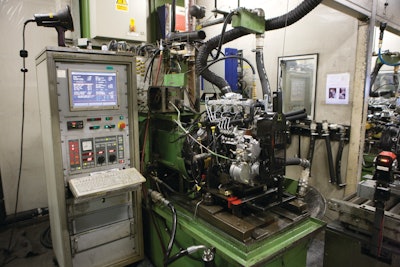
Though Tier 4 Final (T4F) regulations don’t go into effect for a few more years, manufacturers are already working to ensure they and OEMs will be ready to meet the emissions standards. Many companies, like Caterpillar Inc. and Perkins Engines Co., are preparing their manufacturing facilities for the production of the updated engines.
During a recent press event in Griffin, GA, Caterpillar and Perkins invited journalists to hear about the companies’ latest Tier 4 technologies as well as tour the facilities where the engines will be made.
Caterpillar facility
Caterpillar’s 421,000 sq-ft. Griffin facility is the global source for 3408, 3412, C27 and C32 engines, as well as several Caterpillar generator sets. Both the C27 ACERT and C32 ACERT engines produced there are currently Tier 4 Interim compliant and will be ready to meet T4F when the regulations go into effect.
Built upon Caterpillar’s Tier 2 platform, the C27 and C32 engines have the same dimensions and hookup points as its previous model to help ease the transition into Tier 4, eliminating the need to make major equipment redesigns. Both engines offer features such as an electric priming pump and enhanced electronics. Coolers on both sides of the engine help to meet emissions regulations.
At the Caterpillar facility continuous testing is an integral part of the production process to ensure each engine manufactured works properly. One method of testing is in-process validation, which occurs at various check points along the assembly line. A cold test is also performed on the engine before final attachments are affixed.
Once an engine is fully assembled and passed all tests, Caterpillar sends its engines to a second facility a few miles down the road where each engine is painted according to customer specifications.
Another key to Caterpillar’s manufacturing process is the utilization of continuous improvement boards throughout the production facility. On these boards anyone working in the facility can make suggestions for improvements. Suggestions can be made pertaining to any part of the production process, whether it’s related to safety concerns or ways work can be done more efficiently. Each suggestion is reviewed and, if deemed a positive improvement, implemented.
Since the T4F engines are so similar in design to the Interim models, Caterpillar doesn’t have to do much work to prepare its facility for the changeover. With the C27 and C32 engines, the only real change for Tier 4 is the addition of a few extra components, requiring just a couple of extra assembly steps that have already been added to the existing production process.
Caterpillar also notes that all of its facilities manufacturing Tier 4 engines will have to use ultra-low sulfur diesel as well as CJ-4 engine lube oil. The Griffin facility has already been using both for some time and will continue to do so as it produces Tier 4 engines.
Perkins facility
Down the road from Caterpillar is Perkins’ Griffin production facility. Perkins has chosen this plant to be the lead producer of its T4F 400F engine series. First released at ConExpo 2011, the 400F engines utilize a unique aftertreatment system to meet emission regulations. This aftertreatment system not only helps to reduce emissions but also replaces the need for a muffler and has various placement options to fit individual OEMs’ needs.
The 400F engine utilizes the same platform as Perkins’ 400D Series of engines with only a few minor changes. With 97% carryover of components from the previous Tier engine, the 400F will have the same footprint as the 400D engines.
Perkins chose Griffin as the lead facility for manufacturing the 400F Series due to its proximity to US OEMs. Because U.S. OEMs are the most affected by T4F regulations, the Griffin plant was a logical choice. Working directly with OEMs to ensure an engine will fit his or her specific application is an important aspect of Perkins’ business philosophy. By having the production facility in Griffin, it will be easier for Perkins to work with U.S. OEMs needing T4F engines as well as enable the company to get finished products to the customer more quickly.
The 400D engines will continue to be manufactured at the facility alongside the 400F and other Perkins engines. When the T4F regulations take effect in 2013 for horsepower range 25 to 48 engines, the 400D Series will continue to be sufficient for 75% of the world. This is one of the many reasons why Perkins’ 400D and 400F engines have so much commonality between them.
Though smaller than the nearby Caterpillar facility, Perkins’ Griffin plant is able to house all aspects of the production process in one building. Like Caterpillar, Perkins tests its engines at various stages of the production process to ensure the quality of its products. Each “quality gate” an engine stops at checks for known failure problems to ensure the engine works properly before moving on to the next assembly station.
After much of the assembly is completed, Perkins puts each engine through a “hot test” where fuel is placed into the system and tested for any possible issues. Oil testing is also performed at this stage of the production process to ensure there will be no wearing of parts. Once an engine successfully passes these tests, it moves on to be painted. Painting of the engine is completed in the same building as the rest of the production process.
Perkins is currently working to prepare its Griffin plant for the additional production of the 400F Series. With the new engine, a few more assembly stations and machines must be added to the current manufacturing line. The company expects to have the new machines in place by the end of the year so production of the 400F can begin as quickly as possible.
By readying their facilities now for the eventual implementation of T4F, Caterpillar and Perkins will be better able to meet the supply demand of their OEM customers once the regulations go into effect.