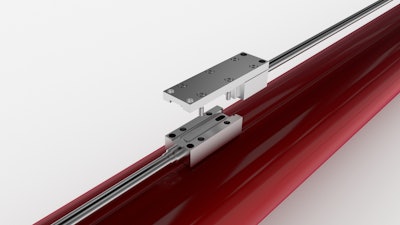
Sensors for hydraulic and pneumatic cylinders have migrated from inside the cylinder to the outside of the cylinder tube over the last several years. This is due to an increasing need for measuring position and providing feedback of longer stroke lengths. Sensors on the outside of the cylinder tube also provide cost-effective warranty and non-warranty support, as the sensor itself can be replaced without having to touch the cylinder.
As OEMs have automated more of their machine functions, longer cylinder stroke position measurement has become a requirement to enhance machine safety and efficiency, says Michael Moore, Technical Sales Engineer at Rota Engineering Ltd.
According to Moore, internal cylinder sensors only covered a certain range of potential applications. “There were certain downsides to an internal sensor, particularly on long stroke cylinders,” he says. “The longer the stroke, the more difficult it is to integrate an internal sensor.”
In addition, it is more costly to purchase and integrate sensors into longer stroke cylinders.
The need to help bring down this cost drove Rota to develop sensors which could be used outside the cylinder. “We found that with Hall Effect technology, we could come up with magnet designs that could work with the linear sensor on the outside of the cylinder tube as opposed to the inside of the cylinder,” says Moore.
Read more: Terex Introduces Electric Boom Lifts Using Rota Hall Effect Sensor
The Modular Linear series sensor is capable of measuring long cylinder stroke lengths.Rota Engineering Ltd.
He notes that boom measurement applications provide some of the longest stroke lengths to measure. Rota’s Hall effect technology has measurement capabilities up to 40 m (131.2 ft.), enabling it to be used in boom measurement and a variety of other applications requiring long measured lengths.
This experience with sensors capable of measuring long cylinder stroke lengths was beneficial to the development of Rota’s newest sensor, the Modular Linear (ML) series sensor. Moore says the challenge wasn’t whether it could measure a long stroke length but instead how to implement a solution with a minimal shipment, handling and installation cost when measuring at those lengths.
“The Modular Linear series sensor was created to address that need, while providing a more reliable and robust solution compared to competing technologies,” he says.
Longer cylinders require longer, more modular sensors
Moore says the ML sensor grew as an extension of Rota’s standard EL series (external linear) sensor. This external linear sensor can be located outside on the cylinder tube with its corresponding magnet located inside the cylinder.
Most hydraulic cylinders with internal sensors typically range in size from 6 in. (15.2 cm) up to about 6 ft. (1.8 m), he says. But because there are also a number of cylinder applications on machines that are longer, Rota developed the standard external linear sensor to measure the longer cylinders while saving on integration costs.
The ML sensor is an extension of Rota’s standard EL series, an external linear sensor which can be located outside on the cylinder tube.Rota Engineering Ltd.
“But at some point, depending on how long your application was, how could you handle the logistics behind the sensor? How do you package it? How do you ship it? How do you unpack it? How do you install it? All while keeping from damaging it? All of those issues came to the forefront with an extremely long, single-piece sensor,” says Moore.
The cylinder sensors have a small diameter of about a half an inch or smaller and are made of aluminum. If they’re long and thin—as they would need to be for long stroke cylinders—the sensors can flex, bend or kink if not handled carefully.
“If you had up to a 6 or 7 ft. (1.8 or 2.1 m) long single-piece sensor it was no problem,” says Moore. “But once you start pushing the length of the sensor [over] 10 ft. (3.0 m), it becomes a problem.”
A long, single-piece sensor is not only difficult to handle but also expensive to package, transport and ship.
Read more: A technology's reach expands, both figuratively and literally
To overcome these challenges, Rota examined the possibility of breaking the sensor up into sections. This would make it easier to package and transport, as well as unpack and install by building out each section until the required length is achieved.
Rota was in fact able to achieve this, bringing about the ML series sensor. The Hall Effect technology enables the sensor to be self-contained in a small diameter tube surface mounted to, for example, a boom section. As a fully solid-state sensor, it has no moving parts and does not need to contact its corresponding magnet on the opposing boom.
The ML series provides OEM customers with a modular design which can be assembled on site in sections, saving on shipping and installation costs.
Moore says the modular linear design provides a manageable way to contain the costs of all the logistical factors that need to be taken into consideration for sensors being used in hydraulic and pneumatic cylinders with long stroke lengths.
Rota Engineering Ltd.
Hall Effect technology increases capabilities
The ML series sensor was developed for any customer requiring the use of long cylinder strokes or mounting on boom sections—such as in mobile cranes, telehandlers and aerial work platforms.
Moore says it could be used by any OEM needing to measure between two moving parts. The key factor is the sensor gets mounted to one structure and the magnet is mounted to another structure. “The Hall Effect technology we have allows you to place a magnet in proximity to the sensor. It does not have to fully surround the sensor like other technologies require,” he says. “The movement of the two structures has to be such that the magnet will stay in proximity of the sensor all throughout stroke travel in order to have a constant signal.
“As long as that proximity can be maintained, you have a way to get measurement information using the Rota Hall Effect sensor.”
Rota defines proximity in two ways:
- offset—the actual distance between the magnet and the sensor
- tolerance of the offset—the amount of play within that offset i.e. how close or far away can you go without affecting sensor performance.
And because there are no moving parts involved—both the sensor and magnet are fixed entities—reliability issues that may have been a concern with other sensor solutions are eliminated (see sidebar below).
The company has a range of magnets that allow for different offsets and tolerances, says Moore. And the range continues to expand as customers’ needs change. Typical offset dimensions can range from 0.5 up to 2 in. (1.3-5.1 cm).
Magnets get larger and more powerful the farther away from the sensor they are, which can increase costs. “We find the initial sweet spot of using it has been with boom systems because boom sections are generally within an offset range and tolerance that our standard magnet range will work with just fine,” he says.
Hall Effect technology allows magnet designs which can work with the sensor on the outside of the cylinder tube as opposed to the inside of the cylinder.Rota Engineering Ltd.
While booms are a common application for the sensor, there are others in which it can be used. There is a similarly designed sensor integrated into a vertical blast drill. The sensor is mounted at the top and bottom of the mast, and the rotary head which travels up and down the mast as it’s rotating the drill pipe contains the magnet. The magnet comes within proximity of the sensors at the top and bottom of the mast. Use of the sensor in this manner helps ensure proper threading of the pipe being drilled.
Moore notes one of the good things about Hall Effect sensor technology is the fact it can be pushed up to 40 m in length as a single operating sensor. This enables it to be used in a variety of applications.
While developing the ML sensor, Moore says understanding the various measurement lengths necessary for heavy-duty equipment was a necessity. Most important though was working with OEMs to learn what offset and tolerances of offset existed on machines in the market so manufacturers would not have to redesign their equipment to use the sensor. The company needed to understand what spacing existed between boom sections that would allow the technology to fit and operate between the steel sections of the booms.
The Rota ML Series sensor allows for redundancy by placing two ML sensors side-by-side on the cylinder or boom section. With proper understanding of spacing between the boom sections, a single magnet can operate two ML sensors, providing redundancy of signal. For hydraulic cylinders, the magnet design allows a range of operability allowing two ML or EL sensors to mount side-by-side achieving redundancy of signal.