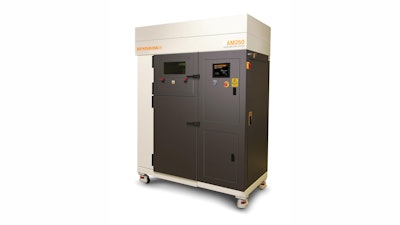
Today, 99 percent of the time on Directed Manufacturing’s five plastic additive manufacturing machines is committed to making
production parts. Those parts include fuel tanks, enclosures, winglets and other components for unmanned aircraft. They also include various specialized surgical instruments and surgical alignment guides. These selective-laser-sintered products are all complex, high-value and low-volume—perfect for additive manufacturing. In the past, additive processes were associated with prototyping. Now,
except for that remaining 1 percent of machine time, this is no longer the way that Directed’s customers view this capability.
But that’s plastic. The Austin, Texas-based additive manufacturing contractor uses 3D printing processes to make metal parts as well. Seeing additive manufacturing accepted for plastic part production took years, perhaps even decades. Materials and processes had to be proven, the company says, and designs and designers had to adapt to the geometric freedom that additive manufacturing makes possible. In metal, this acceptance is coming faster than it did for plastics, but it has not yet been won. The tipping point might come
this year. To date, most of the company’s additive metal capacity has been devoted to product development, but some of those developed products have now been committed to final manufacturing on the same additive machines. The company expects to buy more additive metal equipment to meet the growing demand.