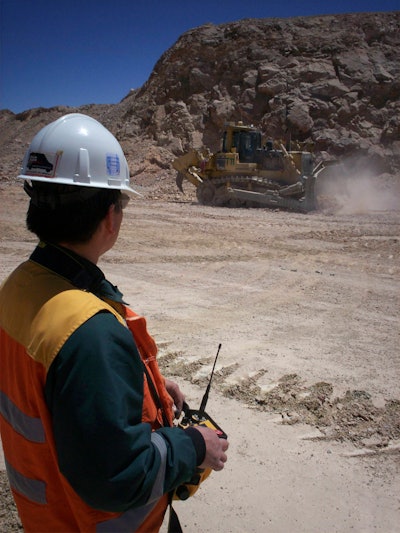
"The robotics and unmanned vehicle market is very young," says Paul Lewis, Director of Software Engineering at Autonomous Solutions Inc. (ASI, company information, 11234577), Mendon, UT. "When we started 10 years ago, the technology for GPS systems and IMUs (inertial measurement units) was much more expensive—10 times as expensive as it is now. We were working with early adopters creating their proof of concept machines. Low volume. Each product was very different. So we built modules to make it easy for us to jump from one vehicle to another. Now that the market is more mature, now that the technology is cheaper and more accessible for higher volumes, now that people are culturally willing to accept vehicles that drive themselves, now we can easily address the market needs because of those building blocks we created years ago."
ASI is a robotics company born from a Utah State University research program that set out to commercialize the product. Its Mobius Command and Control Software is the platform from which varying degrees of autonomous complexity can be built. "The way we designed Mobius was to allow the user to change a fair amount of how it looked, felt and what information was being presented to them," says Lewis. That flexibility was based on the communication protocol used to query the vehicle for its list of available telemetry items and presenting the list back to the users to allow them to choose which items were important to them.
"We're working on some next generation simplifications to make the system even more powerful and easy to use," explains Lewis. "Information is context sensitive, and an automated program should recognize a vehicle's operational context and tailor the relevant information to the user for fewer steps in a certain process, creating a better overall experience."
In the past, Mobius was more manual. A user selected a vehicle or set of vehicles, selected an action for the vehicle to take and selected where the action should take place. "What we're working on now is improved workflow," says Mitch Torrie, Director of Vehicle Automation, ASI. "Instead of selecting a specific application for a particular vehicle for a certain location, the system will automatically be able to suggest the most appropriate actions. If the suggestions are not exactly what a user wants, it is easily changed, but we're trying to make it simpler for the user to get the intention across to the software without as much manual interaction."
The reason for this ease-of-use simplification is because of the growing and changing audience by which the Mobius system is being used. Past versions of Mobius were created and tailored toward the highly technical audience that ASI was working with to develop advanced systems and proof of concept vehicles. As autonomous vehicles become more mainstream, the audience interacting with the software is less technical, so the newer versions of Mobius attempt to make the software easy to understand, showing the user only the things they care about and hiding what information is unnecessary or nonessential.
"While our early adopters were technically literate, now we're putting our systems on vehicles in countries where it may be difficult to find an operator with a driver's license, let alone high technical skills. We're trying to bring autonomy to the masses while also trying to make it accessible," says Lewis.
Safety matters everywhere
Simply put: robots save lives. That statement can be found right on ASI's website (www.asirobots.com). ASI and its Mobius system are being used by global manufacturers with safety standards that apply all over the world. Just because a country's safety standards may be more lax, that doesn't apply to the safety standards an OEM will hold themselves to corporately to protect the operator from harm while working in or around its equipment.
For soldiers and law enforcement, unmanned vehicles provide critical, real-time data giving them superior tactical advantage in dangerous circumstances. "We have vehicles that drive 24 hours a day, seven days a week and have been doing so for a long time. We have great feedback on what works and what doesn't work with the system and have logged a lot of operational hours which has increased our reliability, durability and safety abilities," says Lewis.
Areas of extreme elevation, hazardous working conditions or dangerous situations like underground mines or combat zones are not safe for human operators. Autonomous vehicles are meant to remove humans from unsafe areas, but go one step further and protect the vehicles themselves. Over the past years, ASI has added features relative to multiple vehicle coordination making the system fool-proof so the user can't assign two vehicles to drive into one another. "It has evolved from an engineering tool where the user could do almost anything to a functional system that protects the machines and operators from themselves and gets the job done faster, safer and more efficiently," says Lewis.
Often automation is seen as a means of getting rid of people (meaning fewer jobs) but that's not necessarily the case. There are several new jobs created to manage the command system, supervise networks and overall system support. The difference is that with automation, the system is accomplishing the job instead of a human operator; and the task is being done more efficiently, safely and is more repeatable than most human operators are capable.
The building block approach
"It's been an interesting path for the hardware," says Torrie. "When we left the university, our first project was controlling a John Deere tractor through the CANbus electronically. We were strictly electronic in all different markets we branched into: mining, automotive, factory automation, until a military request was made to run autonomous vehicles at high speeds for air force target practice." The request prompted ASI to create a low-cost bolt-on system, and the hardware was created in-house because it didn't exist yet.
The modularity of the ASI autonomy suite of solutions allows the system's components to be leveraged across a wide range of vehicles. "Whether an omni-directional vehicle, a skid steer or a haul truck, we can automate pretty much any type of vehicle fairly easily," says Lewis. "The core of any vehicle is the same, so it's mainly our modules that vary depending on how we need to interface with the machine." A haul truck will travel at higher speeds than a tractor, so things like object detection sensors change to accommodate the correct range and ruggedness for the vehicle's application. "It has been out of necessity with the large number of vehicles we've worked with and the differences between them that we try to combine as much usefulness as possible into our common core. This allows us to do the smallest amount of work to achieve a unique customer request."
Layer by layer
The lowest level of machine automation available is remote vehicle control. At that level, the user/operator is controlling a machine's individual joints or axes—shift gears, apply the throttle or turn the steering wheel—using a physical interface with controls. One level up is tele-operation in which the user/operator is no longer on site with the vehicle but rather in a remote location monitoring the vehicle through video, for example. "Tele-operation is similar to remote control, but instead of telling a machine to shift gears, the operator will push a joystick forward to indicate forward motion and the software coordinates the gear shift to optimize the action," explains Lewis.
Semi-autonomous mode is where a majority of ASI's customers are operating. At this level, the vehicle is tasked with a goal and the software determines how best to accomplish it while alerting the operator of any intervention needs. Full autonomy brings in a larger amount of vehicles of different types with different tasks that all need to be coordinated for an optimized, safe and productive site operation. These vehicles tend to have more obstacle detection and avoidance systems than less autonomous vehicles to give the software the data it needs to effectively operate in the more chaotic environment.
"The optimization of a larger number of vehicles doesn't have to happen all at once," explains Torrie. "The system can actively configure an optimized plan for multiple vehicles as work is being done."
Looking ahead
The autonomous vehicles market has huge potential. "We're starting to see companies from every market of vehicle manufacturing start to get involved with some level of autonomy and build it directly into their machines," Lewis says. "In the next 10 years, we're going to see a lot of unmanned vehicles come into the market, whether that market is mining, agriculture or somewhere else," he says.
"From the software side of automation, in 20 years I can see the user interface being simplified to a few charts and a slide bar to adjust the balance between efficiency and profit," says Torrie. "Users won't be dealing with the individual vehicle system anymore. Autonomous engagement will be big picture vehicle fleet monitoring and system optimization. Right now there is still a lot of manual system management and vehicle activity verification to ensure it's doing the correct task." This is a similar comparison to current factory floor operations where one man in a control room can operate several complex machines from a desk. The vehicle industry is headed in that direction, and soon there will be fleets of haul trucks to manage based on output, not individual processes.
A larger autonomous system will become useful when the software can handle multiple vehicles at a higher level, such as analyzing a system to learn more about its efficiencies, and how best to optimize a vehicle's individual work flow; then taking all of the data it has gathered, making sense of it, and forming a plan which allows managers to make big picture business decisions about it. "It's about coordination and optimizing an entire job site, not just one single activity for one machine type," says Lewis.
But the future is not without its challenges. There will always be unique situations that will arise. Those will throw a kink in the otherwise systematic approach to production. "The one-off problems are going to be the hardest to teach a system to problem-solve. Each scenario will need to have rules created to allow the system to diagnose a situation and learn how to move forward with its goal. There are always going to be things you can't anticipate," Lewis says.
So you've removed the operator, now what?
OEMs spend millions making the cab of a vehicle comfortable for a human operator. Remove the need for cabs altogether and there are a lot of design benefits that can be realized. Safety issues such as shock and vibration exposure necessitate dampers and advanced seat suspension technology to reduce health risks; without an operator to worry about, the time and money spent researching and developing those technologies would be removed. . Proper air filtration concerns and heating and cooling will be unnecessary, and visibility will no longer be an issue. "After removing a cab, an OEM could mount a much larger fuel tank on a machine, for example, and let the vehicle run for two or three days straight without needing to refuel," says Torrie.
But what if a user needs to engage with the vehicle, but now there's no cab to hop into? ASI has leader/follower technology, based on GPS or laser-to-target, to guide an unmanned vehicle to a different location. "We also have a military product called Guideline Robotic Convoy System that was created for the battlefield that uses no RF communications, nothing that can be jammed or have interference. It's a 45 mm thick Kevlar string that you attach to the leader, and the other vehicles chained to it will sense the movement, turn on, go into gear and follow it. The sensor suite measures the angle and distance traveled and plots the path of the guide vehicle and duplicates it."
Regardless of the ease of talking about complete vehicle redesigns and potential benefits, the complete removal of a vehicle's cab is probably decades down the road, depending on the speed of technological development and cultural comfort with unmanned vehicles. No matter how long it takes, the path of autonomy seems pointed toward cooperative work to embrace full-site operation optimization. "You can call it inherent intelligence, but really it's just a combination of each machine's optimal task-completion route based on the vehicle's capabilities, attachment size, most efficient rate of speed fully loaded versus empty, and several more data parameters taken into consideration," says Torrie.