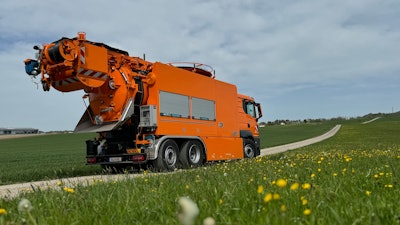
As the off-highway industry considers the electrification of larger and more demanding machines, on-vehicle power distribution becomes a critical consideration. Larger machines require more power, which translates to higher voltages and currents. For instance, a machine requiring 350 kW, would demand up to 438 A from an 800 V system. These current and voltage levels necessitate heavy-gauge cables, robust connectors and a rigorous approach to safety.
Four challenges for PDUs in off-highway vehicles
Every electrical machine requires at least one power distribution unit (PDU), which serves as the central hub connecting the machine's electrical system. At higher powers, every cable is point-to-point and must be properly terminated. Splices are not an option.
The PDU’s importance is more than connectivity; it is integral to the vehicle's safety architecture. While power distribution is already a familiar feature in buildings, requirements for off-highway mobile machines are far more challenging. There are several reasons for this:
- Space constraint. On-vehicle space is significantly more limited than in buildings, and shrinking the dimensions of power distribution equipment introduces both risk and cost. High-voltage components must be safely isolated. High voltages can “jump” or arc if components are too close together. As the available space shrinks, achieving safe isolation becomes an increasingly complex challenge.
- Harsh operating conditions. Off-highway machines operate in challenging environments, requiring PDUs to be protected from water ingress, and to withstand impact, accelerations and vibration. Even changes in operating altitude are pertinent, as arcs form more easily at higher altitudes vs sea level due to thinner air, necessitating additional design considerations.
- Choosing between direct or alternating current (DC/AC). Unlike buildings, where ac systems are the norm, machines normally use dc power. DC is more challenging to manage. It is harder to switch, potentially more dangerous for humans, and if arcs form they are difficult to extinguish. By its nature, alternating current changes direction so every 100 to 120 times per second the current will pass through zero, which facilitates switching.
- Thermal management. Thermal challenges are familiar to all designers of off-highway machines for most components and the PDU is no exception. For example, fuses capable of protecting a 500-A circuit generate considerable heat, and in a closed metal enclosure, good thermal management is required if temperature-related failures are to be avoided.
These factors make the power distribution solutions for mobile machines very different from those of established fixed installations. As a result, this is driving the development of a specialized engineering discipline and a range of dedicated technologies, products and solutions.
Why electrical integration is an underrated challenge
Few OEMs today have teams with deep expertise in high-voltage design. This skill set is relatively new, and skilled designers remain scarce in the industry. Even if an OEM could justify hiring a full-time high-voltage specialist, recruiting such talent is challenging.
The lack of in-house expertise often leads OEMs to underestimate the complexity of high-voltage system design. As a result, the PDU can become a critical path item on the project timeline, jeopardizing overall machine development schedules.
For smaller, low-power machines with simple operational requirements, off-the-shelf PDUs can be feasible. Lower currents and voltages mean less expensive components and make standard solutions easier and more cost-effective to implement.
However, as power requirements and operational complexity increase, a standardized approach becomes impractical. A universal PDU capable of meeting all customer requirements would likely be oversized and prohibitively expensive. The costs of components such as connectors, busbars, and contacts rise exponentially with power, making it uneconomical to incorporate components that are not strictly required.
Large cables carrying hundreds of amps further complicate matters, as they often have minimum bend radii exceeding 1 foot. The direction of cable entry into a PDU can dictate connector placement, which impacts the unit’s internal layout.
Prototyping PDUs with short lead times
The PDU design cannot be finalized until late in the machine development process, yet it is one of the first components to be installed. This makes lead time a critical factor for project success.
When it comes to high-voltage system integration, short lead times are a fundamental part of every project, particularly at the prototype phase. The materials and design choices for prototypes are optimized for rapid delivery without compromising safety or quality.
As OEMs move beyond the prototype stage to pre-series and volume series production, the priority requirements for PDUs rapidly evolve. The focus shifts from lead time to cost optimization. This can be achieved through lower-cost components with longer lead times, such as alternative enclosure materials, or designs that reduce assembly time.
For example, prototypes and initial production would often use a busbar design. Busbars are thick bars of copper with a rectangular cross section, bent to the required form. This is proven technology but it demands a time-consuming assembly of the PDU.
When moving to production volumes, it often makes sense to move to power PCB technology, which allows for assembly time to be reduced by as much as 90%. The higher tooling cost does mean this is only viable when the machine design is frozen, ready for series production.
Figure 2: Example of a power distribution unit (PDU).FÉTIS Group
Four advanced PDU capabilities
At first glance, a PDU may appear to be little more than copper, connectors and fuses. In reality, PDUs often incorporate advanced functionality, including:
- Circuit switching: This is to determine which parts of the machine circuit are live at different points in the machine operating cycle. The power to the wheels or an implement, should, for example, be cut when the machine is charging.
- Safety interlock systems: This ensures the machine only operates when all connectors are correctly plugged in.
- Pre-charge circuits: This reduces the voltage differential when closing a contactor, minimizing the risk of arcing.
- Discharge circuits: To safely discharge residual voltages.
These features make the PDU central not only to power distribution, but also to the machine’s overall safety and operational reliability.
Lowering system costs with a PDU
Although the PDU is one of the last components to be fully specified, it’s good to engage a high-voltage system integrator very early in the machine design process. Early involvement enables proper sizing of components which is key to cost management. The right expertise at the early stages reduces the number of design interactions and shortens the whole project cycle.