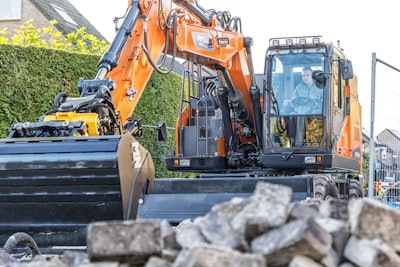
While environmental benefits are often championed as the primary reason to look at alternative power sources, off-highway and construction equipment manufacturers have many reasons to switch to hybrid and fully electric systems and machines. While there are emerging environmental regulatory requirements resulting in machine and system electrification, many original equipment manufacturers (OEMs) are taking advantage of the performance improvements to reduce their customers’ operating costs and improve machine productivity.Electrified machines increase machine productivity and reliability, and they reduce maintenance costs.Junttan
The Driving Forces Behind the Electric Transition
While a positive total cost of ownership (TCO) for most large machines has yet to be realized, given the costs associated with the substantial amounts of energy storage required, TCO can be quite compelling for smaller and medium-sized machines and even larger machines for certain applications.
While initial acquisition costs are typically higher for electrified machines than their conventional diesel-powered counterparts, electrified machines yield operating cost benefits by reducing the total energy consumed because of the higher efficiency of electric systems and their ability to capture and store energy through regeneration.
Electrified machines also increase machine productivity and reliability, and they reduce maintenance costs. In some cases, operators of hybrid or electric machines and systems see more than a 50% improvement in productivity and 20% to 30% reductions in operating cost. These improvements help owners and users recover their investment in the more expensive machine in less than one year.
During the past few years, customer decarbonization obligations and investor pressures have influenced OEMs to develop equipment that supports their operational objectives and commitments. According to a 2019 IEA report, building construction and operations accounts for approximately 39% of CO2 emissions globally, with around 11% coming from the construction industry. In some regions, developers must report on and meet emission targets which are increasingly difficult with traditional construction equipment.
For example, Komatsu, a construction, mining and forestry equipment manufacturer, is aiming to reach carbon neutrality by 2050. The company's comprehensive roadmap, which addresses Scope 1, Scope 2 and Scope 3 emissions, shows a significant commitment to carbon neutrality, demonstrating how the influence of the market and anticipated regulatory pressures have led to an explosion in demand for solutions to address emissions from industrial and construction operations.
To achieve significant reductions in the construction industry, construction machines will have to change. Therefore, to meet emission reduction pledges, many construction industry players are turning to component and subsystem manufacturers to find powerful solutions to achieve their targets.
Regulatory Changes Also Play a Role
The final key driver is the dynamic and evolving regulatory environment. To reach emission reduction targets, new local, national, and international mandates require that traditionally heavy-polluting industries make serious changes to their operations. These regulations are increasingly common, particularly in the E.U. They are often the catalysts that drive equipment manufacturers to commit to environmental emission reduction targets as they anticipate increasing mandate requirements and the global reach of those mandates.
However, not all regulatory restrictions are climate related. Noise regulations are also a significant and growing category. Compliance is vital to site productivity, with permits required to perform work during authorized working hours. This can affect meeting project timelines and, in some cases, operator and employee wellbeing. More work sites are requiring reduced operating hours or permits based on evidence of minimal noise pollution disruption in neighborhoods.
Electrified machines can play an important role in helping contractors meet these demands because electric systems are much quieter than diesel engines and traditional hydraulic systems. Additionally, eliminating mechanical components, which are essential in conventional internal combustion engines, makes electric machines unmatched for reducing noise pollution levels.Electric equipment has improved efficiency and quieter operation.Doosan
A Purpose Design System Architecture for Each Application
The diversity of off-highway machines is extensive, but with this variety comes the need for attention to application and system design details to ensure that machine performance and improvements are realized. Therefore as with traditional diesel and hydraulic systems, a collaborative effort between the OEM and the electrification system solution providers is critical.
While not all applications are currently suited for full electrification, those that can benefit from a fully electric or hybrid solution typically outperform legacy systems because they are quicker, quieter and more responsive. They use less energy and enable higher precision for their work functions. Electric systems also provide immediate power and torque, are more productive, and provide a faster dynamic response for operators.
Embrace an Electrified Construction Industry
The off-highway industry faces pressure to change, and it’s becoming increasingly clear that electrification is a fundamental part of the solution. For those who want or need to invest in a new machine for their construction site, hybrid-electric and full-electric offerings delivering high performance, reduced emissions, reduced noise and a lower TOC are becoming a natural choice. Moreover, with the added consideration of external pressure for more sustainable solutions and regulatory restrictions, investing in an electrified machine now is investing in the future.