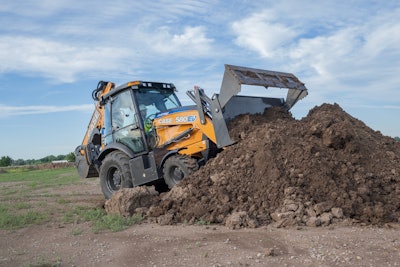
Electrification has always been a major aspect of off-highway vehicles and technology and recent trends have made it even moreso. The mining, agriculture and construction industries are grappling with changes and challenges to the power grid and how their vehicles are powered. This is even more acute with the tide shifting towards alternative energy and fuels as a viable source in certain applications.
These industry experts on the off-highway industry offered their insights on electrification in a roundtable format:
- Dr. Wilfried Aulbur, senior partner, Roland Berger
- Eric Azeroual, vice president, sales development and portfolio, Danfoss
- Lloyd Gomm, global director marketing, ZAPI GROUP
- Brady Lewis, P.E., manager, emerging products & technology, CASE Construction Equipment
- Athan Tsokolas, product manager - commercial Lithium-ion batteries, Vanguard
- Chris Wadsworth, VP and GM, global OEM, Wesco.
Question: How do safety and operational standards influence the development of electronic systems in off-highway equipment?
Eric Azeroual: Functional safety and cybersecurity are critical in off-highways vehicles. These new requirements increase the software and hardware development costs and have to be taken into account from the beginning of the development in a strong partnership between suppliers and OEMs. However, these standards are already well underway in the on-highway market, which allows companies to benefit from these developments and lower costs.
Lloyd Gomm: At the operational and safety level, electric systems must be designed to meet the same standards as delivered by legacy technology. But, electronic systems have the potential to offer more in terms of efficient, safe operation. An example of this is incorporating automotive radars, which offer wider fields of view and improved hazard detection, even in adverse conditions, to ensure safer autonomous and semi-autonomous operation.
Brady Lewis: Safety and operational standards are a good way for the industry to share best practices and enhance the state of the art. Many product development companies work to stay abreast of the latest advancements in their field and contribute back to the industry as a whole, especially on topics involving safety.
Question: What role do industry organizations and standards bodies play in shaping trends?
Dr. Wilfried Aulbur: The role of industry organizations and standard bodies is multi-faceted. On the one hand, industry organizations need to clearly articulate the challenges that the industry faces on its quest towards decarbonization. These challenges and costs need to be clearly addressed, as they will have to be passed down to consumers at the end of the day. Realistic timelines need to be communicated and a fact-based discussion of adequate technology solutions needs to be fostered.
Collaboration with NGOs needs to be strengthened but on the basis of fact-based discussions and mutual respect. Without such a collaboration (the onus being on all participants in these discussions equally) we will face an environment in which policy making becomes difficult and may swing widely depending on who is in power. Such a situation is sub-optimal for OEMs, suppliers, NGOs and the climate. From a standard body perspective the key focus should be on establishing standards that enable scale while taking the need for developing a local industrial base into account.
Eric Azeroual: Industry organizations, such as AEM, help OEMs and suppliers understand what is happening in the market. Industry benchmarks can confirm or refute assumptions, but ultimately OEMs have to stay on top of not only what the competition is doing, but also what their end users want.
Lloyd Gomm: Industry organizations, such as the IEA, are essential in standardizing and scaling electrification, especially given the current lack of global uniformity in:
- Duty cycle measurements
- Charging connectors
- Battery chemistries
- Voltage architectures.
Such organizations also influence policy and regulations, ensuring electrification efforts align with sustainability goals with minimal industry fragmentation.
Brady Lewis: The off-highway EV industry is still in its early stages of growth. Similar to when the automotive industry first began, there are many players each trying to improve the product and application in different ways. The industry organizations and standards bodies serve a critical function to improve communication between players and help the entire industry advance forward.
The CASE 580EV, the industry’s first electric backhoe in full production, combines innovative design with powerful functionality for a big leap forward in electric construction machinery.CASE Construction Equipment
Question: How are advancements in electronic systems enabling automation and autonomous operation in off-highway equipment?
Dr. Wilfried Aulbur: Various sensor technologies, real-time edge computing, improved communication protocols and other technologies are the basis for autonomous applications and have seen rapid improvement over the last years. As a consequence, autonomous mining trucks are very visible in global mining operations and their penetration continues to grow. Turf applications are being increasingly automated and even tractor applications are moving towards autonomous tillage.
The key challenge for all autonomous applications in construction, agriculture and mining is not the machine in itself, but its operation in an overall jobsite workflow. For example, an autonomous grader might finish its job significantly faster, yet this benefit is irrelevant for customers if the workflow is not optimized to take advantage of this efficiency increase. In other cases such as agriculture, quality management becomes a challenge. While visual inspection of the quality of tillage may still be feasible with cameras and sensors, it becomes much more difficult for sowing. Hence the future is most likely one in which the operator intensity of many jobs will be reduced but operators will still be key at managing autonomous vehicles on job sites.
Eric Azeroual: Electronics and software are essential to enabling modern autonomous control systems. In off-highway, we automate the tasks a machine performs, so the components performing those tasks must be electric or electrohydraulic — that’s the first prerequisite. The second is high-power controllers to provide the processing power necessary to run the autonomy algorithms within normal machine control loop times. Autonomy also requires perception sensors such as lidar and radar, global positioning, and other electronics. Advancements in hardware accuracy, reliability, and suitability for off-highway environments has made autonomous operation possible.
Lloyd Gomm: Component-level advancements, such as electronically controlled actuators, enable greater precision in steering, braking and throttle control — establishing an optimal foundation for autonomous machinery. Smart hydraulics and load-sensing technology serve a similar purpose, feeding essential data that allows automated systems to dynamically adjust operations based on current conditions.
Athan Tsokolas: The off-highway sector is undergoing a significant shift toward automation and autonomous operation, fueled by the increasingly vital role of electronics. Electrification is key to this transformation because it enables advanced software integration and unlocks autonomous capabilities that enhance functionality. The result is greater productivity, improved safety and optimized fleet management. While autonomous solutions offer immense potential — particularly in high-risk environments and labor-intensive applications — industries are still working to strike a balance between advanced capabilities and cost-effectiveness.
Chris Wadsworth: Autonomous vehicles are high on the radar of many industrial organizations, especially as advancements in AI and machine learning evolve at a near breakneck pace. These vehicles have the ability to not only address productivity and automate manual processes, but mitigate issues with labor shortages on the jobsite. For example, without a human to operate a 400-ton vehicle, you can reduce labor costs and gain efficiencies as these vehicles can run 24 hours a day with no break and no need to change drivers. If operating in a remote area, this further reduces the burden on the need to find and retain labor. AI can then amplify the impact of autonomous vehicles by automating and improving processes.
Consider how AI might find the best route for a haul truck as it navigates to the deepest depths of a mine, all without a human driver, eliminating a significant safety risk. However, for all the innovation, it’s worth noting that none of this can work without updated network infrastructure. Truly the underpinning to any technology undertaking, the ability to run these systems continually and maintain communications with each machine is critical to ensuring success.
Question: How are advances in electronic systems enabling automation and autonomous operation in off-highway equipment?
Lloyd Gomm: AGVs and AI-driven automation address the growing labor shortage, particularly in structured environments like warehouses, where predictable routes simplify autonomous navigation. Mining and agriculture likewise see increasingly complex autonomous operations, improving productivity without human intervention.
Question: What challenges exist in integrating sensors, cameras and control systems for autonomous functionality in rugged environments?
Lloyd Gomm: There are three challenges to consider:
- Harsh conditions – Dust, vibrations, extreme temperatures, and water exposure can degrade sensor accuracy and lifespan.
- Connectivity limitations – Remote worksites may suffer from poor network coverage and latency issues, reducing real-time responsiveness.
- Processing constraints – High-resolution sensor data (LiDAR, radar, cameras) demands edge computing to avoid delays and guarantee real-time decision-making.
Chris Wadsworth: Internal communication network reliability and bandwidth can be a challenge. Organizations need to make sure they have the right network infrastructure in place to handle the additional data load these systems create — not only today, but in the future, as well. Businesses also need to make sure that their overall system is designed to meet their unique needs and budget.