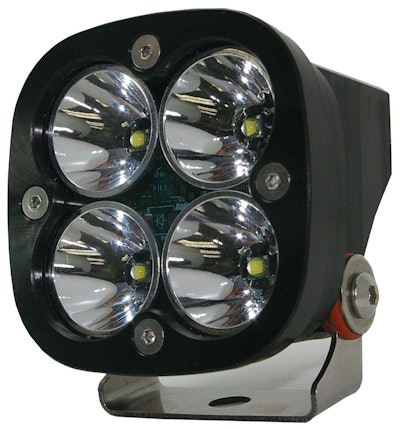
Lifespan of a product is important, especially in this day and age when people are trying to save money any way they can. Continuously replacing lights can become a costly for vehicle owners. As lighting design progresses, manufacturers are producing longer lasting lights to help alleviate those added costs for customers.
At first high-intensity discharge (HID) lamps were the bright new technology, replacing halogens because an HID could provide 2,000 hours of light versus the 200 hours of a halogen bulb. And now, light-emitting diodes (LEDs)—which have a typical lifespan of 20,000-40,000 hours—are replacing HIDs.
LEDs also offer better efficiency because of low energy consumption. According to Brad VanRiper, Senior VP of Research and Development and Chief Technology Officer at Truck-Lite Co. LLC, Falconer, NY, an LED has a lower current draw than other lighting technologies yet offers the same amount of light, if not more, as well as a longer lifespan.
VanRiper says that when white LED technology was developed and organizations like the U.S. Dept. of Energy saw its electricity-saving capabilities, more research money became available for product development. Most of that research money went towards increasing the number of lumens per watt. “If you were to look at a graph of white LED output lumens, it has been up and to the right almost at an exponential rate,” says VanRiper.
Deanne Moore, CEO of Baja Designs Inc., San Marcos, CA, says in lighting design “the holy grail is achieving massive lumens per watt.” The more lumens per watt a light has, the better its efficiency. Moore notes that lights can take up a lot of power, especially in an electric vehicle which has only so much power available for accessories. A halogen can use 100 watts per light while an LED will only use about 35 to 43 watts, says Moore.
A shift towards LEDs
Longer lifetime and higher efficiency are just two of the key advantages which have helped push LEDs to be the most used lighting technology. Dragan Popovic, Director of Research and Development at J.W. Speaker Corp., Germantown, WI, says “in the next five to seven years, I believe every single device will be LEDs.”
The difference in lifespans is one of the biggest features that sets an LED light apart from an HID, halogen or other light source. When compared to an HID, it’s a difference of 3,000 versus 40,000 hours, says Popovic. VanRiper says when compared to incandescent lighting, and designed properly, an LED can offer 10 times the lifespan. He continues that while LEDs will have a 10% reduction in output over time, they aren’t susceptible to failure like incandescent lighting.
With the LEDs’ longer lifespan, users won’t have to worry about changing bulbs over and over again, helping save on costs. J.W. Speaker’s Ryan Mayrand, Product Marketing, notes that changing lights on a piece of heavy-duty off-road equipment can be more frequent because things such as vibrations and rocks can cause an untimely demise to a lamp. “[With LED,] there are no breakable bulbs, fragile filaments or sensitive electrodes.”
Along with a long-lasting product, designers want to create a light that will actually enable their customers to see. With HID technology, a ballast strikes an arc at a high voltage, sometimes as high as 2,000 volts according to VanRiper, which produces a very bright light. However, the color temperature produced is in the 3,500 to 4,000 Kelvin (5,840 to 6,740 F) range, whereas LEDs operate in the 5,500 to 6,000 Kelvin (9,440 to 10,340 F) range for a more daylight-like appearance. Moore says this color temperature range is the one in which a person sees best. In comparison to LEDs, the HIDs emit a light that is much more yellow in appearance.
Durability is another advantage LEDs have over other lighting technologies. HIDs, for example, have bulky housings and bulbs which are very sensitive to vibrations and impact. Because the tip of an HID bulb is especially sensitive, it can only be positioned one way. “As soon as you start to tip it more than 10 degrees it causes catastrophic failure because mercury or salt gets between the electrode and the glass,” says Popovic.
LED lights on the other hand use solid-state technology, requiring no bulbs or filaments, which Mayrand says enables them to be better suited for heavy-duty applications. Instead, small diodes are used as the light source, enabling a properly designed LED light to be resistant to vibration and shock. VanRiper notes that when Truck-Lite began working with LED technology 20 years ago, “we immediately recognized this technology was far more robust than the incandescent technology it was competing with.”
One aspect that hindered LEDs was its cost. Originally they were more expensive than competing technologies. However, VanRiper says the cost of LEDs has decreased from a 10 to 1 ratio to a 4 to 1 ratio when compared to incandescent lights.
Evolution of the LED
When LED lights first started to come into the market 20 years ago, “red LEDs were the first to emerge as bright enough for us to use in signaling and marking devices,” says VanRiper. Since then, the color spectrum has evolved to include amber and white LEDs, as well.
One of the improvements made to LEDs over the years was a decrease in the number of LEDs necessary to provide the light output users wanted. In 1993, Truck-Lite came out with a stop light that contained 61 LEDs. By 2005 the company had a single LED red stop tail and turn lamp. “We’re using fewer and fewer LEDs,” says VanRiper, “and I think we’re hitting a point where the technology is matured enough that you get the best balance of reliability, light output and lower cost.”
With the continued improvements, LEDs became available for more on- and off-road applications. VanRiper notes that Truck-Lite first used white LEDs for license plate lights because they required the least amount of power; but as their low power consumption became more evident, the LEDs were used in backup lights, work lights and headlights.
Consistency of color and output has been improving as well. LEDs first featured a phosphor coating on the reflector cup but now use a ceramic based technology where phosphor is coated directly on top of the light chip. VanRiper says this provides better consistency, output and improved color variation. Along with having the option to choose between red, amber or white for lighting systems, designers are able to choose various shades of white, from cool blue to warm white to meet an application’s lighting needs.
Another development that has come with LED technology is its ability to resist performance loss. Unlike an incandescent or halogen light, an LED will continue to perform even if it’s designed to a vehicle that has a voltage other than 12 volts. VanRiper explains “if you had a 24-volt vehicle, you could be sure the life of your 24-volt [incandescent] lamps would be 1/2 to 1/3 of a 12-volt vehicle with comparable lighting.” This would result in a lot of bulbs being changed on a vehicle.
To offer customers with vehicles running on multiple voltages more flexibility, Truck-Lite and J.W. Speaker can design some LED lights to be multi-volt products. The circuit on these lights adjusts to the input voltage from the system. “For those companies that might have 12-volt and 24-volt vehicles,” says VanRiper, “we can actually make a multi-volt system that allows the lamp to work by sensing the voltage and adjusting the appropriate power for the LED.” This way companies will be able to inventory the same light for all of its vehicles.
Thermal management
One of the keys to ensuring LEDs will last as long as expected is proper thermal management. Moore says that heat is produced at the back of an LED with almost no heat emanating from the front. According to Popovic, this happens because LEDs produce conductive heat, not radiant like a halogen lamp. LEDs are very sensitive to the heat they produce, and as the temperature of an LED goes up, the light output decreases. If overheated enough times, an LED will be prevented from ever reaching its full brightness again, says Moore.
Lighting companies thermally manage LEDs in a number of ways. Moore says one of the most common is the use of a heat sink, which is a metal housing for the reflector and LED board. Heat is carried away by the housing’s surface size, in a similar fashion to a car radiator. This is why some LED lights will have “fins” on the back, says Moore, for increased surface area. Baja Designs uses a thermal management circuit in the heat sink to measure the light’s temperature. If the temperature exceeds programmed parameters “the LEDs are automatically dimmed until the temperature lowers,” says Moore, “then the LEDs go back to full brightness.”
Popovic also notes that without proper thermal management, an LED can fade quickly. Without a properly designed lighting system, an LED can fail prematurely after 1,000 or 2,000 hours, or in extreme cases, after 10 hours, says Popovic.
To help ensure longevity and output, J.W. Speaker uses aluminum boards as its method of heat dissipation. Popovic says this is because aluminum has the highest index of conductivity, besides diamond and copper which are much more expensive. The aluminum board is paired with an aluminum housing which encompasses the entire light system. Heat is able to travel from the LED to the aluminum board, then on through the aluminum housing out into the environment, thus preventing the light from overheating.
Baja Designs, on the other hand, uses copper for heat dissipation. Moore says the copper core boards provide the thermal management necessary for off-highway applications which tend to drive LEDs harder.
Requirements such as LM-80 Lumen Depreciation Lifetime Test Method can help ensure proper thermal management design. Linda Rivers Bell, Global Director for Lighting Product Development at Federal-Mogul Corp., Southfield, MI, says it enables companies to determine if their lights are fading too quickly. Specified by the Illuminating Engineering Society, it requires an LED product to be tested to a fade point of 80%. This is the luminous flux remaining output which is expressed as a percentage of the maximum output. “This allows us to design the lamp based on the amount of time it would take to reach the 80% point to ensure that customer requirements are met,” says Bell.
Why LEDs “fail”
Besides improper thermal management, numerous other factors can cause an LED to fail sooner than anticipated. VanRiper says that as LED technology developed, weak links emerged in the areas of sealing and connectors. To create a more robust product, he says many companies have begun sealing their LED circuit boards in a potting compound. They have also been designing stronger connectors. Since LED lights have evolved to a fit-and-forget type of device installed on the vehicle, says VanRiper, the connector system needed to be more robust as well to ensure power would reach the lights no matter where they were located.
Popovic says the problem with LED lights failing is not the light source itself, but one or more of the other components which encapsulate the LED. He says it’s the plastic and aluminum housings around the LED that break first or the sealant that’s used. When these materials break, they can cause outside elements like water to get inside the light system and cause the electronics to short out. “The light source outlives all the stuff that you have to build around it,” says J.W. Speaker’s Mayrand. “It’s kind of an interesting problem to have.” Before with incandescent, halogen or HID technology there were also components which outlived the light source.
Another factor Popovic notes that must be kept in mind when designing a lighting system is the conditions in which the light will be used. Elements such as the temperature outside need to be taken into account because of LEDs’ sensitivity to heat. “Sometimes you’re mining or on top of a tractor in the Arizona sun,” says Popovic, “and you have to consider those inputs to make your system work with the LED.” Output and lifespan can diminish greatly if these aspects are not considered.
Mayrand says trying to drive more electrical current through the LED can cause problems as well. Attempting to overdrive the system to get more light will generate more heat and thus shorten the life and output of the LED.
The future of lighting
Because LEDs are becoming so prominent in lighting design, companies are constantly working on enhancing the technology itself as well as the other components involved in lighting systems. For vehicles being used in explosive environments, such as mining or construction jobsites, Truck-Lite has been working to design explosion-proof lighting. VanRiper says the LEDs’ heat generating properties can be a hindrance in these types of applications. However, the company has found ways to prevent the LEDs from becoming the source of an explosion.
Truck-Lite has also been working on adapting LED technology for use in emergency warning lights and hazard warning lights as a replacement for strobe lights. This is because LEDs have a 20 millisecond faster bloom time than incandescents. Bloom time refers to how quickly a light can produce 95% of its relative luminous intensity. The instant-on appearance of the LEDs enables the warning lights to be seen much faster. VanRiper offers an example: “At 60 miles per hour, which is 88 feet per second, a trailing vehicle would see the stop signal and have 20 feet more of stopping distance because he saw the signal sooner.”
VanRiper notes that the life and efficiency of an LED helps make it a more desirable choice for warning lights, as well.
While many see LED technology completely dominating the market over the next several years, they are also starting to see other technologies coupled with lighting. J.W. Speaker’s Popovic sees intelligent lighting, photoelectronics and infrared technology being developed more. With intelligent lighting, the technology will be able to anticipate what the vehicle is going to do and illuminate the appropriate area.
According to Mayrand, J.W. Speaker has already begun working with infrared or thermal imaging for some of its products. Because thermal imaging relies on invisible wavelengths of light, a vehicle operator can detect a person, animal or object in total darkness and at distances four times beyond what headlights can illuminate. Already in use in many military applications, thermal imaging can also be of use in mining or other off-highway industries. The thermal imaging allows a vehicle operator to see through dust as well as farther into the distance. “It’s quite diverse and can be used anywhere where visible light may not be enough to cut it,” says Mayrand.
Popovic and Mayrand say they are also seeing a shift towards organic LEDs (OLEDs) in some areas of lighting design. This type of LED has a flat surface which randomly and uniformly emits light, whereas traditional LEDs emit light from a single point. Popovic says organic LEDs get their name from the silicone-carbon based organic matter contained inside the light. Though still in the beginning stages of development and use, Popovic says it’s becoming an attractive technology because it’s an entire panel which uniformly emits the same brilliant white light.
“There are two words which will drive all industry lighting,” says Popovic. “Safety is number one, and performance is number two.”
***Need a "head to oemoffhighway.com" circle somewhere in article that says: Search 10381728 at www.oemoffhighway.com to read Baja Design's whitepaper on selecting the right LED light.***