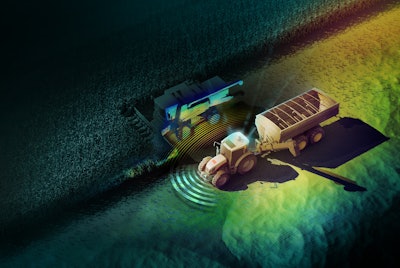
Danfoss Power Solutions, a global supplier of mobile and industrial hydraulics as well as electric powertrain systems, has partnered with Swift Navigation, Bonsai Robotics, and HARD-LINE to expand the offerings in its autonomous machine development platform. Danfoss will integrate the companies’ solutions into its PLUS+1 Autonomy software, enabling users to enhance their autonomous machines with Swift Navigation’s high-precision positioning service, Bonsai Robotics’ camera-based vision systems, and HARD-LINE’s teleoperations solution.
“Autonomous off-highway machines are becoming more sophisticated. As we advance toward Level 4 and even Level 5 autonomy, high-precision navigation and remote control beyond line of sight will become requirements,” said Peter Bleday, head of autonomy at Danfoss Power Solutions.
PLUS+1 Autonomy is a software platform designed to substantially reduce development time and facilitate rapid vehicle prototyping, to help OEMs get autonomous and semi-autonomous off-highway machines to market faster. In addition to its PLUS+1 Autonomy platform, Danfoss offers engineering services and ruggedized hardware. Danfoss Autonomy teams work with customers from concept to production, supporting full machine development.
Swift Navigation's Skylark precise positioning service offers decimeter-level accuracy from the cloud to PLUS+1 Autonomy, eliminating the need for additional ground infrastructure. It is well suited for industries such as construction, agriculture, and other applications that demand high-precision GNSS capabilities. Skylark covers a wide range of major markets, including the U.S., Europe, Japan, Korea, and Australia.
Bonsai Robotics is a fast-growing startup that specializes in camera-based vision systems for adverse conditions such as heavy dust, debris, vibration and lack of GPS. The system uses cameras instead of traditional positioning systems, enabling greater accuracy at very low cost when navigating the toughest conditions, including narrow rows of trees, vines or crops.
“Bonsai’s partnership with Danfoss has allowed us to rapidly integrate with several vehicle form factors in order to add vision-based autonomy and Visionsteer driver augmentation to equipment operating in some of the most challenging conditions,” said Tyler Niday, founder and CEO, Bonsai Robotics. “The beauty of PLUS+1 drive-by-wire systems is that an autonomous perception system can drive the PLUS+1 equipped vehicles through CAN bus messages in the same way that a human would use manual controls.”
HARD-LINE offers teleoperation services that enable monitoring and control of machines over the internet. The service complements Danfoss’ radio-based remote-control solutions, which allow operators to remotely control machines within line of sight. Teleoperations are ideal for operators supervising multiple autonomous machines. If a machine stops due to an unknown obstacle, the operator can log in to the HARD-LINE system, navigate around the obstacle then resume autonomous operation without needing to be close to the machine.