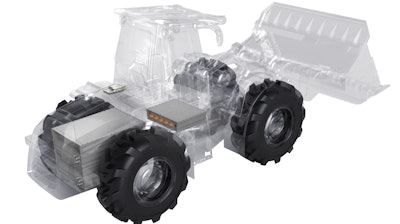
As electrification continues to advance in the heavy equipment and vehicle industries, so do the battery technologies available to power them. With these new battery technologies have come increases in power output as well as new applications in which they are employed.
Nikola Motor Co., for instance, announced in November 2019 it was introducing a new battery technology with energy density of 1,100 watt-hours per kg on the material level and 500 watt-hours per kg on the production cell level. The prototype of this battery removes binder material and current collectors, enabling more energy storage within the cell.
Use of the battery in Nikola’s battery electric trucks could enable them to drive 800 mi. (1,287.5 km) fully loaded between charges, and reduce their weight by 5,000 lbs. (2,268 kg) compared to the competition if the same battery size was kept. Nikola’s hydrogen-electric fuel cell trucks could surpass 1,000 mi. (1,609.3 km) between stops and top off in 15 minutes.
Mourad Chergui, Product Manager at Delta-Q Technologies, says battery technology has reached a point at which it allows heavy equipment to have the same duty cycle—typically an 8-hour shift—as traditional power sources.
CASE Construction Equipment’s recently introduced fully electric backhoe loader is a demonstration of this capability. The 580 EV, also known as Project Zeus, is powered by a 480V, 90 kWh lithium-ion battery pack which supports most common 8-hour workday applications on a single charge.
Advancements like these show battery technologies are overcoming many of the concerns regarding range associated with electric vehicles and equipment.
CASE's electric backhoe-loader is powered by a 480V, 90 kWh lithium-ion battery pack that can be charged by any 220V/three-phase connection.CASE Construction Equipment
More manufacturers enter the battery space
Development of electric powered equipment and vehicles will continue to increase in the coming years. As such, over the past several years many component manufacturers have begun diversifying their product portfolios to include batteries.
Webasto—probably best known for its heating and cooling products—introduced in November 2019 its commercial vehicle (CV) Standard Battery System. Designed for scalability and configuration flexibility, the battery pack provides 35 kWh of energy and allows up to 10 packs to be combined to provide enough power for larger equipment applications.
Josh Lupu, Director of Marketing at Webasto, says the company started investing in high voltage technology around 2010 due to the increased interest and future growth it was seeing in regards to hybrid and electric vehicles. “We created the high voltage heater. That was our first entry into e-mobility or the electric powertrain,” he says. “That was the start of Webasto diversifying into non-combustion powertrains.”
In 2016, the company started developing charging stations and acquired a charging station company in 2017, which is also when it started developing the CV battery system. It is a nickel rich NMC (nickel manganese cobalt) prismatic cell battery. Webasto chose the NMC chemistry because it provides high energy density as well as a long life. “We have a lifetime of 3,000 cycles or 8 years,” says Lupu. “This means if you fully discharged the battery if it was at 100%, and then fully charge it back up to 100%, you could do that every day for 8 years.”
He says in reality that is not how people will use the battery; no one usually fully discharges and recharges it, but it’s been verified that it can withstand that type of use. “It's very robust and made for extreme use cases,” adds Lupu.
Webasto chose a nickel manganese cobalt battery chemistry because of the high energy density and long life provided.Webasto
Briggs & Stratton is one of the latest engine manufacturers to announce its entry into the battery development market. “We've identified that there's a gap in the marketplace of people that are powering units anywhere from 0.5 kWh up to 20 kWh,” says Christine Davison, Senior Manager Marketing, Engines & Power at Briggs & Stratton. “We believe there’s a big opportunity there.”
She says there are some manufacturers offering lead acid batteries in that power range, but not lithium-ion technology. The company wanted to offer a flexible lithium-ion solution for this power range, and so developed the Vanguard Commercial Lithium Ion Battery pack.
In addition, the company saw where the markets it serves were heading in the coming years and wanted to position itself to be more agnostic about the types of power systems it offers.
Key markets it is looking at for the battery pack include construction, agriculture and traditional outdoor power equipment such as lawn mowers. Equipment that would be used inside a building would benefit from using it to protect the health and safety of workers as there would be no exhaust fumes emitted as would otherwise be the case with a gas engine.
Davison says the system is customizable to an application. “Although we first launched with a 5 kWh 48V pack, as we move forward, and as more products and more customers are being developed, those packs can be customized to an application.”
She notes that an advantage of Briggs’ technology is that it only uses the power that is needed for a specific application. “You’re not using anything extra, you’re not paying for power you don’t need, which is a huge advantage for the OEMs we will be working with,” says Davison.
The Vanguard battery comes with the battery management system as well as the controller and charger, offering a complete package for OEMs.Briggs & Stratton
A complete, modular system
Creating a system which is modular and can be customized to an application is beneficial for OEMs looking to develop electric vehicles. Having the ability to choose how many battery packs to use in a machine based on its power needs helps ease their design process.
Lupu says Webasto’s is a plug and play system which reduces development time, cost and resources for OEMs. “We've had several customers want to use this system because they can have one supplier, one battery pack that they can use across their full product line. They can use one [battery pack] on this piece of equipment, two on another piece of equipment, and 10 on yet another, which significantly simplifies their R&D.”
Providing a complete system is also a key aspect. Davison says the Vanguard battery comes with the battery management system—which ensures all components work together properly and safely—as well as the controller and charger.
In addition, she says Briggs & Stratton is able to help OEMs with the design and integration of the battery. The company does all of the assembly and testing of the battery system which helps reduce development time and costs for equipment manufacturers. “Putting together the battery cell module and integrating it with the charger, battery management system, controller and motor is really where we deliver value because we’re bringing that whole system together to work,” in the OEM’s application, says Davison.
Webasto also provides a complete system consisting of the battery and vehicle interface box (VIB) which Lupu says is the brains of the system; it will load balance, houses the charging interface, constantly monitors the cells and keeps everything in a safe operating range. Proprietary software developed in-house by Webasto is used in the VIB to recognize how many packs are hooked up and if they’re being run in parallel or series.
Lupu says the same box and packs can be run at 400V if connected in parallel or at 800V if connected in a series. “That’s significant because it allows the manufacturer to be flexible in their design process.”
It also prepares OEMs for the future because Webasto knows voltages will start to increase in the coming years. Right now, 400V is the norm for high-voltage electric powertrains. But Lupu says that in the near future it will rise to 800V, with many manufacturers already developing systems in this power range. “When you do that, you're able to achieve more power with less current, which means you're running cooler, can use thinner gauge wire and can charge the system faster,” he explains.
The VIB has provisions for both the standard 240V AC , level 2 charging (J1772) and DC fast charging, says Lupu. “It is completely up to the manufacturer which they choose to use in their application.”
Webasto’s battery is liquid cooled; coolant paths within the battery enclosure use a 50/50 water glycol mix to cool it. Lupu says manufacturers can choose to use one of Webasto’s many battery cooling systems, one of which was developed specifically for the CV Standard Battery. It is an all-in-one heating and cooling system capable of cooling the battery system with a capacity of 5 kW. Liquid heating capacity is in the range of 7-10 kW and provided by the company’s high-voltage heater. Sensors continuously monitor the temperature of the battery cell and command the use of heating or cooling to keep the system in a safe operating range.
The first demonstration of the Vanguard battery is on an ARGO J8 unmanned ground vehicle.Briggs & Stratton
Integrated battery charging
In talking with OEMs and end users, Chergui says there is a drive toward having less maintenance on batteries. As such, they are wanting higher power levels, faster charging as well as the ability to utilize public charging infrastructure.
Briggs & Stratton notes the Vanguard Battery Packs are serviceable which makes them unique within the market and will be beneficial for end users.
Regarding charging technology, Chergui says the trend is moving toward integration of battery chargers into a piece of equipment. On-board charging makes it easier for end users to charge the machine anywhere instead of having to go back to a home base and charge for several hours overnight, which Chergui says is typical with lead acid batteries. “I would attribute [the shift] to the emergence of lithium battery applications which require higher input rates,” he adds. “Having the equipment on board is definitely the way to go.”
Growing use of lithium batteries lead Delta-Q to develop its latest charger, the RQ350, which is the company’s smallest and lowest powered charger at 350W. “When an OEM converts from a lead acid to a lithium battery, the vehicle and battery is much lighter,” explains Chergui.
The lithium battery is 20-30% more efficient, and thus smaller than its lead acid counterpart which allows the charger to be smaller and more compact, as well. Because of this, their use in various off-road applications—particularly compact equipment—is growing.
Development of the RQ350 came about due to increased conversion to lithium-ion batteries which could use a smaller charger.Delta-Q Technologies
Chergui notes the lawn and garden segment, particularly mowers, is rapidly adopting battery technology. He says in the last 3 years the company has seen a huge shift from gas to electric in this segment which helped trigger the company to develop its latest chargers.
Global emissions regulations and efficiency improvements will continue to drive development of electric power systems—and thus battery technology—in the coming years. “We’re going to see a lot more normalization of electrification and a lot of the components are going to be driven toward [becoming] a commodity item,” says Kevin Rhodes, Chief Engineer of Electrification at AVL. “That’s important because right now, a lot of things have to be custom made.”
He believes a lot of components such as chargers and inverters will become standardized as power levels and use cases become more normalized. This will help drive down costs. He believes it will be the same with battery technology, which is currently a large cost driver of an overall electric powered system.
Rhodes says more battery chemistries will continue being developed and more manufacturers will get into the battery space. “I think right now is really a great time to get into that space because it's just going to continue moving very rapidly. And if you're not getting on board with it right now, as a company, you're going to be left behind to some extent, and you really need to at least be advancing your knowledge of that and be ready for the changes that are going to be coming in the next 5, 10, 20 years,” he concludes.