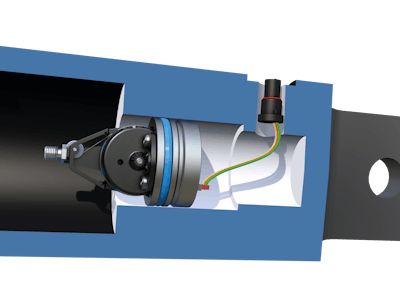
Smarter hydraulic systems which include sensors and other electronic componentry are becoming ever more prominent within the mobile equipment industry, helping to increase the accuracy and efficiency of these systems. Like all companies, sensor manufacturers are continually evolving their products in order to further advance the capabilities of the systems in which they’re integrated.
Flexibility and ease of installation were key criteria for Rota Engineering when it was developing new features for its position sensors for hydraulic cylinders. These sensors will now include field calibration and installation capabilities, and were introduced at CONEXPO/IFPE 2017 (booth S84130).
Mark Hoffman, Vice President of Sales & Marketing at Rota Engineering Ltd., says the new features will provide an OEM the flexibility to install the sensors when necessary, and help reduce part numbers which will in turn lower costs. Warranty cost and complexity will also be minimized as the sensor itself can be swapped out instead of having to remove the entire cylinder in which it's integrated.
Installation of the sensor is as simple as screwing it into the end of the hydraulic cylinder, says Hoffman. Once installed, the entire sensor is encased within the cylinder to protect it from external elements. Only the sensor’s nut and wire for connecting to the power and signal electronics is exposed.
Hoffman says the ease of installation is beneficial for both manufacturers and end users, and is particularly advantageous for very large hydraulic cylinders. “Sometimes these sensors go into cylinders that are so big it requires something like a forklift or telehandler to actually remove the cylinder from a piece of equipment,” he explains. The field installation capabilities, however, eliminate the cost of using such tools should there be a need to remove or replace the sensor. “With our package, they would simply unscrew the sensor, put a new one in, [and be] back up and running.”
MTS Sensors also recently introduced a field-serviceable sensor, the Flexible MH (FMH) linear position sensor. It features a two-part design to separate the flexible sensing element and electronics from the sensor housing without the need to open the hydraulic system in which it's installed.
Giving customers what they want
According to Hoffman, the new position sensor features Rota is offering are those for which the market was asking. To implement them, he says it was a simple software addition to the sensors which are micro-processor based.
Field calibration of the sensors enables factory calibrations to be overridden, and customers can select any portion of the active stroke zone to output a full-scale signal to achieve maximum resolution. The Rota position sensor screw into hydraulic cylinders and is completed integrated other than the wiring necessary for connecting to machine electronics.Rota Engineering Ltd.
Hoffman explains that a cylinder manufacturer may have an 8 in. (203.2 mm) stroke cylinder designed to offer a certain voltage over that stroke measurement. However, there may be times the cylinder never makes it to that full stroke length. Field calibration enables the voltage to be modified to fit the actual stroke measurement without having to modify the cylinder or replace it with a different one. This allows the cylinder manufacturer to stock a single part number—the Rota position sensor—to meet varied cylinder requirements.
OEMs can also benefit from stocking just one part, both in the case of the sensor and the cylinder. In many cases the position sensor may be an optional component to a hydraulic system or machine design. As such, the OEM can stock one cylinder part number and add the sensor during machine production when necessary, providing further flexibility and cost reduction opportunities. “They’ve got one sensor for several different applications,” says Hoffman.
“As the requirements of IoT (the Internet of Things) grow, flexibility to fit into many different business models is paramount. Flexibility, robustness, ease of installation and warranty cost drive these new features,” he adds.
When developing its SGH10 wire-actuated sensor, SIKO GmbH worked closely with customers to ensure its new sensor design would meet their needs. Precision and accuracy were among the key requirements for the SGH10 which provides direct stroke measurement. Initially debuted in 2015 and highlighted at bauma 2016, the sensor was introduced to the U.S. market at IFPE 2017 (booth S83815).
In its press release introducing the SGH10, SIKO says precisely determining the stroke of a cylinder to measure and monitor machine motions to be carried out is one of the most important tasks for sensor technology integrated into hydraulic systems. Because of this, “both machine and sensor manufacturers are always looking for new innovations in stroke measurement for hydraulic cylinders.”
Precision measurement
To ensure precision and accuracy, SIKO made its SGH10 wire actuated. This enables the position of the cylinder to be precisely detected at all times in comparison to inductive, magneto-restrictive or hall-based sensor measurement technologies. While wire actuated encoders have existed in the market for some time, the company says this is the first time they have been used with hydraulic cylinders.
The sensor is designed to be installed directly into a hydraulic cylinder, with its wire mounted in the piston head and wound up in a wire drum. When the cylinder extends, the wire is pulled out which causes the wire drum to rotate. Magnets within the sensor detect this rotation and are scanned by sensor electronics through the SGH10’s pressure-resistant base plate to calculate linear travel.
All of this is accomplished without contacting the sensor electronics which are encapsulated on the unpressurized side of the sensor system. The lack of contact eliminates wear and increases the lifespan of the sensor system.
The entire sensor, in fact, is installed directly into the hydraulic cylinder to protect it from external elements. Unlike a sensor mounted externally on a cylinder, with the SGH10 customers will not have to worry about sensor information being compromised by damage or loose parts. Everything is safely contained within the cylinder and meets protection class IP69K, ensuring durability in harsh applications.
SIKO notes that the sensor was designed specifically for mobile applications, and as such has a high resistance to shocks and vibration, as well as high electromagnetic compatibility.
Like the Rota position sensors, flexibility is also an important feature of the SGH10. Analog or CANopen outputs can be used with the sensor, and programmed over the sensor’s whole measurement range (0-1,000 mm/0-39.4 in.) to reduce the number of variations a manufacturer will need to keep in stock. SIKO's SGH10 sensor is capable of being installed in telescoping cylinders.SIKO GmbH
Additionally, the SGH10 can be integrated into telescopic cylinders, expanding the systems and applications in which it can be used.
Integration costs can be reduced, as well, with the SGH10 as it does not require piston drilling like other systems do. SIKO says other systems often require the sensor rod to be integrated into a piston over the entire measuring path which is costly and can weaken the structure of the piston. The SGH10, however, requires only a small thread put into the piston in order to mount the sensor cable.
As the use of smart hydraulics continues to grow within the mobile equipment industry, sensor features such as precision, accuracy, flexibility and ease of installation will remain important factors to ensuring intelligent hydraulic system performance.