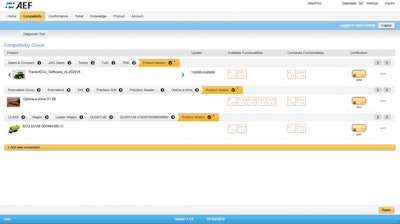
Equipment sales in the agricultural industry are expected to be down all over the world once again in 2016. Though there may be some regional differences due to governmental policies or weather condition—parts of Southern Europe including Spain and Italy, for example, have seen slightly improved conditions—the industry is forecasted to remain in a cyclical downturn for at least the next year.
Many manufacturers already adjusted to this downturn last year by cutting back on production and staffing levels. However, one area where investments are still being made—though at a lower level due to budget constraints—is in new technologies.
Peter van der Vlugt, CTO Mechatronics at Kverneland Group and chair of the Agricultural Industry Electronics Foundation (AEF), says the last thing a company should pull back on is investments in R&D because it will need to be prepared to meet the current and future requirements of its customers, especially once the market begins growing again.
“Fast communication structures, machine-to-machine (M2M) communication with direct access to the internet, short range or long range communication, are all things that will be needed,” says Norbert Schlingmann, soon to be General Manager of AEF and currently Development Manager, Electronics Integration at CLAAS. “But [OEMs] have to reduce their R&D budget, which is tricky. They know they have to develop this technology otherwise it will be difficult to keep up with their competitors.”
The next wave in vehicle communications
The technologies utilized for precision farming (also referred to as smart farming, or Farming 4.0 in Germany) such as GPS and automatic guidance systems, smart sensors and telematics, will continue to be a growth area for the agricultural industry. It is currently projected to grow 15-20% until 2025, says van der Vlugt. Further advancements in vehicle communications—whether it’s from one tractor to another or between a tractor and an implement—will be an important aspect of this.
Today’s farmers, and especially the new, younger generation of farmers expect their agricultural equipment to have the same performance and connectivity as they have in their cars and smartphones. They want to be able to easily exchange data between machines while using uncomplicated interfaces.
Connectivity between different equipment brands is of particular importance, and something which AEF has been working on since its inception in 2008. Though more common in Europe than North America, many farms utilize equipment from various manufacturers. Because of this, ensuring a tractor from one OEM will be able to seamlessly communicate with an implement or tractor from another manufacturer is critical to a farmer’s operations, as well as an OEM’s ability to keep its customers’ business. “The crucial challenge for AEF is the [need to] streamline the development in our companies to benefit our mutual customers,” says van der Vlugt.
This is achieved through the various AEF member companies—which include OEMs, component suppliers and organizations such as the Association of Equipment Manufacturers (AEM)—working together through project teams to help standardize electronics and communications technologies used within agricultural equipment. One of AEF’s first accomplishments was the establishment of ISOBUS as the universal protocol for electronic communication between implements, tractors and computers. By making this the agreed upon communication standard for the industry, manufacturers can ensure their equipment will work properly with that of competitors and aid customers in managing their farming operations.
Five independent test laboratories, located in the U.S. and Europe, are available for manufacturers to certify their communication systems are ISOBUS compliant. Once certified, their information is entered into the ISOBUS database, an online portal that provides manufacturers, dealers and customers with information on various pieces of machinery and which ones are compatible with one another.
“Now based on the fundamental acceptance of ISOBUS, we are going to further expand the technologies that are needed for the future like high-speed ISOBUS, wireless in-field communications and extending FMIS (farm management information systems) data,” says van der Vlugt.
Last year, AEF established two new project teams focused on high-speed ISOBUS and wireless in-field communications. The wireless in-field communication team will work to standardize what radio signals are used for M2M communication while working in the field, as well as examine communications encryption and functional reliability.
AEF Project Team 10: High-Speed ISOBUS will work to find ways of increasing bandwidth on the communications bus. CANbus communication speeds are becoming limited, says van der Vlugt. As more ECUs are connected to the CANbus, the more bandwidth that is eaten up.
Mark Benishek, AEF Secretary and Technical Director at AEM, explains that today’s CANbus system is like a freeway; as more traffic travels on the freeway, traffic flow begins to slow down and expansion to the system is needed to speed up traffic flow once again.
“If you consider new technologies…wanting to communicate on some sort of bus system, CAN is not enough,” adds van der Vlugt. In the automotive industry, manufacturers have begun implementing CAN FD to handle the higher bandwidth requirements. However, he says AEF sees this as an intermediate step and that CAN FD will not be able to handle the future communication needs the foundation foresees for the agricultural industry. As such, communication protocols such as Industrial Ethernet which will work alongside existing ISOBUS technologies are among the technologies being investigated by the project team
No matter what communication protocol is chosen, AEF’s goal is to ensure it will use the same connector interfaces available today and that all of the ISOBUS equipment is backwards compatible.
“Time and critical communications will be staying on the CANbus because it’s a very robust system,” says van der Vlugt, “and high-speed ISOBUS will be used for different means.”
Advancements in the communications system are also being used to improve serviceability for the dealer. “Companies are working on it to support their service organizations to give them better feedback on the machines and wireless connections, as well,” says Schlingmann.
With current CANbus systems, downloading new software onto a machine can take anywhere from 15-25 minutes. Implementing new high-speed connections, however, have the potential to reduce this down to as few as 1 or 2 minutes. In the future when more wireless capabilities are available, Schlingmann foresees technicians being able to automatically update a machine from their office instead of driving to the farm to do so manually, saving time and costs.
Additionally, the ability for a dealer to predict when a component will fail before it actually does and send or take the customer a new one will become more feasible in the future.
Working together for the greater good
Actually developing the new communications technologies, however, is a different story. “We’re [OEMs] experts at developing and producing ag machines, we know what we have to do and the processes behind it. But we do not have the same experience with communication technologies, it’s new for us,” says Schlingmann.
An OEM may have a lot of experienced mechanical engineers who are able to work on various aspects of an equipment design, but do not have the training to develop the communication and electronics systems necessary for M2M connectivity. And with reduced R&D budgets, it can be difficult for an OEM to invest the time and money into these new technologies.
However, many of the larger OEMs have begun investing in “knowledge centers” focused on new communications and electronics technologies—Kverneland Group Mechatronics, John Deere Intelligent Solutions Group and AGCO’s Fuse Technologies are just a few examples. Through these groups companies are cultivating engineers to be experts in communications systems and associated technologies, and then work together with the mechanical engineers to implement those systems into equipment designs. “Every major manufacturer is building up competence on high tech farming with electronics, data and GPS,” says van der Vlugt. “It’s [been] a change in our companies over the last decade.”
Organizations like AEF and AEM can aid this new era of communications development, as well, by bringing manufacturers together to discuss systems development and evaluate what works or what doesn’t. They enable manufacturers to learn from one another and work together to develop products that will benefit the industry as a whole, while still allowing manufacturers to maintain their proprietary information and competitive edge. Benishek says one of the advantages of all the OEMs being a part of AEF is that there will be assurance for farmers of compatibility of communications systems now and in the future as these technologies advance further. “With AEF, we know exactly what we have to do,” says Schlingmann. “We have to combine our ideas to go in one direction.”