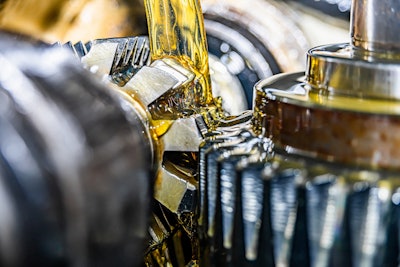
Elitza Terzova is global sector manager for mining at Shell Lubricants Solutions.Shell Lubricants Solutions
Take, for instance, the artificial intelligence (AI) industry, which could end up consuming as much power as a country the size of the Netherlands in the next three years, with the data centers involved to likely need an extra 1 million metric tons of copper by 2030. Miners will be the ones required to meet this rapid growth in demand, while also being under pressure to deliver on their own ambitious commercial and sustainability goals.
The sector finds itself in a perfect storm of change, and the challenge lies in finding feasible ways to navigate it. So, how can miners deliver the seemingly impossible? How do they produce more, while emitting less and remaining competitive?
The vital efficiency equation
While the challenge of decarbonizing mining operations and achieving greater productivity might seem at odds with each other at first, they do not have to be addressed separately. An efficient mine, enabled by well-maintained machinery, equipment and off-highway vehicles, can support more sustainable and productive operations.
Well-maintained equipment and vehicles can reduce downtime incidents, minimize carbon emissions and enable optimal output — a win on all fronts. So, what is the common factor that makes these efficiency wins possible? The answer lies in something that is critical to mining success but is often overlooked in busy mining operations — effective lubricant selection and management.
Why lubrication has a big impact
At first glance, it might not sound like lubricants could have a significant impact in meeting ambitious commercial and sustainability goals. However, effective lubrication is critical to vehicle and equipment health, which impacts operational efficiency, productivity and overall costs.
For example, look at draglines. The downtime costs of these machines can be anywhere between $30,000 to $100,000 an hour. So, the longer the equipment is inactive, the more the costs mount. While this might be one of the more extreme examples of how unplanned downtime can affect mining operations, the principle holds true across a site’s operations and equipment inventory.
Take mining vehicles for example. Whether they are carrying heavy loads or working for long hours in some of the harshest operating environments and conditions, their maintenance costs can spiral. But by selecting the right high-performance lubricant for each vehicle application and managing these correctly with a preventative maintenance program, effective lubrication can extend the overall equipment life cycle, improve productivity, minimize unplanned downtime and have a significant impact on a mining operation’s bottom line. For miners looking to deliver on their commitment to sustainability, biodegradable lubricants with their low ecotoxicity and bioaccumulation, can help miners minimize the environmental impact of their operations, while delivering on their operational targets.
Why miners must focus on total cost of ownership (TCO)
So, if the case for using high-performance lubricants is clear, why are more than a quarter of miners not acting when it comes to lubrication selection and management and why are a further 35% stalling and only planning to address this area in the next 1 to 2 years?
The answer lies in the rising costs associated with mining operations. Rising operating costs are the number one challenge for site managers with a third saying the rising cost of consumables like fuel and lubricants will significantly impact their operations in the next 3 to 5 years. Of course, this comes at a time when some say addressing shareholder demands to increase profits and maintain low operating costs will remain a priority.
In this challenging context, it’s easy to see why lubricant selection and management might not be at the top of the agenda. In this environment, it’s critical site managers and operators continue to focus on the TCO of their operations and consider the significant long-term gains that can come from investment in effective lubricant selection and management programs. If upfront commodity costs are higher it stands to reason that miners need to maximize the potential of the equipment across their site and get the maximum value from the consumables powering and protecting them. Fuel consumption, for instance, can account for up to 80% of the lifetime cost of running a machine powered by a large diesel engine and effective maintenance and lubrication is key to improving fuel efficiency in mining equipment.
Maintenance is another dominant cost in any operation’s budget line. By selecting the right high-performance lubricants for each application — and managing them correctly — sites can reduce their overall maintenance budgets by up to 30% each year, despite lubricants accounting for only 5% of a mine’s total costs. With lubricants and an effective maintenance strategy, miners can improve productivity and drive output while addressing rising costs.
However, despite the clear wins effective lubricant selection can deliver, it is often overlooked in mining operations. In fact, more than half of miners believe senior stakeholders in their business do not give lubricants selection and management the importance they deserve.
So, there is still plenty of work to be done to convince miners at all levels on the difference effective lubrication can make to their business. It is also important to highlight “effective management” is a key phrase for miners because the efficiency improvements do not stop at lubricant selection.
Driving further efficiency gains with expertise and digital solutions
Selecting the right lubricants can have an immediate impact in enabling miners to operate more efficiently, productively and sustainably. However, it’s only when miners also manage their lubrication systems by bringing in digital tools and expertise that they can enable the most impactful efficiency gains.
Lubricant suppliers’ technical services can help miners to make informed decisions through expert analysis. Oil condition monitoring (OCM) for instance can help to detect potential equipment failures early, allowing sites to prevent unplanned downtime and continue to operate productively. The benefit of this expertise is being increasingly recognized across the industry. When considering lubricant suppliers, over a fifth of miners are seeking a company that can help them increase the productivity of their current mining operations.
Digital technologies also have an essential role to play in helping miners to improve their operational efficiency while they decarbonize and cut costs. For example, using sensors and machine learning, mines can predict when components are likely to fail enabling predictive maintenance programs and helping to extend component lifetime by up to 50% to further improve TCO, enhance site sustainability and increase operational efficiency. In fact, by 2035, the age of smart mining is predicted to save the industry up to $390 billion each year.
Unlocking new mining potential
Miners already have many of the answers and solutions needed to drive operational efficiency, improve TCO, and manage the significant commercial and sustainability challenges facing their industry. However, the significant role lubricants could play in supporting these efforts is often overlooked.
When it comes to producing more while emitting less, this can depend on how efficiently a site’s mining equipment and machinery — legacy and new — are operating. As miners continue to adapt to the changes facing the industry, selecting and applying high-performance lubricants, biodegradable lubricants and implementing effective lubricant programs, are critical for miners. They can help enhance the operational efficiency of their sites, extend equipment life and reduce TCO while delivering the critical materials and services needed to transition to a lower carbon future.