighting alternative material options are in development; 140,000 psi (140 ksi) steel that could shed 200-300 lbs. is one of them; aluminum is another. The Freightliner Cascadia lists an aluminum frame rail option today.
Alcoa and Metalsa demonstrated an aluminum-intensive frame assembly at the 2015 Mid-America Trucking Show (event information, 10207301) that incorporates rails along with suspension mounts and cross members. They report a savings potential of 1,000 lbs. (453.6 kg) over a traditional steel frame assembly. The aluminum frame is not a new idea, though improvements in processing such as roll-forming and the ability to selectively increase the section size have improved the ability to perform in heavy trucks. Aluminum cross members are very common; one of the Dept. of Energy (DOE) SuperTrucks used magnesium cross-members. In the driveline, the baseline driveshaft is steel, yet an aluminum driveshaft would save 100 lbs. (45 kg).
In the compressed natural gas (CNG) market, carbon fiber has taken over the gas storage market. Because CNG isn’t an efficient fuel from a volumetric perspective, the storage vessels are large, and the lightest option is winning.
There are many barriers to weight reduction in a heavy truck fleet. Automatic manual transmissions (AMTs) deliver up to 5% better fuel economy. Since they are easier to drive, it’s easier to attract and retain drivers; and it’s easier to integrate safety technologies to the transmission, such as stability control or platooning. However, AMTs are as much as 500 lbs. (226.8 kg) heavier than a manual transmission.
The diesel emission regulations have added hundreds of pounds of equipment to the primary engine, and up to 260 lbs. to the trailer refrigeration units. To save fuel, an auxiliary power unit (APU) is used to heat and cool the cabin in lieu of running the main engine, and in some states, APUs are mandatory. Unfortunately they weigh 400-500 lbs.
However, amidst the difficulties, lightweighting and material selection continues to be top of mind for many equipment manufacturers in order to meet increasing fuel economy expectations while maintaining productivity and payload capabilities. |
Details in this article came from the “Confidence Report on Light-Weighting of Heavy Trucks & Trailers” by the North American Council on Freight Efficiency (www.nacfe.org). Andrew Halonen led that study and it can be downloaded for free at the following link, http://www.truckingefficiency.org/tractor-aerodynamics/weight-reduction-tractors. The Trucking Efficiency website explores many technologies available for heavy trucks with the intent of providing a balanced review for fleet owners to make evaluation and selection decisions.