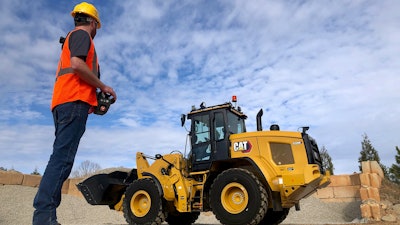
Caterpillar announces the expansion of Cat Command to a broader range of construction machines. Cat Command is now launching a line of remote control and semi-autonomous technologies, ranging from operator-assisted compaction to remote control loading, dozing and excavating operations.
Scalable technologies built to flexibly meet customer needs, Cat Command helps to enhance safety and increase productivity for a variety of applications. Remote control provides full machine maneuverability from a safe distance when working in potentially hazardous environments. By removing the user from the cab, it also eliminates machine vibration feedback felt by the operator, reducing fatigue. Helping to address current and future labor shortages, the technology expands machine operation to a larger pool of potential operators, through its “virtual cab,” which offers easy access to accommodate those with physical limitations.
A single user can quickly and easily control multiple machines, one at a time, or change jobsite location without traveling from the office to the machine, significantly improving operating efficiency and reducing travel time and costs. Remote control affords continuous production immediately following a disruptive process, like blasting, to increase machine productivity. Cat Command helps reduce work disruptions due to weather conditions or non-production related issues to improve machine uptime.
Precise remote control
Cat Command Console and Station controls are fully integrated with the machines’ electronic and hydraulic systems for quick response and smooth control. Operating commands are sent directly to the machine’s electronics through a dedicated radio transmitter/receiver, resulting in real-time control. Since the system is a dealer-installed kit fully designed and integrated into the machine, not an aftermarket add-on, Cat Command can be quickly switched between similar machines to give the customer increased machine flexibility.
The line-of-sight Cat Command Console comes complete with a lightweight, compact control console supported by a comfortable shoulder harness. Controlling all machine functions, the Command Console allows the user to work safely and comfortably away from the machine, while remaining onsite and in direct visual contact with the equipment. This solution requires no onsite communications infrastructure and is ideal for short-term and emergency use when encountering a potentially hazardous work area.
The Command Station offers the flexibility of being located onsite for line-of-sight operation or positioned miles away for non-line-of-sight applications. The station includes a modular, customized “virtual cab,” where the user is comfortably seated in front of machine controls and displays similar to those inside the operator’s cab. Offering an improved working environment, the Command Station allows users to work for longer periods of time without fatigue, and one user can remotely operate multiple machines, one at a time, from a single station.
The Cat COMMAND for Compaction touchscreen interface.
Assisted compaction
The semi-autonomous Cat Command for Compaction technology automates soil compaction to help contractors meet high compaction quality standards. By automating the process, it allows operators of all experience levels to deliver consistent compaction results. Command for Compaction is available as a dealer-installed kit on new and B-Series Cat soil compactors.
With no back-office design required, the operator simply uses the intuitive in-cab display with touchscreen interface to quickly map the boundaries of the area to be compacted. The operator then enters compaction parameters and sets the machine to auto. The system automatically controls compactor propulsion, steering, vibration and compaction overlap. To supplement an operator’s safety awareness, an integrated object detection system alerts the operator of an obstruction in the roller’s path.
CONEXPO-CON/AGG demonstrations
Caterpillar’s “Technology Hub” at CONEXPO-CON/AGG 2020 housed two Cat Command Stations configured for remote, non-line-of-sight machine control from inside the company's Festival Grounds exhibit. Throughout the duration of the show, attendees were welcome to sit in the “virtual cab” and control equipment – a Cat D6 XE dozer, 930M wheel loader and 320 Next Gen excavator – located from just under 500 to more than 2,300 miles (800-3,700 km) away.
Cat Command for Loading
Caterpillar has also expanded Cat Command for Loading to its small wheel loader line. Removing the operator from the machine, Command provides semi-autonomous remote operation of Cat 926M, 930M and 938M models to increase operating safety in potentially hazardous operating environments.
New Cat Command for Loading for small wheel loaders will be available in both line-of-sight and non-line-of-sight operating configurations. By allowing the user to comfortably control the machine from a safe location, Command maintains high machine productivity in operating environments such as stevedoring, steel mill blast furnaces, industrial and waste, and demolition and site decommissioning. Cat Command for Loading on Cat Small Wheel Loader.
A new dealer-installed field kit will make the Cat 926M, 930M and 938M models Command-ready. The system includes rear and side cameras, electric over hydraulic steering system and Command activation lever mounted conveniently on the machine for ground-level access. Installed on the cabin roof are cameras, indicator lights, microphone, wireless receiver, and antenna. Since Command controls are integrated with machine electronics, users will experience the same control response as they would operating inside the cab, allowing for productivity to be maintained from a distance.
Flexible remote configurations
Line-of-sight Command for Loading operation comes complete with a lightweight, compact control console supported by a comfortable shoulder harness. Basic machine controls like wheel loader startup/shutdown, bucket rack/dump, and lift/lower are easily accessed through the ergonomic Command console control layout. Machine commands sent from the remote console are sent directly to the engine and implement electronics via a detected radio, reducing machine response delay.
To ensure the user maintains machine control at all times, integrated Caterpillar electronics activate several safety features to stop all wheel loader movements if: A-stop or E-stop switch is pressed; wireless communication is lost; a severe fault is detected; or the Command console is tilted more than 60 degrees from normal operating position. Line-of-sight control with the Command console extends up to 437 yd (400 m) to allow for convenient remote operation.
The non-line-of-sight Command for Loading solution includes a modular, customized Command station that positions users in a familiar and comfortable seated position that simulates traditional machine control. One user can connect multiple machines from a single station, but only control one machine at a time. It is also compatible with other Command offerings for Cat equipment, such as excavators and dozers.
Station components include machine joystick and foot pedal controls for all the company’s Command technology capable machines. A touchscreen mount is incorporated in the station design for machine control, while universal screen mounts are included for camera displays of the wheel loader. An emergency A-Stop or E-stop button is located on the Command station to quickly halt all machine movements. At the jobsite, an optional remote All-Stop control is available for people working around non-line-of-sight Command loaders.