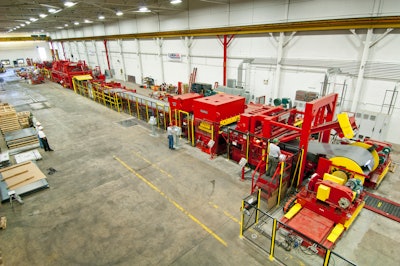
High Steel Service Center LLC, of Lancaster, PA, has introduced HIGHSL, sheet and plate steel that is panel-flat and stress-free for laser processing. Produced on a new leveling line, the material will not warp or buckle during fabrication by sensitive equipment because all the internal stresses have been removed from the metal. The line is the first of its kind in the Mid-Atlantic region.
High Steel Service Center takes coil steel from mills and processes it for use by original equipment manufacturers, laser processors, sheet metal fabricators, and others who make a wide range of steel parts. In a multi-year market survey, the company demonstrated that flatness is a top issue in its markets, where internal stresses could cause material to warp during fabrication, reducing customer efficiencies and increasing costs. “This is a significant problem for fabricators running high-speed equipment such as laser, plasma and waterjet cutters,” says Jim Cunningham, vice president, sales and marketing. “It slows down their operations and can damage the equipment.”
The company addressed the market issue by investing $10 million in a Red Bud Industries stretcher leveler and two Bradbury roller levelers, one with eDrive technology, to produce HIGHSL. A unique combination of leveler machines, the state-of-the-art line stretches 100% of the material beyond its yield point to completely relieve internal stresses.
“This capability offers a unique competitive advantage to our customers by eliminating their number one challenge: problems relating to flatness and stress removal,” says Rick Bennett, High Steel Service Center president. “At the same time, we improve our customers’ product quality, increasing their manufacturing throughput and helping to reduce their operating costs.”
The new equipment provides a higher level of flatness when compared with stretcher levelers paired with flatteners or straighteners, temper mills or tension leveling lines. The eDrive roller leveler assists the stretcher leveler in complete removal of coil set and crossbow, important in heavier gauges and at higher yields, and generates about 50% of the energy it consumes.
The new line became fully operational in July, 2012. “Customers have confirmed that this is the flattest material they have ever received, both before and after laser processing. Most importantly, they have confirmed that it absolutely reduces their operating costs,” Bennett adds.