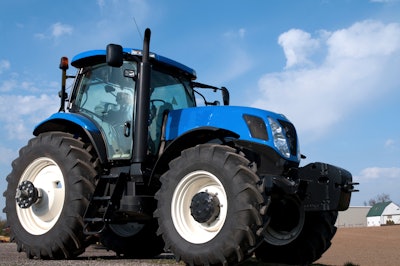
It can be difficult to ascertain the root cause when a design aspect is not performing correctly in an application. Even with a single component in a product, a multitude of factors can affect its performance, so it often takes a methodical approach and an expert eye to identify the true underlying cause. When the problem only arises after delivery of the finished product warranty claims can place added financial pressures on a business; understandably, this places extra demands on engineers to address the overall design problem quickly.
This was exactly the situation faced by a manufacturer of compact tractors, who had begun to receive warranty claims due to a failing joint. The associated component in question was a zinc electroplated thread forming deck screw, which attached to the tractor’s chassis, and had passed all mechanical and dimensional inspections. This screw was mated with a large diameter washer and a powdered metal spacer, which was incorporated into the joint grip to prevent over-compression. The joint was failing shortly after delivery, resulting in warranty claims, so the engineering teams began disassembling a compact tractor deck to try and identify the root cause, and a possible solution.
Working with its external service provider and distributor of fasteners, Optimas Solutions, the manufacturer began assessing the assembly. It was quickly discovered that the spacer was misaligned, which presented the opportunity for it to shear off a section of the plastic decking. To further compound the problem, the design of the extruded cylinder (which seated the washer), did not distribute load evenly, placing more stress on the deck and screw, and encouraging joint failure.
Tim Day, Applications Engineer at Optimas, explains the next steps: “We had to try and identify the root cause of the failures. The fracture surfaces on the failed screws seemed to suggest hydrogen embrittlement failure, but none of the production lots or any testing carried out on them offered any correlation that process induced embrittlement was the cause. Subsequently, we worked out that the screws were most likely being placed under a bending load during installation, which was due to the uneven seating of the washer and spacer. Eventually we were able to conclude that we were faced with a stress corrosion issue due to the faulty design of the joint.”
Together, the engineering teams proposed the solution. The screw was redesigned to include an integrated shoulder, which removed the powdered metal spacer, simplifying the assembly. Next, the coating of the screw itself was changed from zinc electroplating to a cathodic E-coat process, which all but eliminated embrittlement risk and improved stress corrosion characteristics. The heat treatment applied to the screw was also changed from case hardening to through hardening, with an induction hardened point for thread forming. This served to further reduce the possibility of case cracking or stress corrosion. Finally, the load bearing surface was redesigned to remove the need for the washer and promote even loading in application, solving the underlying cause.
The manufacturer implemented the solution in its compact tractor designs from then onward, which immediately stemmed the flow of delayed joint failure and associated warranty claims. As a result, the business was under reduced financial pressure, increasing the return on its operations. Furthermore, the new screw with integrated shoulder meant that two separate part numbers could be removed from the compact tractor’s Bill of Materials (BoM) and increased production efficiency. This helped to consolidate supply requirements for this compact tractor model, simplifying the supply chain.
Small design defects can create big challenges, as the issue may not be discovered until the product reaches the dealership or customer. In an application where durability is paramount, such as a compact tractor, the problems are simply exacerbated. However, by solving the issue with appropriate component solutions at the earliest possible opportunity, failure can be addressed with added benefits beyond ensuring product quality. In this case, the solution avoided additional, potentially damaging warranty claims, ensuring that the manufacturer’s overall reputation was never at risk.