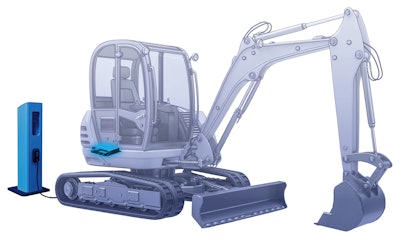
As the global drive toward electrification continues reshaping industries, original equipment manufacturers (OEMs) in the off-highway sector face growing regulatory pressures. These challenges demand innovation, but they also present a chance to leverage solutions from parallel sectors.
There are several ways the off-highway industry overcome obstacles in achieving electrification and build toward a thriving future.
A Generational Model for Electrification
Historical breakthroughs often guide future innovations. Similarly, the evolution of electrification in adjacent sectors indicates a clear trajectory for off-highway machinery.
Electric forklifts and indoor machinery serve as prime examples of early electrification efforts. While industries often credit the automotive sector with pioneering electrification, few recognize the material handling sector laid the foundational groundwork for this innovation. These machines demonstrated early success with emissions-free solutions in demanding environments, paving the way for modern passenger electric vehicles (EVs).
With stricter CO2 emission regulations driving change, the same pattern repeats today. Off-highway electrification now benefits from mature electric technologies—such as advanced charging solutions—developed in parallel industries.
Figure 1: Decarbonization and adherence to environmental over time and by type of vehicle.ZAPI Group
With future growth anticipated in higher-powered, industrial applications, OEMs can utilize established markets as case studies for developing electric and hybrid solutions.
This progression a three-part “generational model” of electrification, comprising:
- Generation 1 – Early proof-of-concept designs using standard parts from other industries to create an electric drivetrain.
- Generation 1.5 – A phase of iterative refinement, with design decisions focused on enhancing performance, reducing costs, and delegating more tasks to suppliers.
- Generation 2 – Full maturity, where third-party integrators manage optimized subsystems, allowing OEMs to focus on market-specific customization and seamless integration.
Fully integrated drivetrains mark the ultimate goal. By replacing systems composed of disparate parts with cohesive designs, each component works in harmony for maximum efficiency.
Chargers: The Centerpiece of Integration?
Achieving this integrated future in electrified machinery starts with the right charging solution. An OEM’s charger selection is not an afterthought, but the backbone of next-generation drivetrains.
Two factors support this statement:
- A charger tailored to the machine’s application improves the battery’s efficiency, safety, and lifespan. Since the battery is often the most expensive component, it makes sense to protect this investment and maximize its value with the right charger.
- Charging an electric or hybrid machine is far more complex than refueling an internal combustion engine counterpart. An on-board charging solution is non-negotiable in bridging the gap between the machine’s battery and varied charging infrastructures.
The second point is particularly crucial given the significant growth in EV charging infrastructure—a market anticipated to be worth $12.1 billion by 2030.
This circles back to the charging solution. On-board chargers simplify logistics and broaden recharging options for OEM machinery across various settings, from public EV stations to basic ac wall plugs.
Figure 2: Example of electric powertrain system integration.ZAPI Group
Unlocking these efficiencies—such as opportunity charging for heavy construction equipment—requires chargers designed to meet the specific challenges of off-highway applications. Without them, the vision of seamless electrification remains incomplete.
Real-World Developments and Applications
Besides meeting sustainability goals, emerging technologies continue to redefine the electrification landscape and fuel new OEM designs. Consider these four examples:
- Gallium Nitride (GaN) and Silicon Carbide (SiC) drive new efficiencies in power electronics, reducing losses and improving performance.
- Lithium batteries deliver greater energy density and smarter integration capabilities, meeting the ever-increasing power demands of industrial machinery.
- Battery management systems (BMS) enhance operational safety, provide predictive maintenance insights, and adapt charging profiles for maximum battery performance.
- CANbus protocols facilitate remote fleet monitoring and management, streamlining operations and reducing machine downtime.
Real-world applications exemplify the possibilities of these technologies in off-highway applications, expanding options for OEMs and end-users alike.
For instance, Delta-Q Technologies, a ZAPI GROUP company, operates an automated battery charger test lab for applications ranging from golf carts to construction. By calibrating custom charging profiles and algorithms to match the application, the facility ensures every charger maximizes battery cost performance.
ZIVAN, another ZAPI GROUP company, leverages advanced communication protocols to empower fleet managers with real-time analytics and charge control. These “battery rooms” extend battery life by implementing strategies like first-in-first-out rotation and automated recharge management. Such tools allow managers to predict maintenance and replacement needs, regardless of fleet size or complexity.
Both case studies underscore a crucial point: OEMs must cultivate strategic partnerships to navigate electrification efficiently and at scale.
Overcoming Integrated Solution Challenges
While internal combustion engines rely on discrete components working together to generate motion, an integrated electric drivetrain operates differently—each component enhances the performance of the others.
Figure 3: On-board and off-board charging solutions.ZAPI Group
This interconnectedness requires OEMs to navigate certain trade-offs—particularly between flexibility and cost efficiency.
For example, consider two potential scenarios when upgrading an electric drivetrain:
- Upgrades for non-integrated setups are a simple process. Each component can simply be replaced as needed. Although this approach incurs a higher upfront cost due to varied parts and design complexity, it provides significant flexibility for future modifications.
- A fully integrated solution presents a greater challenge given its interconnected design architecture. Though optimized for cost and performance, such a solution lacks the flexibility to swap or upgrade components independently.
These examples aren’t intended to discourage a fully integrated future. Rather, it showcases the considerations OEMs must address when electrifying. Even partially integrated systems face similar trade-offs, requiring design teams to balance performance, cost, and flexibility for their specific applications.
Finding that balance and overcoming these limitations, again, hinges on collaboration.
Rather than transactional supplier relationships, OEMs must prioritize strategic partnerships with electrification experts such as the ZAPI GROUP of companies—leveraging their cross-industry insights and supply networks to develop electrified solutions tailored to meet evolving demands.
Developing Electrification Partnerships Are Key for the Future
Cross-industry expertise has always been the engine of innovation, and today’s off-highway machinery sector is no different. The only difference is electrification is no longer optional—it’s a regulatory and operational necessity.
As the industry moves toward fully integrated solutions, partnering with electrification experts from the initial design stage is crucial. Such a proactive approach will allow OEMs to avoid expensive backtracking and ensure a seamless transition to an all-electric future.
Electrification isn’t just about powering machinery. It’s about powering progress—and OEMs who embrace these technologies will lead the way.
Rod Dayrit is the global director of business development for ZAPI GROUP charging solutions.