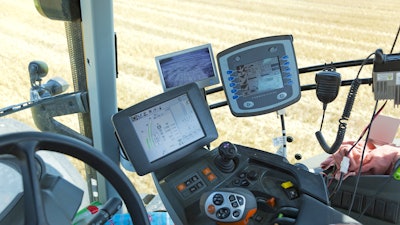
The challenge of designing off-highway vehicles is mounting as the electrical systems grow in size and sophistication. A network of electronic control units (ECUs) and sensors monitor and control the critical systems in these vehicles. ECUs monitor the temperature, pressure, and position of various components and can control the actuation of hydraulics, engine valves, and more. The increasing electrification of off-highway vehicles is similarly evident in the cabin. Agricultural tractors, for example, now feature electronic and digital controls as well as cabin amenities like heated seats and climate control systems (Figure 1).
The growth of electronic content will only continue as off-highway manufacturers invest in hybrid and full-electric powertrains. Electric powertrains contain fewer moving parts and must be serviced much less frequently than internal combustion engines. They also increase fuel efficiency and reduce the emissions of off-highway vehicles, reducing operational costs and increasing work output.
However, off-highway work is stressful for electric powertrains and electric systems. Off-highway vehicles must be able to work for long hours under extreme temperatures and in dusty, dirty environments. The work cycles of this equipment also create high charges and discharges that standard battery units are not suited to handle. Super- and ultra-capacitors are required to manage the sizable and rapid charges and discharges created by functions like regenerative braking and heavy lifting. These complex electrical systems need to be incorporated with existing hydraulic and other mechanical systems.
Meanwhile, autonomous vehicle technology is also making headway in the off-highway industry. Automated driving systems will further complicate the task of meeting safety and functionality requirements for the electromechanical design. Electrical and electronic systems will become even more sophisticated to support the array of new sensing and computing devices needed for automated vehicles. Furthermore, automated vehicles require redundant electrical systems to preserve safety-critical functions during electronic failures or accidents. These redundant systems increase the overall complexity of the vehicle design.
Wiring for the various electronic controls, modules, and systems must be routed throughout the vehicle, placing them in close proximity to mechanical systems and other electrical wiring. This introduces the potential for electromagnetic, radio, and physical interference. These and other errors, such as an improperly shielded wire, can be lost in the intricacy of the electrical and mechanical systems. Should these errors go unnoticed, equipment may operate inefficiently or malfunction in the field, causing productivity losses and safety hazards.
As the electrical and electronic content of off-highway vehicles continues to grow, the interactions between the electrical and mechanical systems will grow in step. Waiting until prototyping to validate ECAD and MCAD compatibility is not an option for today’s off-highway manufacturers. The fit and function of the wiring harness and all associated electrical components, with the vehicle frame and all associated mechanical hardware, must be ensured during the design phase.
The optimal strategy is to use a system that allows for ECAD and MCAD design data to be exchanged consistently throughout the design process. With consistent communication, ECAD and MCAD teams resolve issues early, preventing costly rework late in the design cycle. They can also optimize the vehicle design to meet evolving constraints while maintaining quality, performance, and reliability standards. Finally, ECAD and MCAD designers are able to collaborate from within their own design environments without learning new tools. Consistent and iterative communication between ECAD and MCAD teams reduces time-to-market, enables the creation of more accurate designs, and increases productivity.
ECAD-MCAD co-design: Moving from interfacing to integration
ECAD-MCAD co-design is easier said than done. Traditionally, the electrical and mechanical domains are separated; engineers work with completely different tool sets and have completely different vocabularies. Mechanical and electrical CAD systems have different ways of presenting the structure of the same object. Many times, they even reside in different physical locations.
Because of these impediments, previous efforts to collaborate have achieved limited success. Earlier ECAD-MCAD collaboration techniques used everything from sticky notes and email, to Excel® spreadsheets. These approaches fell short at enhancing the collaboration between electrical and mechanical domains because they continued to rely on manual data entry and transferal. Therefore, the accuracy of the data transferred was not assured, nor were significant time-savings realized.
As a result, many off-highway product development teams resorted to internally developed software and processes for collaboration that had to be tested and verified with each new release of the underlying ECAD and MCAD tool suites. These locally-developed software and processes were costly to maintain because they required dedicated in-house support staff to implement updates and resolve bugs as needed. Figure 2: ECAD-MCAD integration enables mechanical and electrical engineers to cross-probe between applications, providing valuable contextual information from each domain.Mentor, A Siemens Business
True co-design
The electrical and mechanical design processes benefit from being more connected, integrated, and collaborative. Cross-probing between applications serving different domains enables closer integration and collaboration, by providing each domain with contextual information from the other to leverage during design work (Figure 2).
A key feature of such integration is replacing cumbersome file-based exchanges that depend on manual exportation of a massive file of changes into a file system for the other engineers to retrieve and then import. Modern ECAD and MCAD tools support API level integrations, where the two domains are connected directly to immediately update designs with changes or new information.
With this integration, the electrical system and wiring harness can be designed with explicit knowledge of the wet, hot, and noisy areas of the mechanical design. On the mechanical side, space reservations can be made to ensure that wiring bundles will conform to minimum bend radius and diameter constraints for routing through conduits in the mechanical structures.
Furthermore, the addition of objects like clips, grommets and tubing to the harness design requires cross-domain collaboration. It is best to create these objects in the 3D MCAD environment, and then merge them with electrical data from the ECAD tool. Once this association is made, the fully buildable wiring harness can be automatically engineered in all of its configurations.
Change management
The immense complexity of modern off-highway vehicles results in hundreds or even thousands of engineering change orders affecting cable length, type, and physical placement. Managing these changes effectively is paramount to effective cross-domain collaboration.
For instance, formboard construction requires close collaboration between the mechanical and electrical domains. A mechanical engineer defines the bend radius constraints of the wire bundle, based on its physical structure and the properties of the wires it contains, to prevent deformation of the bundle from affecting performance. Once these bend radius constraints are communicated back to the ECAD solution, the formboard can be created upon which the wiring harness will be assembled. With the bend constraints from MCAD, the ECAD solution could alert the formboard engineer if they are creating a model that cannot be cost-effectively manufactured. The ECAD designer can then quickly implement necessary changes and begin formboard construction.
The challenge of change management, however, is how to track each other’s changes quickly and efficiently. There are two major aspects of change management. First is the automatic merging of data and the clear display of changes to the designer. The second critical piece is a change policy that defines the master of the data and the direction in which changes will flow.
Integrated ECAD and MCAD solutions facilitate robust and efficient change management. ECAD solutions, such as Capital, can automatically create a list of incoming design changes. This list supports live cross-probing between the electrical and mechanical designs, and can preview changes in a variety of diagrams. Also, each change can be accepted or rejected individually, giving the engineer a fine degree of control over change implementation.
A change policy allows mechanical and electrical engineers to automatically control how data is changed. Ownership over data is determined piecewise so that the change policy can be tailored to individual design flows. The pieces available for selection are highly detailed, such that rules may be set for specific attributes of individual components.
Enhanced design for vehicles doing challenging work
ECAD-MCAD co-design is a powerful strategy to increase productivity and ensure robust off-highway vehicle designs. With modern CAD tools, designers are able to synchronize their data more efficiently and collaborate more effectively on critical design items between domains, thereby ensuring that the design intent is properly implemented.
During design, integrated electrical and mechanical applications help designers understand their counterpart’s domain. Incompatibilities are identified and resolved early, reducing costly design iterations. There is added benefit in tightly coupled applications that contain design rule checks and can capture your design best practices. Imposing those best practices will ensure the electromechanical systems in off-highway vehicles are able to withstand the difficult working conditions in which they must perform. ECAD-MCAD co-design, with rich change management support, is empowering for design engineering teams as they optimize off-highway vehicle designs for reliability and performance.