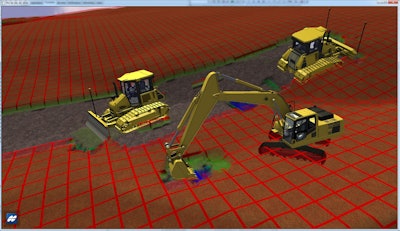
First there were sensors. Then came GPS satellite location and navigation. Now we have ambiguous ideas like Big Data and the Internet of Things (IoT)—the network of interconnected devices exchanging data from manufacturer to user to other connected devices in an effort to maximize the capabilities and services for all parties involved.
Even ten years ago, GPS (global positioning systems, often referred to in the context of consumer grade products) and precision systems were flashy and relatively rare, seen as upgrades and high end options to enhance a vehicle’s performance. GNSS (global navigation satellite systems, in reference to multi-constellation professional grade systems which incorporate GPS [US], GLONASS [Russia], Galileo [EU] and/or BeiDou [China]) is now such a proven and widely accepted technology, it has become just another one of the many sensors that contribute to the accuracy and position of an off-highway vehicle in the field.
There are more constellations coming online all the time forcing providers to constantly having to change their systems to support them. While most current systems offered track all signals, in the past system providers would have to improve the RF (radio frequency) sections of the GPS receiver and develop different antennas to receive the new signal.
New receivers are also capable of supporting hundreds of channels at one time. Topcon in particular has a patent on universal channels, so each channel can be used to track whatever signal is needed without having to increase the channel count. The next generations of systems coming onto the market will continue to improve upon the quality and consistency of the systems.
Consider how common it is becoming to have a sense of place geospatially, whether using social media, a navigation system or using a search tool to find nearby amenities. How is this expectation influencing the technology designed into a vehicle? Certainly there are a lot of things being considered. For instance, knowing who entered the vehicle cab and how they are operating for performance metrics, knowing what other people and/or machines are in the nearby proximity to the vehicle for enhanced safety, and local information sharing between devices in the field.
There is no doubt that the world is heading toward more and more sensors as we become used to—and even expecting of—the idea of “logging in” to access information or perform a task remotely from anywhere on any device. “Technologies like Bluetooth Smart are making devices aware of their surroundings, which is a very interesting concept,” says Jason Hallett, Vice President of Product Management, Topcon Positioning Group. “You can imagine that these devices might be able to auto-configure equipment for specific tasks, and provide instant and secure access for identified users.”
But, while it may seem that the GNSS technology is light years beyond where it was less than a decade ago, it is not without challenges, namely that it still requires clear sky, avoiding solid object obstructions. “The signals are pretty weak coming off the satellites, so when you get underneath tree coverage, in a tunnel, or next to tall buildings, it’s very difficult to get quality positions,” says Hallett. “So, we’re improving antennas and integrating other sensors into the systems to improve, augment, or assist the GNSS position when in those types of conditions.”
There are technologies available to carry the vehicle’s position forward, at least temporarily, when a signal is lost, such as IMUs or SLAM. SLAM technology (simultaneous localization and mapping) uses previously recorded images to back-calculate the location of the vehicle. These technologies work for well in short-range scenarios, until clear sky can be achieved again. “I’m sure we’ll be seeing more long-range technologies impacting systems in the future,” Hallett says.
What an OEM wants
OEM expectations have changed as the abilities of the positioning and accuracy measurement systems continue to increase a vehicles performance significantly for the aftermarket. An OEM can easily see that if it integrates positioning systems with its own innovations, the vehicle will be taken to the next level. “And it’s not just about knowing the approximate location of the vehicle on a project; it’s about knowing exactly where the vehicle is, what the position of the blade is, and using dual antennae and IMU’s to track rotation and trajectory. At that point, you can fully automate the machine,” Hallett says.
Topcon has been doing machine control more than twenty years. “It started as an aftermarket technology and gained adoption with OEMs offering optional systems. Now what is happening is a far deeper integration of more advanced systems, and in certain cases, the co-creation of very advanced systems in partnership with the OEMs,” says Hallett. “The market is beginning to expect this level of integration. I don’t think it will be long before all machines have GNSS as a standard feature.”
What’s next
“We’re seeing a trend toward combining traditional RTK corrections with network and/or satellite distributed correction services, so a user can get the best position available, in more conditions,” Hallett says. Topcon, for example, has a distribution of base stations around the world for its RTK correction service, TopNET Live, and the GNSS systems also support satellite-based correction services for areas not covered by the TopNET Live network. “TopNET would deliver accuracy from a base station at about 1-2 cm accuracy, if you are within range of one of the stations (typically within 20km). The satellite-based systems typically deliver accuracies around 5-10 cm, which might be good enough for the task they are performing, such as clearing a site or working a field. A simple interface alert would let the operator know what correction services are available.”
One thing that is absolutely growing in demand is web-based services. For example, Topcon’s SiteLink3D.net and Enterprise products that help machines exchange information and data between the office and the field, or between each other in the field. It provides data control, machine tracking and reporting in one system.
“We can provide remote support and actually see the operator’s display, so if they are having trouble or are just learning the system, a support person can connect to their machine, take over and help guide the operator in the vehicle to get it back up and running,” explains Hallett. “There is a strong and growing demand for these connected web products and services. A site manager can monitor activities, see what materials have been moved, get volume reports and pass counts, and exchange data effortlessly. The expansion of these services are one of the next areas that is really going to help increase productivity on job sites.”
Efficient and truly optimized machine control requires a plethora of electronics, sensors, software and networked communication. GNSS is just another mandatory and expected piece of the puzzle. “We’re so much more than GNSS now, and you have to be,” says Hallett. “We make everything from optical and GNSS products, to remote sensing, IMUs and auto steering systems. All of these products and the prevalence of sensors, both on and off a vehicle, will play a role in delivering more value to the end user and the OEM as they continue to become integrated into the connected IoT network for real-time and historical monitoring applications.”