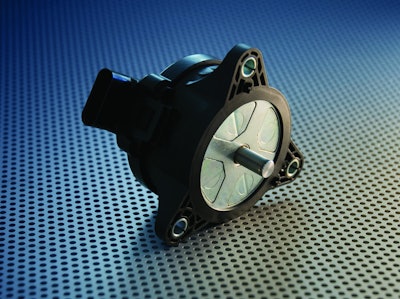
Growing environmental awareness is promoting a rise in environmentally-friendly technologies. New regulation standards, such as Tier 4 final or Euro VI set to come into effect in 2014, are stipulating ever higher requirements with regard to reducing the emissions and fuel consumption of agricultural machinery, construction vehicles and trucks. Optimization of induction and exhaust flow has become key to reducing emissions and improving overall engine performance, while downsizing the engine to increase fuel economy.
One of the key technologies for reducing NOx emissions for large diesel engines is exhaust gas recirculation (EGR), which requires the optimal use of valves, whatever they are installed in the high-pressure or a low-pressure loop. The increasingly exigent emission thresholds mean that gas flows must be precisely managed. This implies the requirement of reliable actuation and sensing solutions. The need for robust, precise, and fast electric actuators is thus continually increasing.
This on-going trend for electric drives means as well optimizing key components without compromising on performance, design and comfort. Sonceboz, the Swiss firm based in the town of the same name in Jura, offers an optimal solution with its electromagnetic drive known as the "torque motor". It is widely used for valve or flap positioning functions. “More than 20 million torque motors have already been produced by Sonceboz with an outstanding field quality record below 0.5 ppm for powertrain applications such as EGR valves, throttle positioners, and variable-geometry turbochargers.” said Dr. Marc-Olivier André, Business Unit Manager.
Compact with high functional density
The torque motor is a rotary DC brushless actuator. Thanks to a unique mechanical and magnetic structure, it offers very high torque in a very compact design, as well as an elevated boost or breakaway torque capability. Yet the detent torque is negligible, minimizing the impact of the return spring and permitting low holding currents. Being a direct-drive actuator with no transmission gears, torque motors yield the advantage of fast response (full-troke positioning below 100 ms) and guarantees unparalleled robustness in harsh environments and reliability over a long service life.
This single-phase motor is compatible with the standard H-bridge drives typically available in engine control units, which means substantial cost savings and higher temperature resistance compared to actuators featured with integrated electronics. The functional density of the torque motor is further increased by the optimized integration of the sensor system. Indeed a highly integrated non-contact position sensor permits positional control with simple, standard PID regulation protocols. It is the integrated position sensor, based on a contactless magnetic principle with Hall ASIC (application-specific integrated circuit), that makes the extremely compact design of the motor possible in the first place. A molded casing encapsulates the coils and contact terminals, helps dissipate heat, protects against the harsh service environment and serves the function of bearing for the rotor shaft as well. Sonceboz' fully automated production lines guarantee consistently high quality and cost efficiency.
The torque motor works without a brush using a permanent magnet on the rotor and is therefore smooth and non-wearing. The rotor in the Sonceboz drive moves across an angle range of 75 degrees. The interaction between the magnet on the rotor and the electromagnet on the stator generates a torque, whose direction depends on the current polarity supplied to the electromagnets. This means that any position can be controlled proportionally by adjusting the current. The rotor stops in the position at which the drive torque and the total resistance torques of the application are at equilibrium.
Adaptation to any valve size
The existing product range includes a large torque range to fit any valve sizes. In the example of Sonceboz' 4256 Series torque motor, it features a peak torque of up to 1.4 Nm at 13.5V, with a compact size of 80 mm diameter and 40 mm high, with a light weight of just 640g.“Higher performances in the product range are currently under development in order to match larger EGR valves specifications. Latest designs include torque values up to 4.7 Nm for 12V systems—higher in 24V systems—thus making the torque motor suitable for valve or flap specifications for heavy-duty engines. “We are working closely with our customers to meet their requirements and provide them the optimal solution in terms of performance and total cost of ownership,” says André.
Customer-specific solutions are developed by a dedicated and flexible engineering team, working quickly and efficiently to optimize the standard torque motor to the required mechanical performance and interface specifications. The 75 degree rotary output angle of the torque motor can be translated into a reduced or extended rotary range, or into a linear motion by means of simple and robust mechanical kinematics.
A return spring ensures safety in the event of a power failure for most engine management applications. This always guarantees a reliable failsafe position, as a random position in a power cut could cause substantial damage. As the torque motor is a direct drive, i.e. it works without transmission gearing, the residual torque—friction or detent—is extremely low. This means that the return spring can be optimally sized to enable a perfectly compact design and installation in the whole EGR valve system.
Extreme robustness
These brushless actuators have been validated against the highest standards prevailing in construction machinery, confirming an intrinsic robustness not achieved by other actuator technologies. Their ability to operate in very harsh engine environmental conditions are in-house tested at the Swiss headquarters. For instance, the 4256 series was tested during validation in the harshest environmental conditions for off-highway machines to determine what types of adversity it could withstand. With regard to temperature and vibration resistance the drive performed superbly and was rated best in its class. For example, it sailed through the vibration tests with loads of up to 40 G in ambient temperatures of -40 to 150 C. It performed ten million cycles of durability testing, as well.
“What makes then torque motors so impressive at work in EGR valve is the high torque they generate for their size. They are also very precise, fast and exceptionally robust, guaranteeing a long service life” says André. All these attributes make them ideal for EGR valves actuation in off-highway vehicles and mobile machines, where resistance to high temperatures and strong vibrations prevail.
Sonceboz has been developing and producing electromagnetic drives for the automotive industry for years: passenger cars, medium and heavy trucks, agricultural and construction machines. By orchestrating mechanical, electronic and software technologies into powerful mechatronic drive systems, Sonceboz provides dependable solutions for engine control of petrol and diesel engines. Therefore this multi-field expertise is as well proven in mobile hydraulic, instrumentation and industrial applications. Sonceboz is assisted by its fully-owned subsidiary, Moving Magnet Technology (MMT) whose approx. Thirty five engineers, many of whom hold doctorates, work exclusively on the advanced research and patenting of pioneering electromagnetic technologies for sensors, motors and actuators.