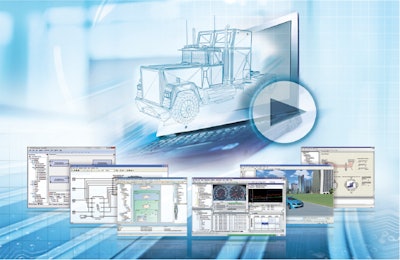
“All engineering organizations are under a lot of pressure to turn around product designs much quicker and to reduce their design costs,” says Paul Goossens Vice President of Applications Engineering at Maplesoft (company information, 10684595), Waterloo, Ontario, Canada. And having the right design tools at their fingertips can help engineers better meet these time and cost constraints. Creating tools that will make an engineer’s design process more efficient and productive is a constant goal of design software companies. They want to provide users with the ability to complete their design with ease and in a timely manner.
Including more capabilities within a software program—such as integrating more tools and automation—and developing easier-to-use interfaces through commonality to other programs are some of the key areas where engineers want to see improvements, and where many design software companies are focusing their efforts.
Integration of more capabilities
“The broad trend has always been towards integration. That is taking all the disparate parts and tools that are used to produce designs and get them to work together in some seamless kind of manner because a lot of things that one tool requires another tool produces, or that one tool produces a third tool will require,” says Alan Wegienka, President of Design Simulation Technologies (DST, company information, 11150366), Canton, MI. “The more you can have those technologies working together, the better it is.”
DST’s mechanical simulation tool SimWise enables users to perform 3D dynamic motion simulation and finite element analysis (FEA) of CAD models within a single software program. This eliminates the need to build physical prototypes, at least until later in the design process, which can be costly and time consuming. Instead, all analysis can be done in the software throughout the various stages of the design process; if errors are found, they can be fixed immediately. “The more you can do to increase that iteration speed—to look at a design and quickly determine if it’s good or bad or is going in the right direction and can proceed further—saves you time and saves you money,” says Wegienka.
Compatibility with other tools used in the design process is also an important efficiency feature. As a CAD-independent software, SimWise can read the geometry of models from any CAD system. Providing this capability enables engineers to place their CAD models within the software and immediately begin the simulation process without fear of transposing errors that could adversely affect their tests or time constraints.
In a similar manner, LMS International (company information, 10055729), Leuven, Belgium, built the ability to reference existing documents into its Virtual.Lab multi-body dynamics software (product information, 10924981). If a spreadsheet has been created that a user needs to reference, it does not first have to be converted in order for the spreadsheet to be accessed within Virtual.Lab. And like SimWise, Virtual.Lab also supports all of the common CAD and FEA formats for flexible body incorporation for a streamlined modeling process.
Maplesoft’s MapleSim Connector for JMAG-RT (product information, 10987413) creates high-fidelity system models using components from MapleSim (product information, 10930049) and JMAG-RT, an FEA tool from JSOL Corp. “It allows us to implement reduced order models from JMAG within the MapleSim environment,” explains Goossens. Bringing components from both programs into the connector helps save time and cost by completing simulations in one tool which take into consideration various factors that using the two programs separately might not have taken into account.
Automating design processes
Creating more automated processes within a software program can be a real time saver. Products such as SimWise which perform FEA testing help reduce the amount of manual work the engineer has to complete because all of the calculations are done in the software, and quickly. If a design issue is found, SimWise will automatically pinpoint the problem area and run further FEA tests on that specific area to figure out what needs to be fixed in the design.
Previously, FEA required a lot of expertise to accurately study a design and determine how best to break it down for further analysis if there was a problem. Automating this process, however, reduces the need for that expertise. Engineers can still get the information they need from the FEA tests to proceed with their designs without having proficiency in the subject. “That’s what we’re trying to do is remove a lot of this need for a deep level of understanding into the technologies,” says Wegienka.
For engineers developing embedded software in vehicle applications, dSPACE (company information, 10055313), Wixom, MI, introduced a simulation software called VEOS (product information, 10826112) that enables virtual validation of designs throughout the design process. VEOS allows engineers to continually test their software designs and fix errors early on instead of having to wait until the related hardware and software are both in the final development stages. “In developing this technology we ensured that the tools used for experimenting and testing in software development can be applied in this virtual environment,” explains Mahendra Muli, Director of Marketing and New Business Development at dSPACE. “That provides them a continuity of work and also reusability of experiments and tests throughout the development process.”
In addition to the core testing necessary during embedded software development, VEOS makes it easy to perform some of the more peripheral design tasks such as preparation of tests, data analysis, management of variances and versions of experiments, and development of experiments within the virtual environment. “It optimizes the cost, improves the return on investment, and gets the work done faster and in parallel because most of the software function testing can be done without the need for a physical product,” says Muli.
Design optimization is another area software companies are looking to bring more automation. As part of the newest version of SimWise, DST added an optimization tool which uses algorithms to help engineers determine the best possible configurations for a design. Wegienka explains that if an engineer is looking to maximize strength while minimizing weight, the tool will run through hundreds of possible iterations of the design until it finds the right combination of parameters that meet the strength and weight requirements without affecting functionality. “It kind of replaces some human intuition with a lot of brute force calculation, but in the end it does come up with very good designs,” he says.
Goossens says Maplesoft is also getting more involved with the development of optimization tools. He says today there is a much larger set of parameters and situations to consider when optimizing a design that are not possible for a single engineer to handle. “In the past, optimization for us was very much an academic exercise, but now we’re starting to see the application of these optimization routines that can actually have a real benefit to the engineering design process,” says Goossens.
Maplesoft is currently working with Noesis Solutions to expand the capabilities of a Noesis tool called Optimus. Goossens says the two companies are working to include more optimization and Maplesoft tools within Optimus, as well as include other features an engineer may need throughout the design process such as tools to enable bill of materials to be taken into consideration while designing a product or system.
Friendlier user interfaces
How users interact with their design software is just as important as the many features it offers. “I think in terms of user interfaces, it all comes down to coming up with a paradigm for the interface that people are comfortable using in their existing workflows,” says Goossens. To achieve this, many software companies look to other software programs for inspiration when developing the user interface.
Microsoft Office products and CAD programs are the most common inspirations as these are the tools engineers use most on a day-to-day basis. Having a familiarity between products makes the software easier to use as well as minimizes the learning curve when users are new to a program or if they have long gaps of time where they do not use the software. “Anything we can do in terms of the interface to minimize that learning curve is going to be advantageous because people are going to use tools that they know how to use. Nobody likes to spend a lot of time learning and relearning new things,” says Wegienka.
In addition to using interface techniques similar to Microsoft products, Muli says dSPACE attempts to use graphical elements as much as possible. Using graphical elements reduces the learning curve as well as makes it easier to retain information and share it. “We try to use graphical methods throughout our development tool chain because of the many benefits they offer,” he says.
To make extracting information from its Virtual.Lab product easier, LMS added a Composer to the latest edition of the software program. Dan Kinne, Product Manager at LMS, says the Composer builds a custom interface that allows users to interact with models created in the software without the need to be experts in multi-body dynamics. The Composer creates an application featuring a simplified list of inputs engineers can use to quickly get the results they need from Virtual.Lab. “Prior to the Composer, if you wanted to create a simple interface to interact with Virtual.Lab, you had to do a certain level of programming and have programming knowledge,” says Kinne. With the Composer that programming knowledge is no longer necessary, and applications can be created much faster than if it were being manually programmed into the software.
LMS has also been working to add more context menus into Virtual.Lab to make the program easier to navigate. Any information related to a particular element a user may be working with will be included in that element’s context menu. “You simply right click on something and get all of the available options that are related to that feature,” explains Kinne. “That way you don’t have to be searching through menus.” He adds there is also a feature browser in the software that enables users to quickly see how different portions of a model are related to one another; users can go from one feature to the next to see how the model is set up and how it’s topology is laid out.
With component and system design becoming more complex every day, the increased capabilities and easier-to-use interfaces design software companies have added to their products—and will continue to enhance further—are helping to make the task of creating those designs a little less complex.